What is HDI technology?
As per IPC-2226, high-density interconnect (HDI) boards have a higher wiring density per unit area than conventional PCBs. Thus to achieve this, as a designer you need to opt for smaller vias, smaller traces, and fewer layers. These PCBs have components packed in a small space to achieve the required formfactor.
These PCBs use different via technologies like microvias, blind and buried vias, and built-up laminations. Implementation of this, frees up space for additional components and offers more routing versatility.
Earlier in conventional board design, to add more components, more layers would have to be introduced. Also, only one type of connectivity was available. But with the emergence of HDI, more sub-connectivities are introduced between layers. This reduces the number of layers and makes the boards more compact. Compact boards with reduced thickness will have a smaller aspect ratio and increased reliability. These boards have thinner trace width and a reduced drill-to-copper ratio. Due to the short distance connections and lower power requirements, the signal integrity of these boards are better than conventional PCBs.
Sierra Circuits is the nation’s top HDI PCB manufacturer — with expert engineering and rigorous testing to deliver full turnkey HDI PCB assemblies guaranteed to work.
Learn more about our capabilities for HDI PCBs.
HDI layout design
An HDI layout design consists of more components, microvias, thinner traces, and lower signal levels. The selection of components for these boards is equally important.
SMD components with high pin counts and BGA components with low pitches (typically ≤0.65mm) can be helpful in reducing trace widths.
The microvias should be filled/capped for a planar copper surface. Via-in-pads with offset design will help to acquire more space for wiring. The total connection length required to connect all the parts is called the wiring demand. The wiring length available to connect all these parts is called the substrate capacity. In high-density interconnect boards, the substrate capacity should always be larger than the wiring demand.
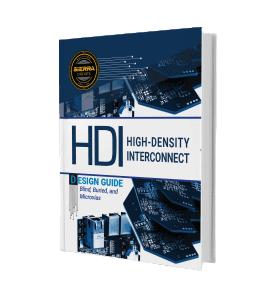
HDI PCB Design Guide
5 Chapters - 52 Pages - 60 Minute ReadWhat's Inside:
- Planning your stack-up and microvia structure
- Choosing the right materials
- Signal integrity and controlled impedance in HDI
- Manufacturing considerations for higher yields
Download Now
High-density interconnection structures
There are two basic HDI structures: build-up/sequential laminations and any-layer structures/every layer interconnect (ELIC). In sequential lamination structure, the cores are constructed, laminated, drilled, plated, and filled first. This layer is then laminated with the other layers and later drilling, plating, and filling processes are repeated.
In any-layer structure, all the layers are interconnected. This allows the conductors of any layer to be interconnected freely with copper-filled stacked microvia structures. This structure is used in complex large pin-count devices.
Manufacturing considerations for HDI printed circuit boards
- Number of laminations: The number of laminations used in the stack-up is the most important factor when it comes to HDI manufacturing. This in turn decides the cost of the overall board.
- Choosing laser drilling over mechanical drilling: Laser-drilled vias will reduce cost, time, and are effective for controlled depth vias.
- Aspect ratio of laser drill: The aspect ratio of the drilled vias should be smaller for easy plating and good thermal properties. This is achieved by choosing microvias that generally have an aspect ratio less than 1. The ideal value is 0.75:1.
- Drill-to-copper: Drill-to-copper is defined as the distance between the edge of a drilled hole and the nearest copper feature. Design automation tools do not take into account the drill-to-copper clearance. While designing for HDI, the drill-to-copper capability of a manufacturer needs to be considered. The typical value of drill-to-copper clearance is 7 to 8 mils.
- Landless via technology: Using laser drilling, it is possible to drill vias with no pads at all. This is called landless via technology. Implementing this technology reduces the size of the board even more.
- Choosing the right surface finish: ENIG or ENEPIG surface finishes are preferred over hard or soft gold for high-density boards.
See our FAQ on HDI PCBs.
Benefits of HDI boards
Here are a few benefits of using HDI printed circuit boards compared to conventional PCBs:
- Reduces board space (form factor) requirement: The compact design due to the use of microvias, blind vias, and buried vias reduces the overall board space.
- Signal integrity improvement: Since the components are placed closer to each other, the signal path length is reduced, thereby improving the quality of the signal.
- Better reliability: Reduced aspect ratio of make them more reliable.
- Reduction in cost: HDI technology reduces the number of layers required for a circuit board. This happens without compromising the quality and operation of the PCB. Hence the cost of manufacturing is reduced.
The gaining momentum of technology towards the size reduction of gadgets has caused an increase in demand for HDI boards. Hence, every day, efforts are made towards improving every possible aspect of this technology. In the coming days, more superior methods will arise which would make miniaturization even more effective.
Get started with HDI Printed Circuit Boards (HDI PCBS)
- Blind vias, buried vias, and other microvia techniques
- Built-up laminations and high-signal performance considerations
- Laser direct imaging
- Fine lines and via-in-pad technology