Contents
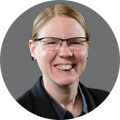
On-demand webinar
How Good is My Shield? An Introduction to Transfer Impedance and Shielding Effectiveness
by Karen Burnham
When manufacturing a circuit board, one of the most critical aspects is printing and etching the layout on the copper-clad laminates. The imaging process is central to creating a PCB layout and defines the circuit traces. While the conventional imaging process needs a photo-tool film, and UV light to transfer the images, LDI uses a computer-controlled laser beam to directly define circuit paths onto the board.
Laser Direct Imaging (LDI) process
Laser Direct Imaging is the next step in the evolution of the PCB photolithography process. Unlike photo exposure, LDI does not employ a phototool. It directly exposes a digitally saved pattern onto the resist. Photoresist is selectively exposed to the laser beam in increments across the substrate in a rastering manner. The image formed can be compared to the image on a CRT screen, formed from several lines across the screen. Similar to photolithography, LDI requires a photo-resist, although the resist is specially created for laser printing as LDI resist is fast-acting compared to conventional photo-resist. LDI resist comes in dry film and liquid options with the resist application methods being identical to those used in photolithography.
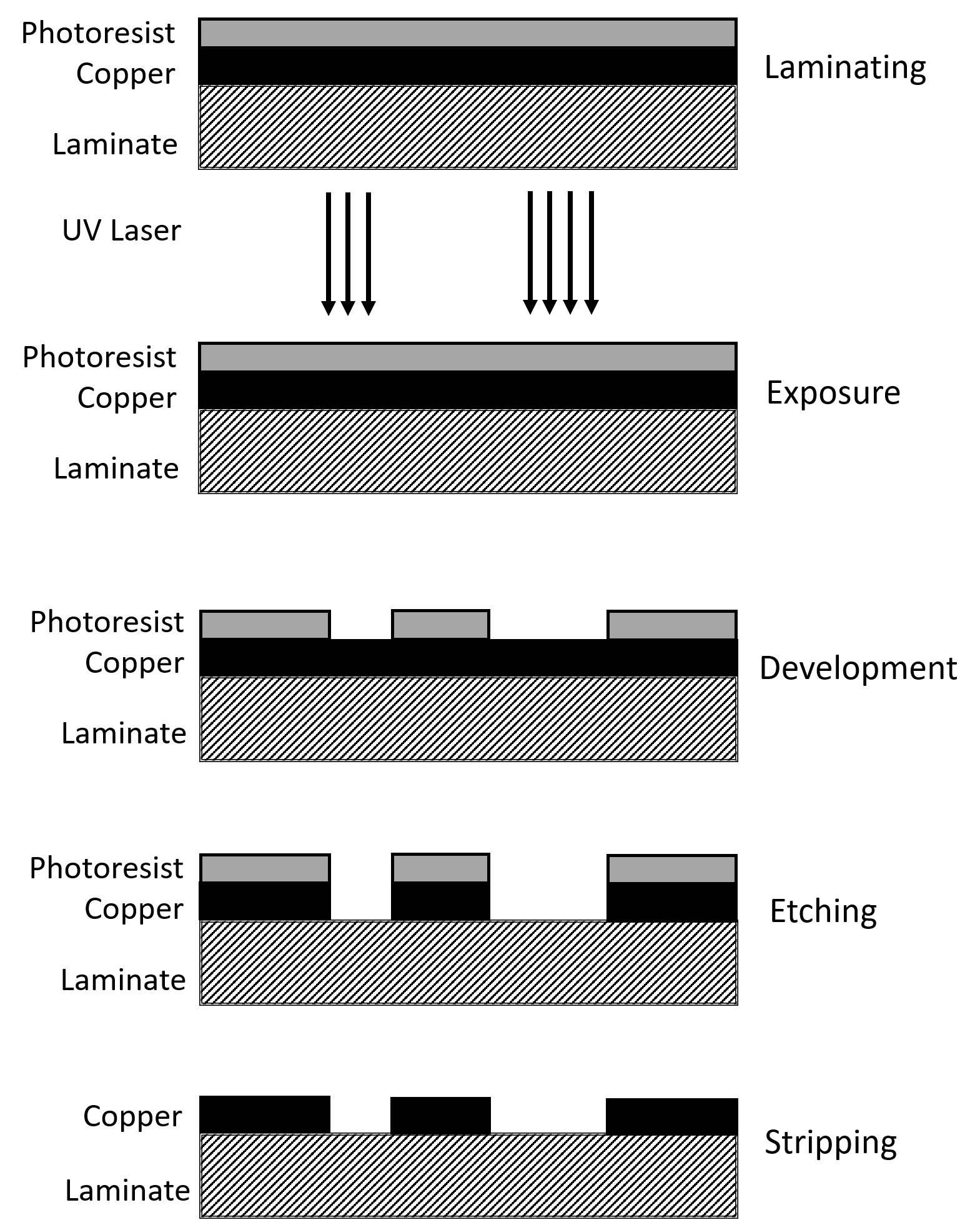
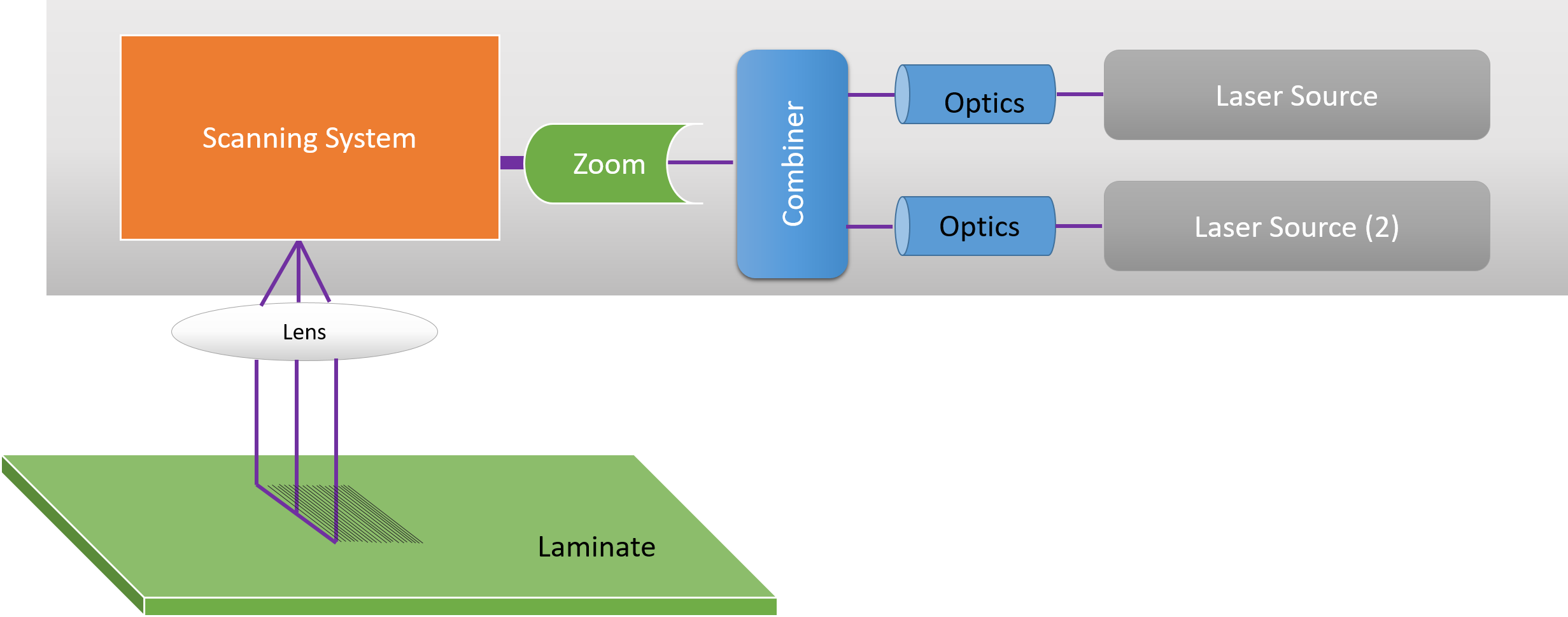
Here are the steps used in the LDI process:
Scrubbing
This includes removing any oxide layers on the core surface using anti-oxidant baths and mechanical scrubbing with abrasive pads. Sometimes Isopropyl alcohol is used to remove any organic residues and oil on the core surface.
Lamination Photoresist
The PCB panel is coated with a layer of photosensitive material.
Loading CAM files
CAM files are then loaded into the laser.
Laser printing
The circuit pattern is printed onto the board by the CNC laser.
Etching
Areas of photoresist material that weren’t exposed to the laser beam are etched away using acid leaving behind the desired circuit paths/traces.
Photoresist strip
Removal of the photo-sensitive material
Drying
Drying the core/CCL after removal of photo material
Advantages of LDI over Photolithography
The major reason LDI is preferred by PCB manufacturers, especially for HDI circuit fabrication is that it eliminates the phototool. Given below are the reasons why laser direct imaging is favored over conventional photolithography:
- There are costs associated with the storage and preservation along with tracking and continuous inspection of a phototool that LDI eliminates.
- A phototool/film is affected by dirt, fibers, smears, and scratches which can degrade the phototool and decrease the effectiveness of creating the required circuit pattern.
- A phototool is affected by the diffraction of light even under ideal conditions
- Photo tools are affected by temperature and humidity variations that can end up distorting the original image.
- There are greater limitations in phototool alignment with regard to the substrate. Flexible circuit substrates may undergo dimensional changes when subjected to processing. In this case, a static phototool can be used to achieve a “best fit”, whereas in LDI the image pattern is precisely adjusted through the computer software for an exact fit, accommodating the dimensional changes. This is important for multilayer circuit fabrication where printing of traces, vias, and other features is critical.
LDI layer registration
In laser direct imaging, the patterns of the Gerber file are directly exposed to the photoresist film and laser beam. This creates a sharp image of the circuit. The layer registration is conducted with the help of colliding laser beams from the top and bottom sides of the board. In this method, there will be always zero-zero registration, which means the beams are perfectly aligned. Now depending on the flatness of the board, the variations can be up to 5-microns.
Under the traditional photolithography imaging process, films are implemented in photo tools. Films have a glass tray where the tooling holes are distributed and the same tooling holes are punched on the films and the registration takes place. The tooling holes control the top and bottom layers.
Let’s compare these two methods:
Quality: Photolithography method results in poor quality images due to fluctuation in temperature and humidity. Laser imaging results in more precision and consistent imaging as compared to photo methodology. Enhanced resolution, precision positioning, perfect alignment, and image trace widths are factors where LDI surpasses.
Environmental impact- Photolithography involves temperature and humidity-controlled environments whereas LDI does not have any environmental impacts on resulting images.
Variation- In this photolithography registration, when you plot a film from Gerber data, there will be a 5-micron variation. During the transition from the film to the board will lead to 10–15-micron variations due to board warpage and tooling tolerances. In total, there will be 15–20-micron variations. In LDI registration, there will be a 5-micron variation depending upon the flatness of the board.
PCB photolithography/UV lithography
PCB fabrication has been dependent on the conventional photolithography process for quite some time. In traditional photolithography, a photographic mask called a phototool is created from a drawing and placed on a panel covered by photoresist. The photoresist will then be exposed to a UV light source to harden/develop after which the PCB panel is etched with chemicals to retain the circuit pattern.
While generating the phototool itself is a time-intensive, multistep process, automated exposure systems set with a 5-second exposure time can generate up to 150 panels per hour.
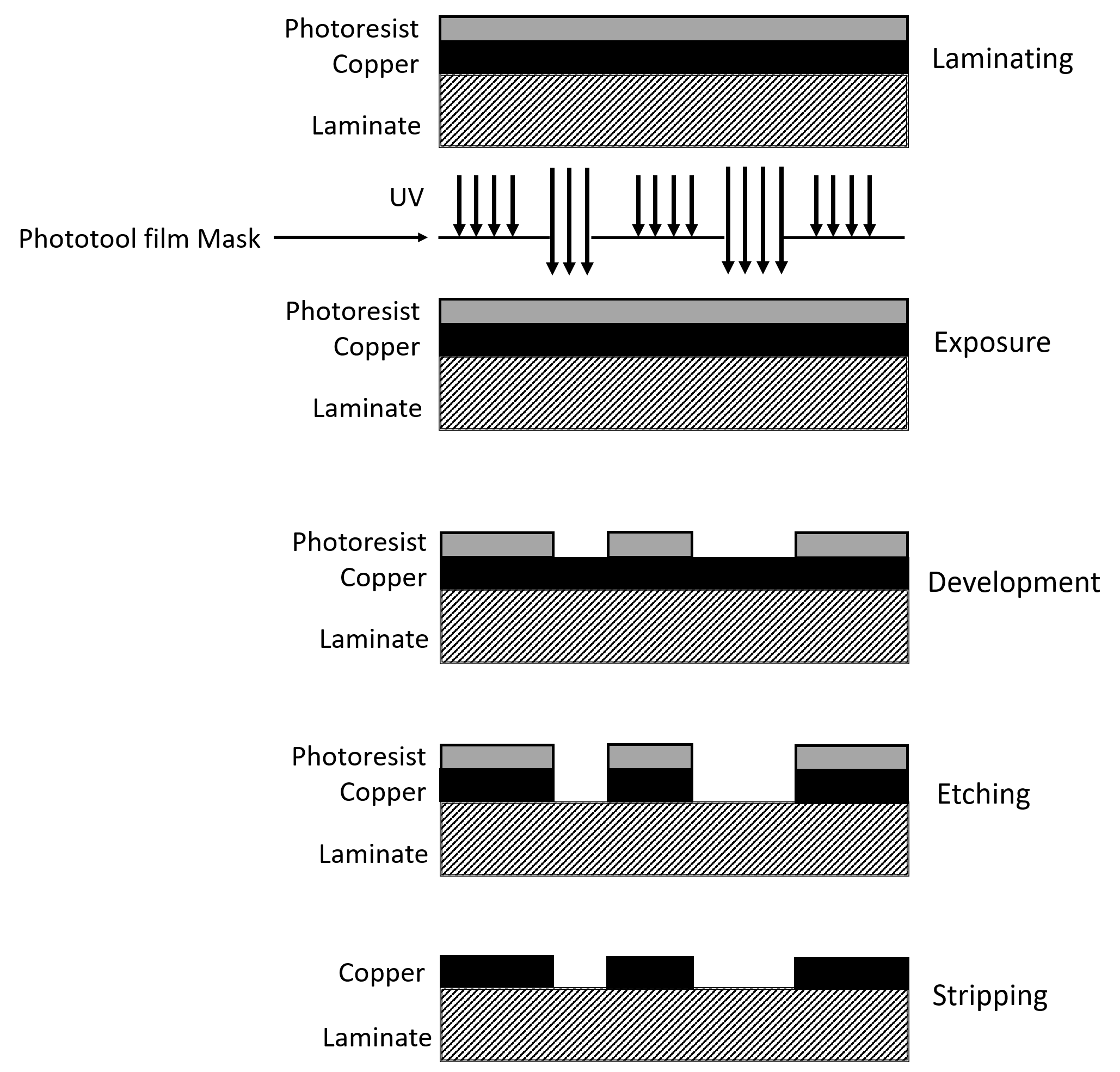
Here is a sequence of steps undertaken in conventional PCB photolithography to print a circuit pattern on a PCB:
Scrubbing
Surface preparation for the cores is done similar to the process mentioned in LDI.
Lamination photoresist
Photosensitive film called photoresist is placed on core surfaces at 75-80 °C to bind it to the core surface. This phase is also called creating a presensitized PCB, as the surface of the PCB is made sensitive to UV light exposure.
What is the difference between positive and negative images?
Positive image
When using positive image UV light is made to hit the material in the regions where the copper must be removed. Once the positive image is exposed to the UV light, the photoresist becomes more soluble in the photoresist developer solution. This will leave behind an identical copy of the pattern.
Negative image
When using negative image UV light is made to hit the material in the regions where copper must be retained. The region exposed to UV light polymerizes and hardens, so that the developer solution will wash away the unexposed photoresist regions. This will leave behind an inverse copy of the pattern.
Exposing
Exposing the photo material to UV light. This will harden the exposed portion of the photo-resist material. Later the remaining unhardened photo-resist material will be etched away using chemicals.
What is the function of UV exposure in PCB fabrication?
UV light causes a change in the photoresist material, which causes it to harden or become more soluble depending on whether it is a negative photoresist or a positive photoresist respectively.
Developing
This involves using chemicals to induce reactions in the photo-sensitive film and cause it to dissolve. Usually, the developer solution is a 1% solution of Sodium Carbonate (Na2CO3) or Potassium Carbonate (K2CO3). Both solutions yield similar results, except that Potassium Carbonate is known to give slightly better quality results with regard to developing.
Automatic Optical Inspection (AOI)
This involves checking the existing CCL against circuit patterns that are present in the system. AOI inspection process involves scanning the board surface. The AOI equipment includes one or more high-definition cameras that capture images of PCB surface using several light sources. The images are then compared in real-time with required board patterns using built-in processing software. The full process can be carefully monitored throughout.
Etching
This is a process where unwanted copper on the board is removed. Copper covered under dry film remains. PCB manufacturing processes use solvents like ferric chloride, cupric chloride, ammoniacal etchant, sulphuric and chromic acid, alkaline etchants, and copper ammonia complex ion as etching fluids.
Photoresist strip
Removal of the photo-sensitive material
Drying
Drying the core/CCL after removal of photo material
Also Read: PCB Cross-Section Analysis: A Microscopic Visual Validation of PCBs
Laser Direct Imaging is the next step in the evolution of the PCB printing process. Even though it is more expensive than conventional photolithography, it is invaluable in the manufacture of high-precision PCBs and prototype boards. The adoption of LDI in PCB manufacture is increasing and showing no signs of slowing down.
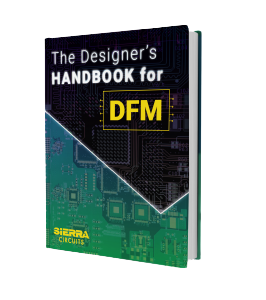
Design for Manufacturing Handbook
10 Chapters - 40 Pages - 45 Minute ReadWhat's Inside:
- Annular rings: avoid drill breakouts
- Vias: optimize your design
- Trace width and space: follow the best practices
- Solder mask and silkscreen: get the must-knows
Download Now
Quote and order your circuit boards online with our Turnkey PRO tools in just a few minutes.