Contents
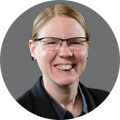
On-demand webinar
How Good is My Shield? An Introduction to Transfer Impedance and Shielding Effectiveness
by Karen Burnham
Choosing the same fab house for PCB prototypes and bulk production has many advantages, such as better DFM collaboration, manufacturing optimization, streamlined communication, and efficient supply chain management.
Entrusting a single manufacturer with all your circuit board production needs promotes a smoother production process while maintaining quality standards.
In this article, you will learn:
- Perks of choosing a single fab house for PCB prototype and bulk production
- Characteristics of a capable circuit board manufacturer
- Advantages of building a prototype prior to full-scale manufacturing
Before we talk about the advantages of choosing the same fab house for prototype and production, have a look at our infographic 10 things to check before choosing a PCB manufacturer.
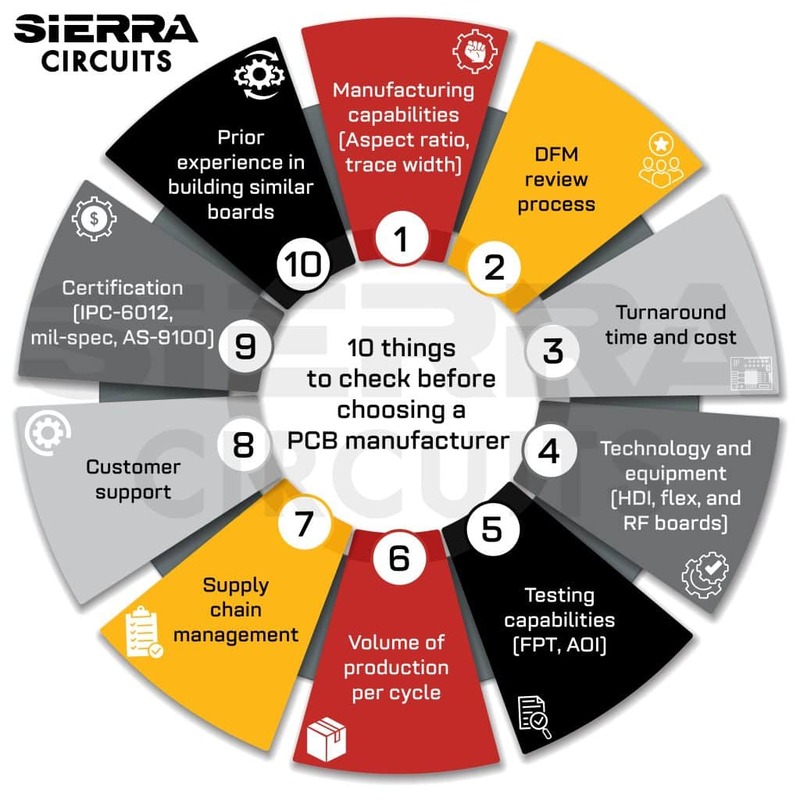
7 benefits of choosing the same fab house for PCB prototype and bulk production
Here are the advantages of getting your prototype and high-volume production from the same fabrication house:
1. Shortens time to market
Capable manufacturers can support you at every stage of the board production. Maintaining a harmonious working partnership is essential. If you choose a different PCB manufacturer after your prototype is ready, it will consume a significant amount of time in finding a new manufacturer and understanding their workflow.
Thus by choosing a circuit board manufacturer that has expertise in both prototype and mass production, you can shorten the time to market.
2. Efficient data transfer within the fab house
Often, when you shift between two manufacturers, there can be a risk of inconsistent data transfer. For instance, you make multiple modifications to your original PCB design files during the prototype stage. Tracking every change and its reasons can be challenging.
The manufacturer can also modify the specifications to make the design compatible with their machinery. Conveying these design files to the next PCB manufacturer can be time-consuming and may cause data discrepancies.
When you choose the same fabricator, the prototyping data will remain intact. The manufacturer’s prototype team will just transfer the updated design data effectively to the bulk production team.
In case you happen to have a different bulk manufacturer, you will have to go back and forth between two vendors which can be frustrating.
3. Maintains consistency between PCB prototype and bulk production
When you work with the same manufacturer, they become familiar with your design requirements, preferences, and manufacturing constraints. This will help in maintaining consistency across PCB prototypes and bulk production. Thus, the final product will meet your expectations.
4. Similar DFM processes for PCB prototyping and bulk orders
Through a detailed review, fab houses can identify and rectify potential DFM issues in your design. They can also ensure that your PCB design meets industry standards and complies with their manufacturing capabilities. This will help prevent expensive errors and delays during production.
DFM guidelines and circuit board manufacturing tolerances vary with manufacturers. Working closely with the same board manufacturer throughout the prototype and bulk production facilitates better collaboration.
The feedback and suggestions received to optimize your prototype can be carried through the high-volume manufacturing process. This effective coordination helps minimize design iterations and speeds up the transition from prototype to mass production.
Steve Dutton, Director of Aerospace and Defense Business at Sierra Circuits, explained, “DFM in prototype and production stages are different. Most of the time, tighter track gaps, sharp corners, closed pads, or pad-to-copper issues can survive through the slim prototype environment. But in high-volume production, these aspects create yield issues. Hence, this data needs more attention during DFM analysis of high-volume production”.
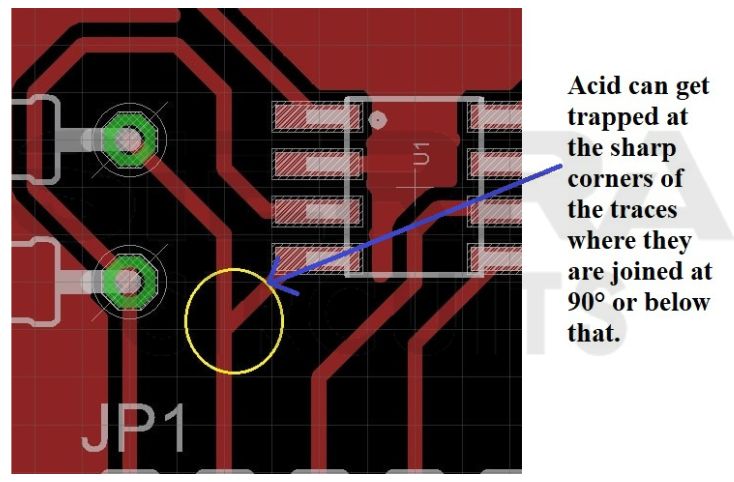
5. Optimized manufacturing process
When a fabricator is capable of processing prototypes and bulk orders, they can optimize their manufacturing processes accordingly. From the prototype stage, they gain valuable insights that allow them to refine their processes.
This can help them in scaling their high-volume production accordingly. We will discuss more about scaling in one of the upcoming sections. This will result in faster turnaround times, reduced errors, and improved manufacturing yield.
You can also leverage their experience to optimize your design and allocate resources effectively.
6. Effective supply chain management
Opting for a single fabrication house allows for better supply chain management. They will be familiar with your production timelines, volume requirements, and material needs. Hence, the manufacturer can proactively manage their inventory and ensure the availability of the required materials.
They can also optimize their production schedule to accommodate bulk orders more effectively. Through their well-established supply chains, they can help you obtain competitive pricing and assured material availability.
7. Streamlined communication
Choosing one manufacturer for all your PCB needs can help you establish a long-term relationship with a fabricator. This allows you to have efficient and streamlined communication. You become familiar with the communication interface and processes. It will be easier to collaborate with the design, engineering, and production teams.
With this collaboration, you can get design support, and your queries will be addressed effectively. This helps reduce miscommunication during the entire production process.
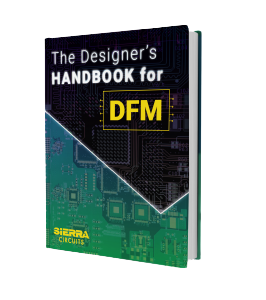
Design for Manufacturing Handbook
10 Chapters - 40 Pages - 45 Minute ReadWhat's Inside:
- Annular rings: avoid drill breakouts
- Vias: optimize your design
- Trace width and space: follow the best practices
- Solder mask and silkscreen: get the must-knows
Download Now
Qualities of a capable prototype and bulk-order manufacturer
Vadiraj Kulkarni, Senior Manager, Sales Engineering and Business Development at Sierra Circuits, says, “ When transitioning from prototype to bulk production, the manufacturer’s ability to repeat the same process every time to produce the exact board is extremely important. This will lower the risk of the rejected board”.
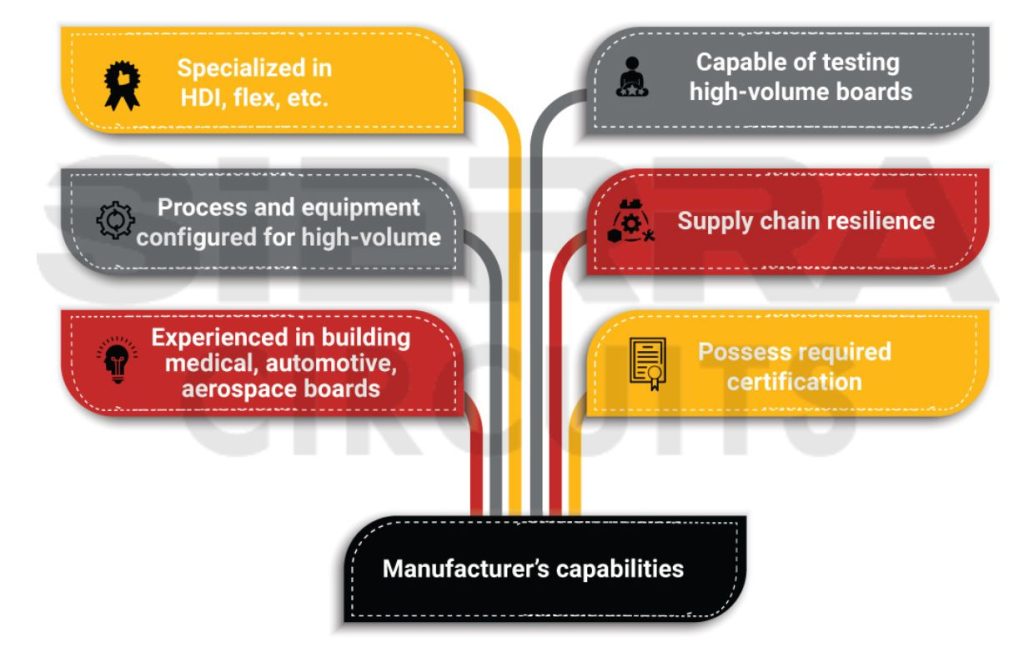
For a successful board production, you need to partner with a fabrication house with the following qualities:
Provides expert design assistance
The circuit board manufacturer should possess experienced and skilled design experts who can support you in creating an efficient PCB layout. They need to help you in choosing the right substrate, prepare the stack-up, and calculate the impedance values.
They should also be updated on the latest industry standards, materials, and manufacturing techniques. This will help you in getting valuable insights, troubleshooting issues easily, and guidance throughout the production process.
Experienced in building boards for various industries
A proven track record of managing PCB prototypes and bulk production for diverse industries such as consumer electronics, medical, automotive, aerospace, and defense. Manufacturers should also specialize in building boards with HDI, high-frequency operation, microvias, and controlled impedance traces.
Robust supply chain management
A robust supply chain management system with reliable suppliers ensures a steady supply of quality materials. They should also have a recovery plan for any supply chain risks such as natural disasters, cyber-attacks, business continuity risks, and pandemics. Having an assigned team to manage these risks is also essential.
State-of-the-art facility
Well-equipped facilities with advanced machinery, automated assembly lines, and quality control systems with a good production capacity. They should have testing and quality control procedures for producing reliable boards on a large scale.
Certified
Your CM should be certified by the organizations such as IPC, ISO, Mil-spec, DLA, ITAR, etc. This is essential to build boards for critical industries such as health and automotive.
On-time delivery and logistics
Manufacturers should take responsibility for the timely delivery of circuit boards. They should correctly package, label, and ship the boards to your location. In case of any delays, they should proactively address the issue.
You might also be interested in learning the benefits of choosing turnkey PCB manufacturing and Assembly from a single facility.
Why building a PCB prototype is necessary?
In prototyping, we build a small-scale and functional circuit board before proceeding with mass PCB production. Here, a design concept is translated into a physical prototype, which is tested and evaluated.
This is a crucial step in the product development cycle, where you verify the functionality and feasibility of a design. For guidelines on designing a PCB prototype, see building a PCB prototype from scratch: A designer’s guide.
The main reasons for creating a prototype are as follows:
- Avoids unnecessary high-density connections, a high number of cutouts, and increased component count through successive iterations.
- Enables you to choose dielectric material that is cost-efficient and also fits your design requirements.
- Ensures that all layout constraints (dimensions and clearances) can be easily transitioned to bulk manufacturing.
- Makes your design error-free through signal integrity analysis, and electrical and functional testing.
- Identifies manufacturing errors that reduce the risk of re-spins during high-volume production.
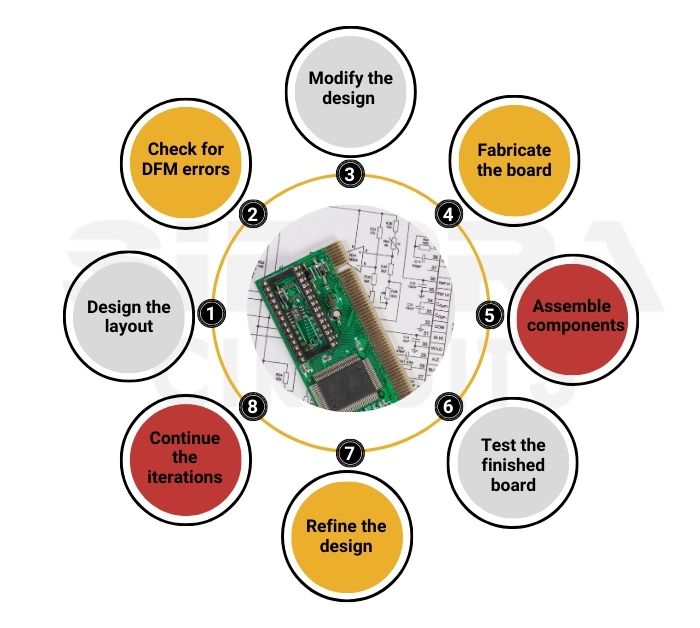
Things a PCB designer should know about high-volume production
Generally, fabricating more than 100 panels with multiple arrays of circuit boards is considered mass production. The tested and approved prototype design can be replicated in thousands to millions of units.
Compared to small scale, high-volume manufacturing is cost-efficient with lower turnaround time. The manufactured product will also be more consistent. Furthermore, the production cycle with be less with improved process control.
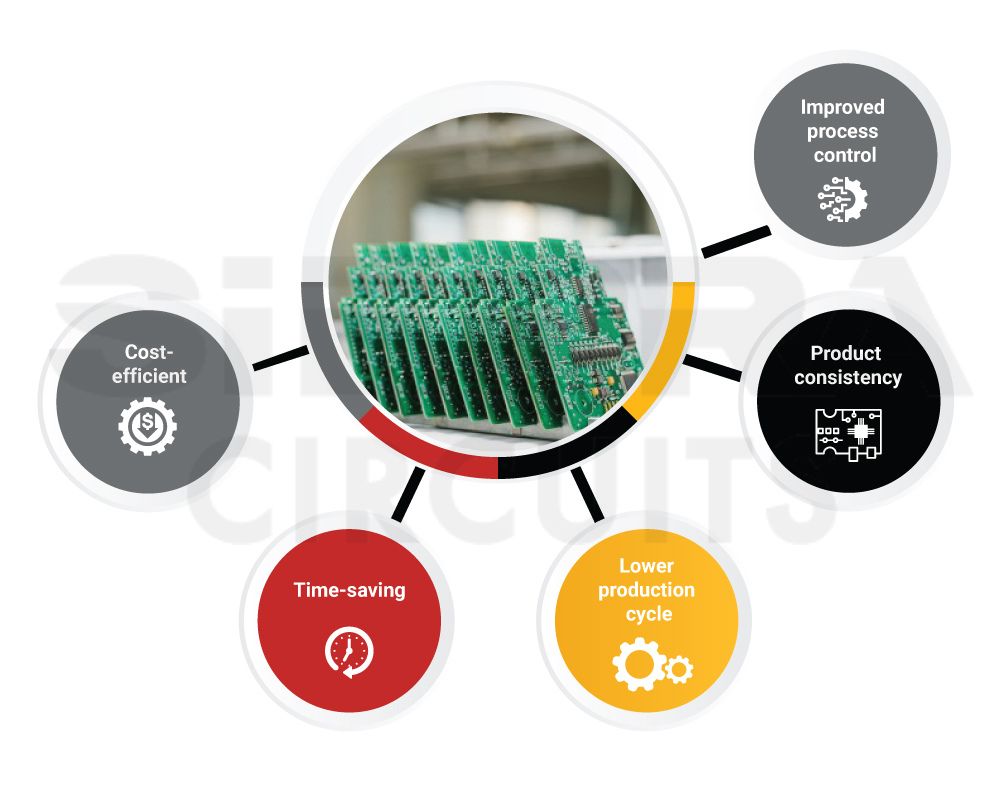
Scaling the manufacturing process
For full-scale PCB production, we need to optimize the workflow and ensure efficient utilization of resources. Here, the manufacturer needs to identify the bottleneck process which decides the throughput of the facility (irrespective of its size).
For instance, if the hole plating is lagging behind the drilling process, then drilled circuit boards will wait in line for plating. This will be the bottleneck process that determines the timeline for production.
Adding another machine to the plating section may not be the only solution. The manufacturer should utilize the complete plating bath area by choosing the right panel size.
Sometimes, scaling can also depend on the design requirements. If the circuit has a heavy component with a through-hole assembly, then it needs manual soldering. This will consume more time than the automated assembly line for the rest of the components. Hence, the manufacturer needs to consider all these scaling factors before moving into production.
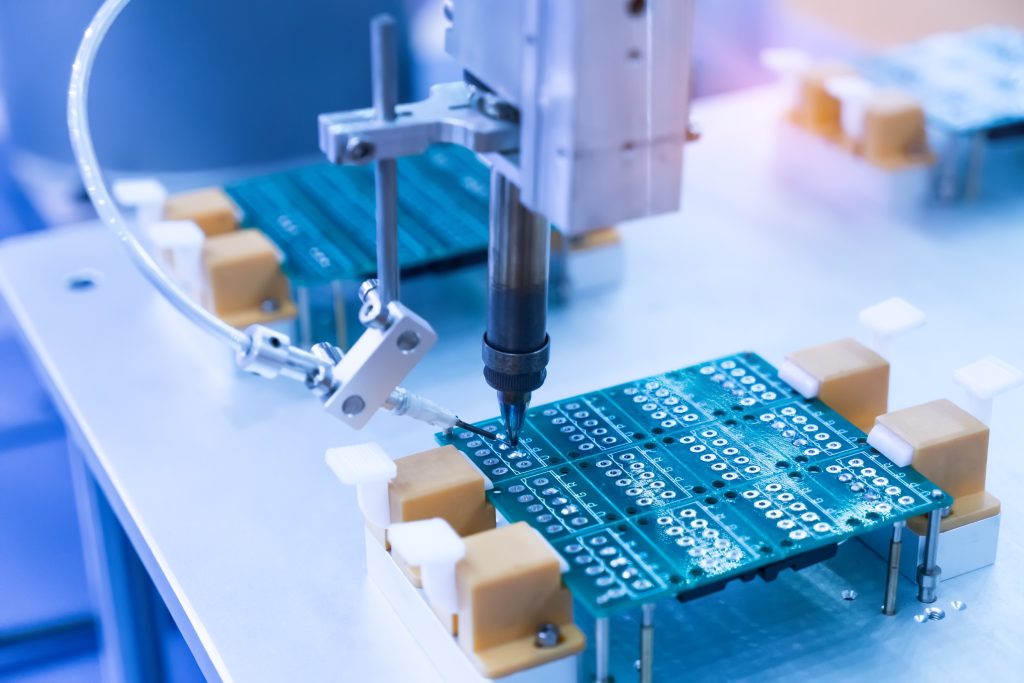
Advanced manufacturing techniques
When you are aiming for mass production, time to market becomes crucial. Therefore, each production cycle duration should be minimized as much as possible. This can be achieved by incorporating automated machines like robotic soldering, pick-and-place machines, and inline testing systems.
Additionally, the equipment size should be scaled to accommodate high-volume production like tanks, presses, CNC machines, drilling, etc.
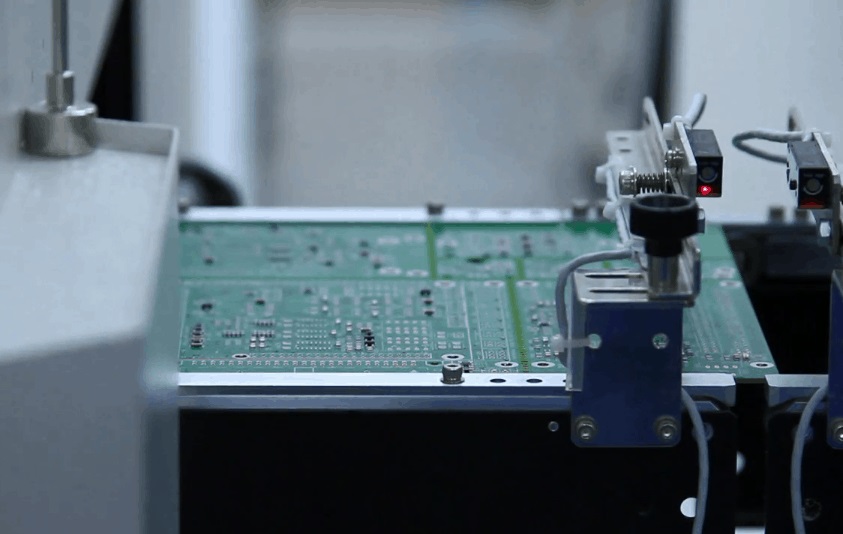
Steve Dutton stated, “A small volume bath could create exothermic heat, which is detrimental to the panel. You can avoid this by using large tanks with controlled heat rise and temperature”.
Material sourcing and management
Supply chain management and sourcing of materials like different types of laminates and components are crucial in high-volume production. When there is a scarcity of a single material, it can affect the whole production line. Hence, the fab house needs to closely coordinate with local and global vendors.
Procuring the same material from multiple vendors can ensure a stable and timely supply of raw materials. Further, efficient inventory management is also necessary to optimize production efficiency and minimize material waste.
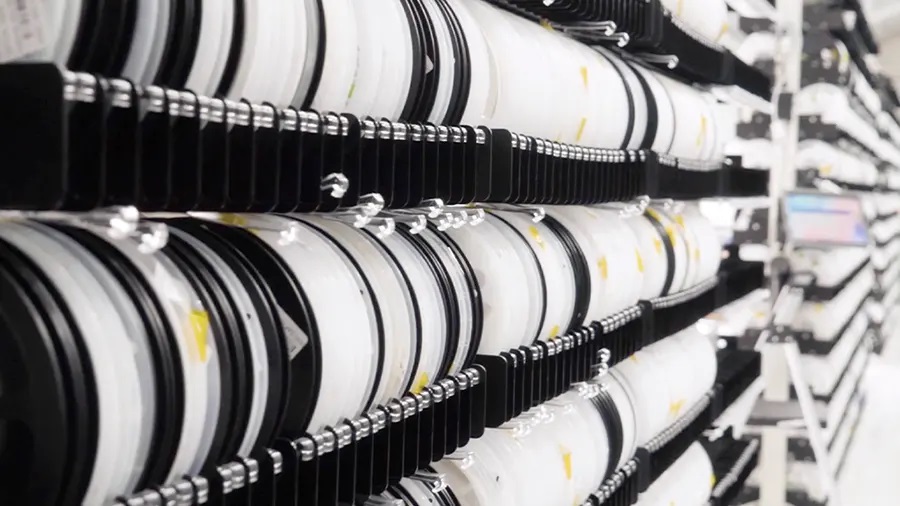
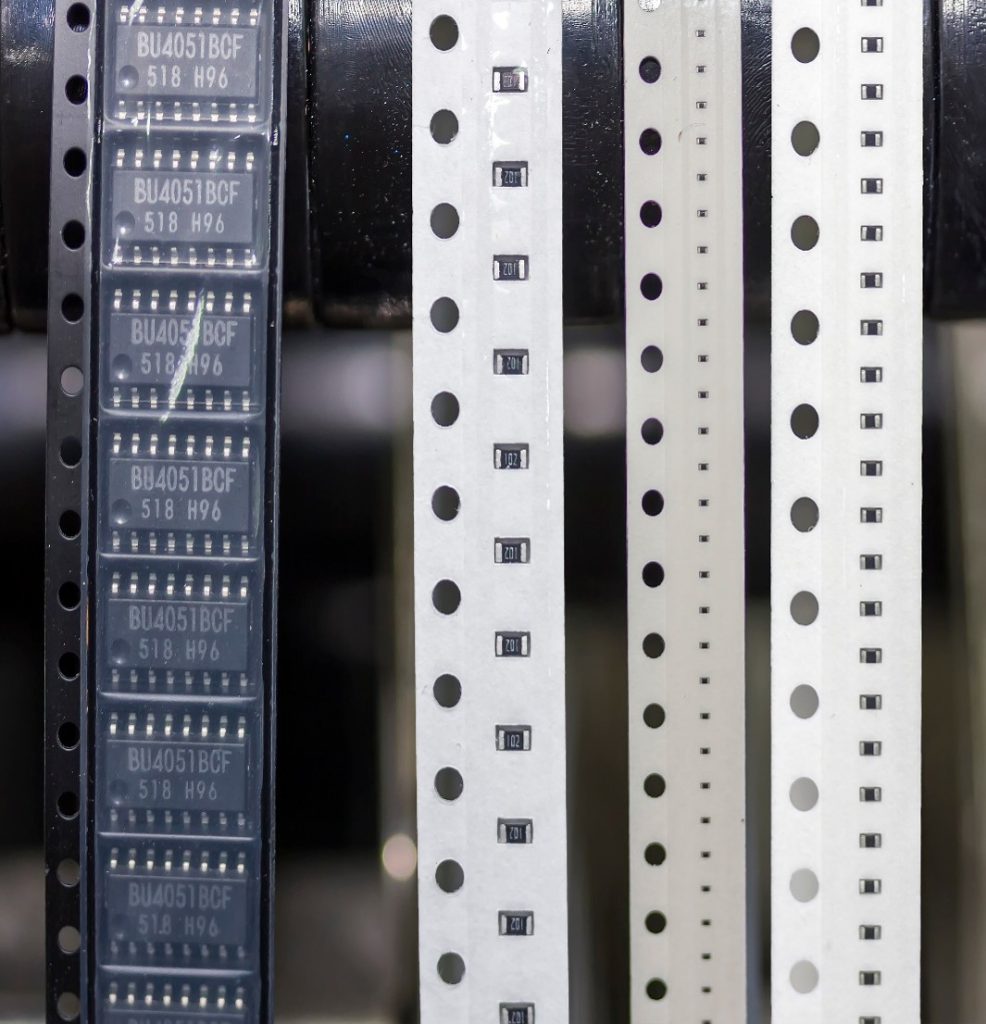
Choosing array and panel size
Selecting the right array size can increase production throughput and reduce cost. You can determine this using board dimensions and volume. Next, the manufacturer decides the panel size that accommodates these circuit board arrays. They need to add test coupons with panels based on IPC and DLA standards.
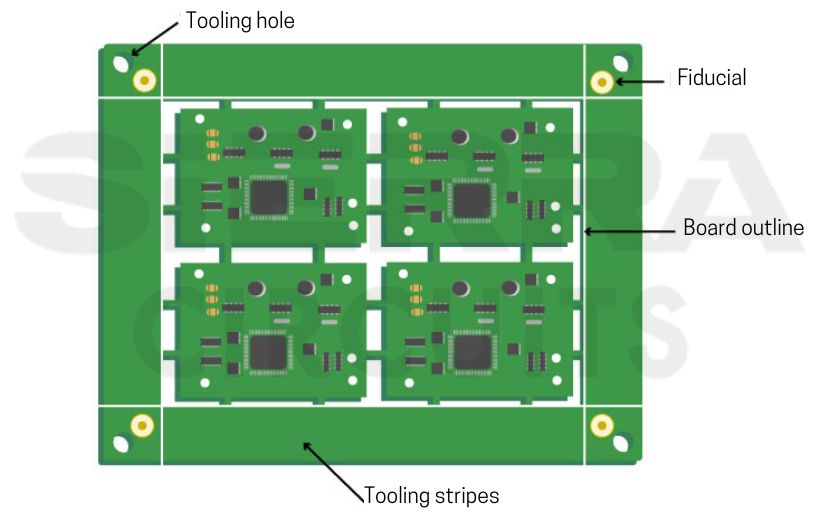
In a panel, the spacing between the boards can affect the manufacturing yield, cost, and ease of handling. For instance, if your PCB is odd-shaped, rigid-flex, or hybrid rigid, the number of boards per panel will decrease. It also requires a higher number of internal pinning to hold the registration for lamination, drilling, and imaging which increases costs and lead time.
Steve Bray, Vice President Group Operations, Sierra Circuits, says, “Removing snap-offs from trailing and leading edge can help reduce the costs without causing any detrimental impact on the board”
Quality control and testing
Maintaining quality across large quantities of boards can become a challenging task. To achieve this, PCB manufacturers must have strict quality control measures. This includes in-process inspections and adherence to industry standards such as UL, IPC, etc.
In mass production, the manufacturer needs to perform rigorous testing to identify any faults or inconsistencies in the fabricated board. They test multiple circuit boards on the panel at a time. A few standard tests include:
- Automated optical inspection: The AOI machine inspects every board visually (100% inspection), detecting any potential defects or anomalies.
- Electrical test using a flying probe machine: This test verifies the functionality of various components and checks for any electrical issues using the flying probe test machine. Further, for testing large quantities of the board, a master panel is created, and the fixtures are automatically placed to speed up the process.
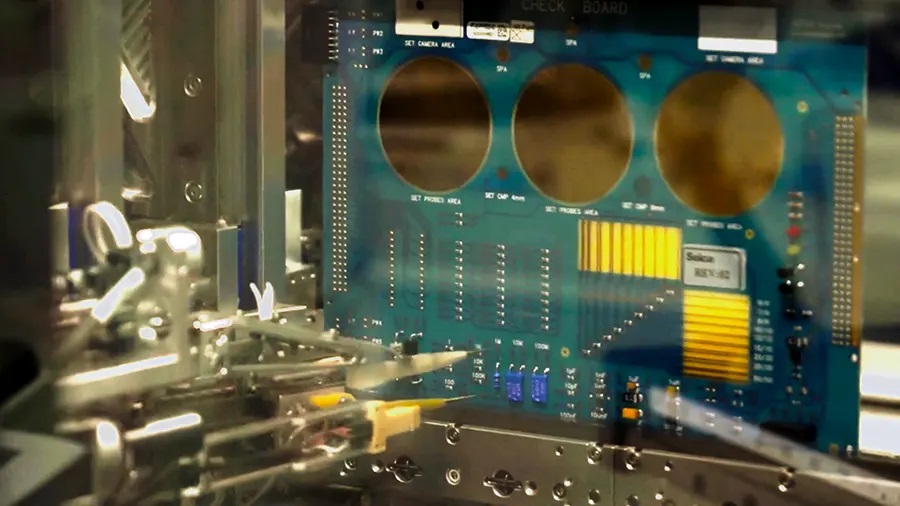
- Automated X-ray inspection: It identifies any flaws or irregularities present in the internal layers of the board. Additionally, PCB X-ray inspection helps to uncover hidden defects that may not be visible through other inspection techniques.
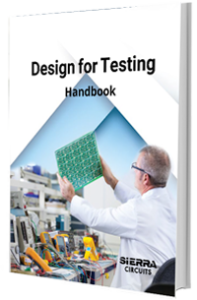
Design for Testing Handbook
7 Chapters - 28 Pages - 45 Minute ReadWhat's Inside:
- PCB testing strategies
- Guidelines to design and place a test point for FPT
- Directives to make your board ICT compatible
- Benefits and drawbacks of various testing methods
- Defects that you can identify through board testing
Download Now
Cost drivers in high-volume production
In high-volume production, the cost per unit can be lower when compared to the prototype, but the overall cost is significantly higher. Here, the board size, dielectric materials, number of layers in stack-up, drill holes, and surface finish are some of the cost drivers.
Hence, minimizing waste, improving yield, and reducing overhead expenses is crucial. For instance, efficiently arranging the arrays in a panel can help reduce material waste and increase cost efficiency.
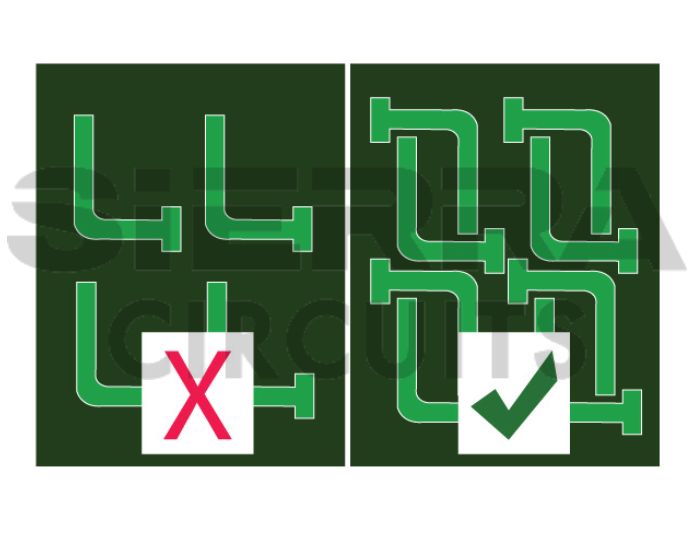
Key takeaways:
- The benefits of opting for the same fabricator for PCB prototyping and bulk production include efficient data transfer, robust supply chain management, and streamlined communication.
- Before choosing your CM, ensure that they provide expert design assistance, are capable of building boards for different industries, and possess the required certifications.
- As a designer, you should always understand the scaling process of your fab house and high-volume cost drivers before transitioning to large-scale production.
For a seamless transition from PCB prototype to bulk production, opting for a single fab house can be a good choice. By working consistently with the same fabricator, you become familiar with their workflow while they gain a deep understanding of your design requirements.
Sierra Circuits is capable of fabricating both PCB prototypes and bulk production. We have two state-of-the-art facilities with skilled and experienced staff to support all your circuit board requirements. Visit our PCB mass production to learn more about our capabilities.