How is a PCB manufactured?
The PCB manufacturing process transforms design files such as Gerber/ODB++/IPC-2581, netlists, and drill files into a physical circuit board.
It begins with product conceptualization, schematic entry, layout design, and production file generation.
The bare board is fabricated once the printed board design files are finalized. Next, the components are assembled on the board, followed by comprehensive functionality testing.
Step-by-step PCB manufacturing process
Step 1: Pre-production engineering
The PCB manufacturing commences after receiving the design files from a PCB designer or an electrical engineer. The files include:
- Gerber or ODB++ or IPC-2581 files (used for fabrication).
- Bill of Materials (BOM) (used for assembly).
This stage involves:
- DFM checks: It is performed to identify potential errors that might arise during the PCB fabrication process. In case of any errors, the designer/client is alerted about it.
- CAM processing: Corrected files are fed into computer-aided manufacturing (CAM) software, which recognizes layer formats, drilling data, and IPC netlists and converts the electronic data into images. It also verifies the layer order sequence, runs design rule checks (DRC), and performs many other operations.
- Output file generation: The CAM system generates essential files for manufacturing, including drill program (sub drill and main drill), imaging layers, solder mask file output, route file, and IPC netlist.
Download our eBook to learn how to design a manufacturable PCB.
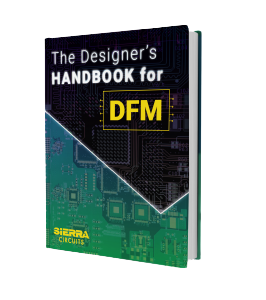
Design for Manufacturing Handbook
10 Chapters - 40 Pages - 45 Minute ReadWhat's Inside:
- Annular rings: avoid drill breakouts
- Vias: optimize your design
- Trace width and space: follow the best practices
- Solder mask and silkscreen: get the must-knows
Download Now
Step 2: Inner layer imaging
With the increasing miniaturization of electronic components, fabricators primarily rely on laser direct imaging (LDI) for precise circuit patterning.
Here are the steps involved in LDI:
- Photoresist application: A layer of photo-sensitive film (photoresist) is applied to the board. This film contains photo-reactive chemicals that undergo polymerization upon exposure to ultraviolet (UV) light.
- Laser direct imaging (LDI): The panel is positioned under a computer-controlled laser that selectively hardens the photoresist, forming the desired circuit pattern.
- Development and processing: The unhardened (unexposed) photoresist is removed with an alkaline solution, leaving the protected copper intact.
The LDI workflow is shown in the image below:
Step 3: Etching
Etching is a crucial step in the PCB manufacturing process, where the excess copper (non-circuit copper) is removed from the board to reveal the desired circuit pattern.
It typically takes place in a conveyorized develop, etch, and strip line. Here, the board moves through the chamber while being sprayed with the various chemicals to ensure consistent developing and etching to achieve the desired results.
Key parameters to monitor during etching include:
- Well-maintained chemistry within the specification.
- Panel movement speed
- Proper spray pressure and distribution of the chemical solution based on the resist height and the amount of copper to be etched.
Proper control of these factors is essential for achieving precise and clean circuit patterns on the PCB.
Step 4: Photoresist stripping
In this process, the residual photoresist is etched away from the copper surface. The process involves dissolving caustic pellets (chemical agents) in water combined with a high-pressure water rinse, which breaks down and washes away the remaining photoresist.
Step 5: Inspection and post-etch punch
Once all layers are cleaned and prepared, we perform a post-etch punch to ensure precise layer-to-layer registration. Using alignment targets on the inner layers, the boards are placed into an optical punch machine that accurately aligns both the inner and outer layers.
Following this, inspection is carried out through visual scanning of the board surface using an automated optical inspection (AOI) system. The circuit board is illuminated using various light sources, while high-definition cameras capture detailed images. The AOI system then analyzes these images to verify accuracy and detect any defects.
Step 6: Alternative oxide coating
Here, the copper circuit pattern is coated with an alternative oxide coating, primarily used as an adhesion promoter. It also helps prevent oxidation and corrosion of copper.
Step 7: Lamination
Lamination is the process of bonding copper foil, prepreg, and inner layer cores under controlled temperature and pressure to form a multilayer PCB.
The lamination process consists of two main steps:
- Stack-up preparation: Carefully arranging the layers (copper foil, prepreg, and cores) in a symmetrical configuration.
- Bonding: Applying heat and pressure using a mechanical press to fuse the layers together. The bonding is done in two stages: hot pressing and cold pressing.
A computer-controlled bonding press regulates the stack-up heating, pressure application, and controlled cooling of the stack to ensure optimal bonding quality.
Sierra Circuits specializes in high-precision PCB manufacturing in the USA, utilizing advanced tools like X-ray drill machines, mechanical vision drill systems with controlled depth, laser drilling, and Seica FPT machines to ensure the highest precision.
Check out our rigid PCB manufacturing capabilities to learn more.
Step 8: Drilling
During this stage, holes are created for vias and solder leaded components. A computer-controlled X-ray drill is used to accurately locate target points within the inner layers and drill precise registration holes. Operators can select specific drill programs, allowing the machine to position itself accurately along the X-Y coordinates.
The system is capable of drilling holes as small as 125 microns in diameter. The machine automatically selects the drilling parameter for material/stack-up.
Drilling can produce burrs. These are removed during the deburring process, which cleans the surface of the board and eliminates any impurities. Laser drilling is commonly used in high-speed PCB manufacturing to create precise vias that support high-frequency signal performance.
For more, see PCB drilling explained: the dos and don’ts.
Step 9: Metallization of the dielectric
During this step, the walls of the drilled holes are made conductive through electroless copper deposition. It is a chemical process that coats both the hole walls and the panel surface with a thin layer of copper.
Here are the steps involved in the metallization process:
- Surface preparation and cleaning: The PCB panel undergoes a thorough chemical de-smear process to remove the possibility of any epoxy smear from the hole walls, debris, and oxidation from the hole walls and surface. Plasma is also used for various types of de-smear, etch back, and activation processes.
- Catalyst activation: A palladium-based catalyst is used to initiate an electroless deposition process.
- Electroless copper deposition: The panel is immersed in an electroless copper bath where a controlled auto-catalytic reaction deposits a uniform copper layer on the hole walls as well as the surface of the panel. According to IPC class 2 requirements, the final copper thickness (after plating) in vias must be at least 0.0008 inches (20 microns).
- Coverage: The thin copper coating forms a continuous conductive layer along the hole walls and over the surface, enabling subsequent electroplating and circuit formation.
Download our eBook to learn how to select the right materials for your circuit boards.
PCB Material Design Guide
9 Chapters - 30 Pages - 40 Minute ReadWhat's Inside:
- Basic properties of the dielectric material to be considered
- Signal loss in PCB substrates
- Copper foil selection
- Key considerations for choosing PCB materials
Download Now
Step 10: Outer layer imaging
This step utilizes photoresist, similar to the inner layers, but involves a positive image and follows the print-plate-etch method.
The key steps are:
- Panel cleaning: To ensure proper adhesion and imaging quality, the panels are thoroughly cleaned to eliminate any dust or contaminants.
- Photoresist application: A uniform layer of photoresist is applied over the cleaned panel surface, preparing it for imaging.
- Laser direct imaging (LDI): The circuit pattern is digitally printed onto the photoresist using LDI. This method ensures precise alignment and definition, as it directly corresponds to the CAD/CAM design.
Step 11: Copper plating
In this step, the holes and surface are electroplated with copper to ensure electrical connectivity between the layers of a printed circuit board.
Below are the key stages of the copper plating process:
- Pre-plate cleaning: Prior to plating, the panels are cleaned and activated in a sequence of chemical baths to ensure optimal surface condition.
- Electroplating setup: During electroplating, the panels function as cathodes in an electrolytic cell. Soluble anodes are typically used to supply current and copper replenishment to the bath. Since the holes already contain a thin, conductive layer of copper (deposited during the earlier electroless copper processes), they can now be electroplated. Copper is deposited onto both the surface and inside the hole walls.
- Controlled copper deposition: Rectifiers with precise power controls are used to ensure the copper is evenly deposited across both the hole wall on the surface of the panel.
Copper plating in PCB fabrication. - Tin plating: Following copper plating, a tin layer is electroplated onto the surface. It prevents corrosion of surface features such as copper pads, hole pads, and hole walls during the etching of the outer layer.
Tin plating during printed board fabrication.
Step 12: Photoresist stripping
Once the panel is plated, the photo-resist will be stripped off to expose the unwanted copper.
A single continuous process line is used to dissolve and wash off the photoresist that covers the copper areas intended for removal. This step ensures that the panel is properly prepared for the subsequent etching phase.
Step 13: Final etching
In this stage, the unwanted exposed copper is chemically removed using an ammoniacal etchant. The areas of copper protected by a tin layer remain intact, as the tin acts as a resist against the etching solution. This process precisely defines the conducting paths and establishes the final circuit connections on the board.
For more, see wet PCB etching using acidic and alkaline methods.
Step 14: Tin stripping
Post etching, the protective tin layer present on the copper tracks is removed. This is achieved using concentrated nitric acid, which effectively dissolves the tin without damaging the copper underneath. As a result, a clean and well-defined outline of the copper tracks becomes visible on the PCB surface.
Try our Better DFM tool to thoroughly verify design for manufacturing aspect of your PCB design.
Step 15: Solder mask application
Solder mask in PCB serves the following purposes:
- It provides insulation resistance to the traces.
- Distinguishes solderable and non-solderable areas.
- Provides protection against environmental conditions by covering non-solderable areas with ink.
The application process typically involves the LPI (liquid photo imageable) mask, which allows precise and uniform coverage across various board surfaces. Here’s an overview of the process:
- LPI coating: A liquid photo imageable mask composed of solvents and polymers is applied to the board surface, forming a thin, photo-sensitive layer that adheres to various board surfaces.
- Imaging: The coated panel is imaged using a printer system. A UV lamp in the machine exposes the transparent areas of the design, hardening the mask in those regions.
- Developing: The unhardened (unexposed) ink is chemically stripped from the board, leaving only the desired mask pattern.
- Curing (drying): The mask is cured to chemically bond the ink with the dielectric material, enhancing adhesion.
- Final baking: As a final step, the board is baked in an oven or under infrared heat to fully dry and harden the solder mask, completing the process.
This process ensures the resistive layer is accurately aligned and fully integrated with the circuit board structure.
Green became the standard solder mask color because it doesn’t strain the eyes. Before automated inspection systems were introduced, PCB inspection was done manually. The overhead lighting used by technicians did not reflect as harshly off the green mask, reducing glare and making it safer and more comfortable for extended visual inspections.
Step 16: Surface finish
PCB surface finishes form intermetallic joints between the bare copper on the solderable areas of a circuit board and its components. The base copper is highly susceptible to oxidation without a protective coating, so applying a surface finish is essential to prevent corrosion. Additionally, the surface finish prepares the board for soldering during assembly and helps extend its shelf life.
Lead-free PCB manufacturing demands surface finishes that can withstand higher processing temperatures and meet environmental compliance standards.
There are various types of surface finishes available. However, lead-free surface finishes are widely used in PCB fabrication process due to the strict RoHS (restriction of hazardous substances) norms.
Table 1: Classification of surface finishes
Type | Surface finish | Description |
---|---|---|
Metallic | HASL (hot air solder leveling) | Solder coating by dipping in molten tin-lead solder and removing excess with hot air. |
Lead-free HASL | Variation of HASL using RoHS-compliant lead-free solder alloys like Sn/Ag/Cu. | |
ENIG (electroless nickel immersion gold) | Thin gold over nickel layer to prevent copper oxidation. | |
ENEPIG | Combination of nickel, palladium, and gold for high solderability and oxidation resistance. | |
Hard gold | Thick, durable gold plating over nickel, used in high-wear areas like edge connectors. | |
Soft gold | Primarily used for wire bond pads or where a thicker gold deposit is required. | |
Immersion silver (ImAg) | Lead-free silver coating that protects copper through an immersion reaction. | |
Immersion tin (ImSn) | Thin tin layer on copper, suitable for fine-pitch and RoHS-compliant boards. | |
Organic | OSP (organic solderability preservative) | Water-based organic coating to protect copper until soldering. |
While choosing a surface finish, consider the factors such as cost, environment, component selection, shelf life, and production volume.
Step 17: Silkscreen
In this process, inkjet projectors are used to image the legends directly from the board’s digital data.
The ink is spread on the surface of the panel using a jet printer. The panels are then baked to cure the ink. It designates different kinds of text such as part number, name, code, logos, etc.
There are two types of silkscreen printing:
- Manual screen printing
- Direct legend printing
Step 18: Electrical test or E-test
E-test refers to bare board electrical testing. In this step, electrical probes are used to check for shorts, opens, and netlist integrity.
This test verifies the electrical conductivity of the circuit board using the netlist file, which contains information about the PCB’s intended interconnection patterns.
Flying probe testing
Flying probe tests in PCB are implemented to test for functionality. The test is done using probes that move from one point to another based on instructions provided by specialized software. It is a fixtureless test method.
Initially, flying probe test (FPT) programs are created and then loaded into the FPT tester. The tester applies electrical signals and power to the probe points and measures the results according to the test program.
Step 19: Routing and v-scoring
Circuit boards are profiled and cut out of the production panel during the final stage of the PCB manufacturing process. This is typically done using either a router or a V-scoring machine.
The V-groove method cuts diagonal channels on both sides of the board, while the router leaves small tabs along the borders. In either case, the boards can be easily popped out from the panel.
Use our Stackup Designer to quickly create a manufacturable build-up.
Have questions on printed board fabrication? See our PCB manufacturing FAQs for quick answers.