A PCB surface finish protects the circuit from any damage due to harsh operating and storage environments. Selecting the right coating plays an important role in enhancing the board’s solderability, and shelf-life.
Why do you need a surface finish on a circuit board?
The surface finish is a coating between the bare copper at the solderable area and the components on the circuit board. It protects the copper surface from oxidation. During assembly, the surface coating prepares the board surface for soldering components.
Types of surface coating
Surface coating for printed circuit boards can be classified broadly into metallic and organic.
Metallic surface finishes
Metallic surface finishes use metallic layers. Some examples of these finishes are discussed below.
Hot air solder leveling (HASL)
HASL is a traditional surface finish. In this method, the board is dipped into a molten solder bath to encase all the exposed copper surfaces with solder. The extra solder is removed by passing the circuit board between hot-air knives. The solder used here is a mix of tin and lead. HASL can make a device drop-resistant.
Lead-free HASL
Lead-free HASL is identical to the HASL method. The only difference is that the solder is made up of a lead-free alloy such as Sn-Cu-Ni-Ge, Sn-Ag-Cu (SAC), and Sn-Cu-Co.
Electroless nickel immersion gold plating (ENIG)
ENIG refers to electroless nickel plating covered with a thin coating of immersion gold.
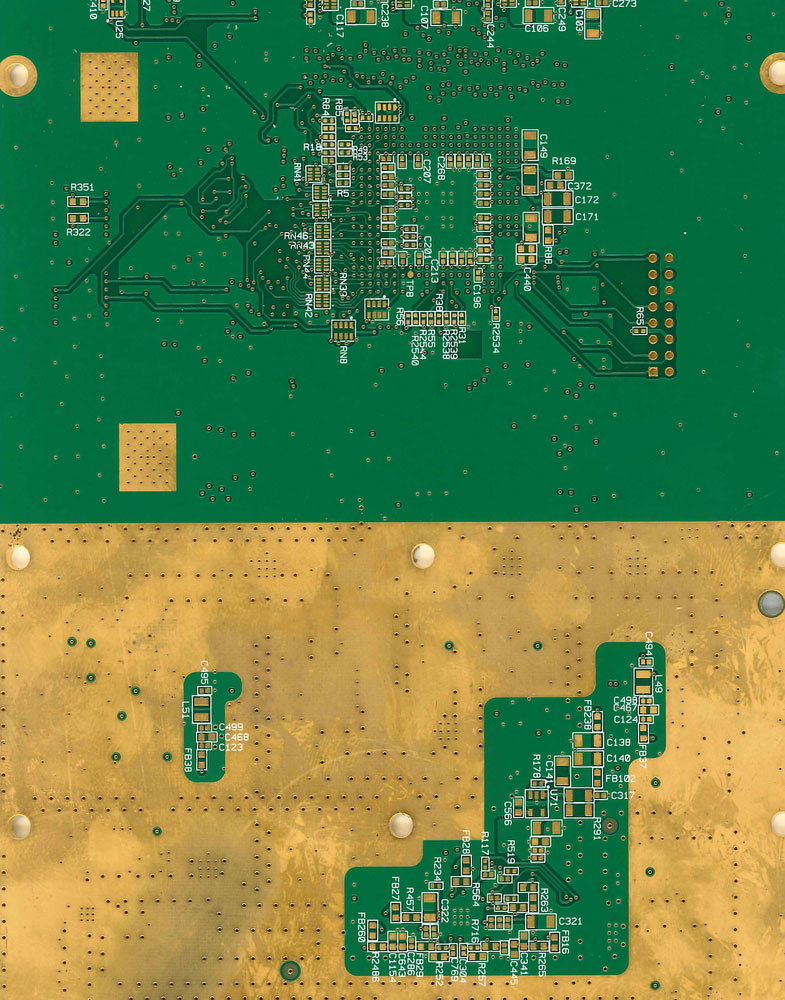
Electroless nickel deposition is an auto-catalytic process. Here nickel is deposited on the copper surface which is catalyzed using palladium. To obtain a consistent coating, the reducing agent that contains nickel ions needs to be restored. This also provides a proper concentration and temperature for plating. Subsequently, gold will adhere to the areas that have nickel plating. ENIG can be used to protect medical devices from shock and drop issues.
Design for Manufacturing Handbook
10 Chapters - 40 Pages - 45 Minute ReadWhat's Inside:
- Annular rings: avoid drill breakouts
- Vias: optimize your design
- Trace width and space: follow the best practices
- Solder mask and silkscreen: get the must-knows
Download Now
HASL vs. ENIG: Which surface finish is better?
Parameter | HASL | ENIG |
---|---|---|
Type of metal coating | Lead variant: tin-lead solder Lead-free variant: tin with small amounts of silver and copper | Nickel and gold |
Plating thickness | A thicker solder layer is plated | A thinner gold layer is deposited |
Adhesion to copper | The solder layer in HASL adheres well to the copper pads due to the metallurgical bond formed during the soldering process | The nickel layer serves as a barrier between the copper and the gold, ensuring good adhesion between copper-nickel and nickel-gold |
Thermal stress | Chances of damage are high since the board is exposed to a higher temperature during hot-air knives process | As the process does not require high temperature, it reduces the risk of warping |
Electrical performance | Lower electrical performance compared to ENIG | Since gold is a better electrical conductor than tin, it enhances the electrical performance |
Flatness | Can create an uneven surface due to the thickness of the solder layer | Provides a smooth surface finish |
Solderability | Provides good solderability for manual soldering and simple assembly process | Compatible with all advanced and automated soldering techniques |
Component compatibility | Suitable for both through-hole and SMT components. However, the thickness of the solder layer can create bridges between adjacent pads and cause issues in fine-pitch component placement | Allows all types of component placement. It is preferred for fine-pitch and wire-bond components, as the thin gold layer does not create any bridging issues |
Operational environment | Not recommended for harsh environments | Can withstand harsh environments |
Cost | Cost effective due to its simple process and lower material costs | Expensive as it undergoes the gold immersion processes |
Shelf life | Lower shelf life as it can be oxidized and corroded over time, leading to solderability issues | Longer shelf life as the gold layer provides protection against oxidation and corrosion |
Eco-friendly | The HASL lead variant is not eco-friendly. It can cause health and safety issues in the working environment | ENIG is environment safe |
RoHS compliance | The lead variant does not comply with RoHS regulation | Adheres to RoHS regulation |
Electroless nickel electroless palladium immersion gold (ENEPIG)
ENEPIG is similar to ENIG. The difference is a palladium coating is implemented as the protective layer to prevent nickel oxidation and stop diffusion to the copper layer.
ENIG and ENEPIG provide great solderability at a higher cost compared to other surface finishes.
Hard gold
Hard gold includes a gold layer that is plated over a nickel coating. The hard gold finish consists of gold alloying with nickel, cobalt, or iron. It is best suited for components with a higher risk of wear and tear such as edge connectors, interconnected carrier boards, contacts, and keypads.
Immersion silver (ImAg)
Immersion silver surface finish provides a lead-free layer of silver and protects the copper traces from corrosion. An electroless immersion reaction is used to apply ImAg to the copper traces.
Immersion tin (ImSn)
Immersion tin surface finish consists of a thin layer of tin. It is RoHS-compliant and a great choice when it comes to small geometries and components. It is also well-suited for flat surface requirements and fine-pitch components.
These are all the commonly used metallic surface finishes. Now let us take a look at the organic ones.
Organic
An organic finish includes organic compounds (compounds with carbon). Some of the popular ones are listed below.
Organic solderability preservative (OSP)
OSP is a water-based organic finish used for copper pads. It protects the copper pad prior to soldering.
Carbon ink
This consists of a layer of carbon ink. This method is used in welding equipment, remote controllers, automotive, keyboards, keypads, and RF shielding. The primary factors involved in board production with the carbon ink surface finish are printing, baking, and resistance control.
Choosing the right surface finish for a board
Selecting the right surface finish is essential since it decides the reliability of the board. Some important factors to keep in mind while choosing a surface finish are as follows:
- Operating environment
- Board aesthetics
- Shock and drop issues
- Corrosion
- Presence of fine pitch components (BGA)
- Flatness of SMT pads
The types of surface finishes available at Sierra Circuits are listed below: