Contents
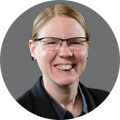
On-demand webinar
How Good is My Shield? An Introduction to Transfer Impedance and Shielding Effectiveness
by Karen Burnham
Choosing the right flexible PCB material is crucial as it impacts board functionality, production time, and cost. But how to select a suitable substrate? Many designers blindly opt for FR4. Should you just follow the trend? Don’t make this mistake. You need to analyze the design requirements before making a choice.
Different kinds of substrates are available for different applications. One such material used to build FPCs is polyimide. In this article, you will learn all about its properties, types, and applications.
What are polyimide PCB materials made of?
Polyimides (PI) are synthesized polymers of imide monomers comprised of two acyl groups (C=O) linked to nitrogen (N). They belong to the thermosetting and thermoplastic categories.
Due to their excellent mechanical strength and thermal resistance, they have replaced glass and metals in many applications. Because of their good dielectric properties and low coefficient of thermal expansion (CTE), PI is prevalently used in flexible printed circuit board fabrication.
This material is available in many forms, such as films, resin, plastic, adhesive, and insulation.

Significant polyimide material properties
The properties of the dielectric material can impact heat dissipation, signal integrity, load-bearing capacity, and the overall weight of your board. In this section, we will see how polyimide laminates can be a good choice for your design.
Polyimides have a mechanically robust structure
Polyimide substrates have good strength and durability to resist any physical damage when operating in harsh conditions.
Excellent flexibility: This laminate has a film structure, allowing it to bend. That’s why they are generally preferred for flexible and rigid-flex designs. In the below graph, you can see that the elongation is directly proportional to the stress.
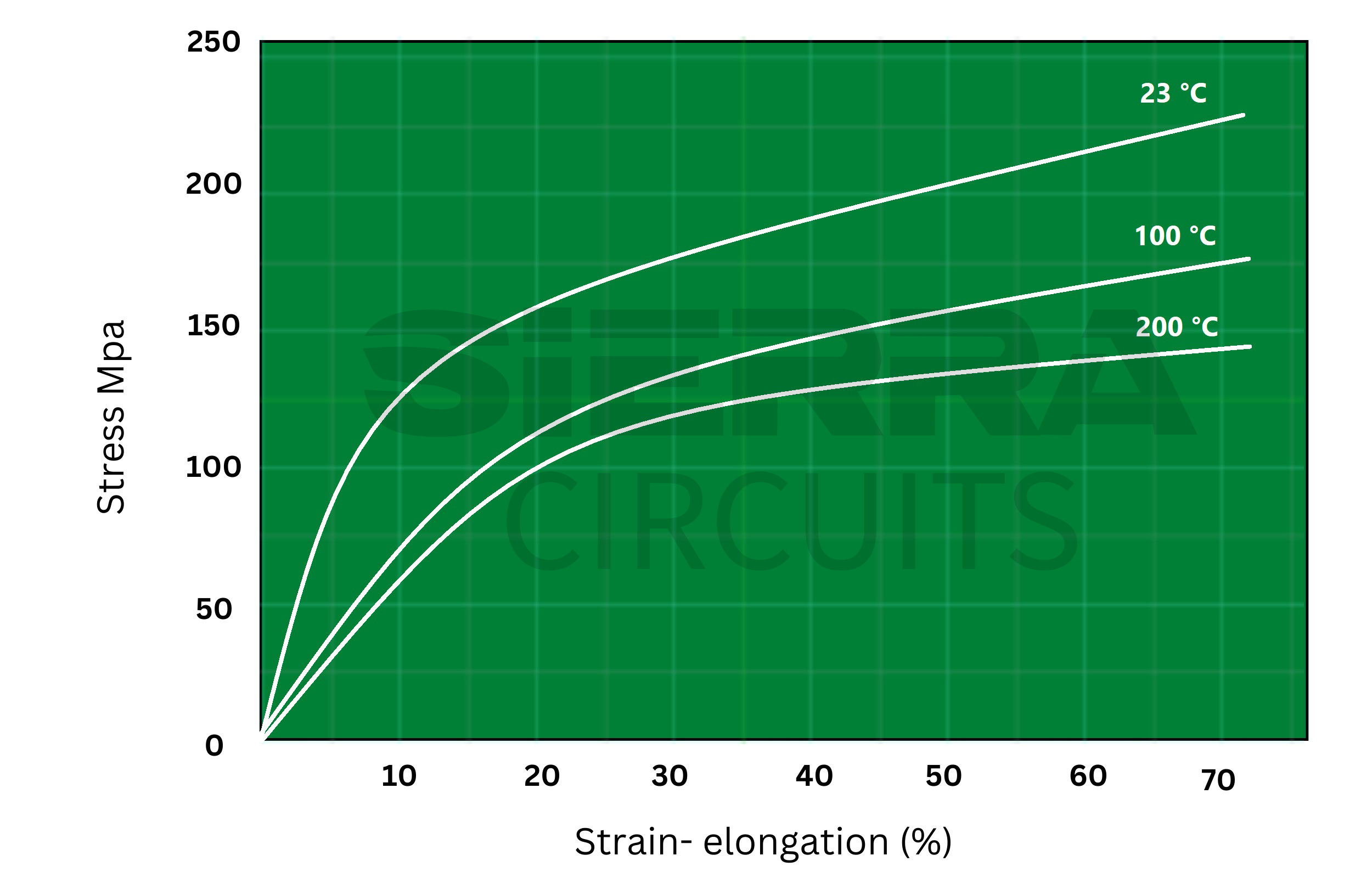
Good tensile strength: Even though they are flexible, polyimide board materials have commendable tensile strength. This enables them to be stable and support heavier loads.
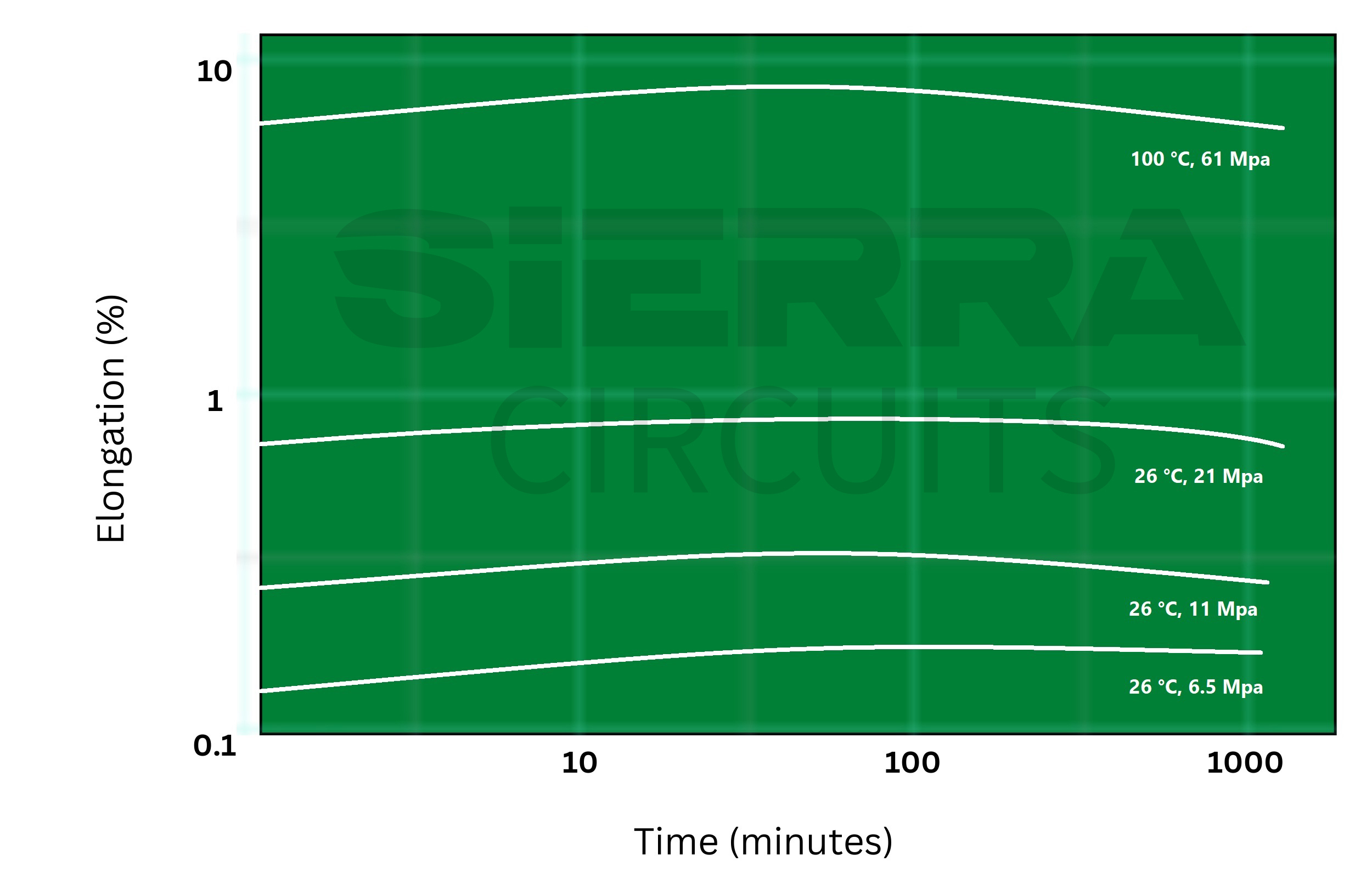
The graph shows that PI materials are stable even when they are elongated for a longer duration. They are warp-resistant, which helps during the stack-up preparations.
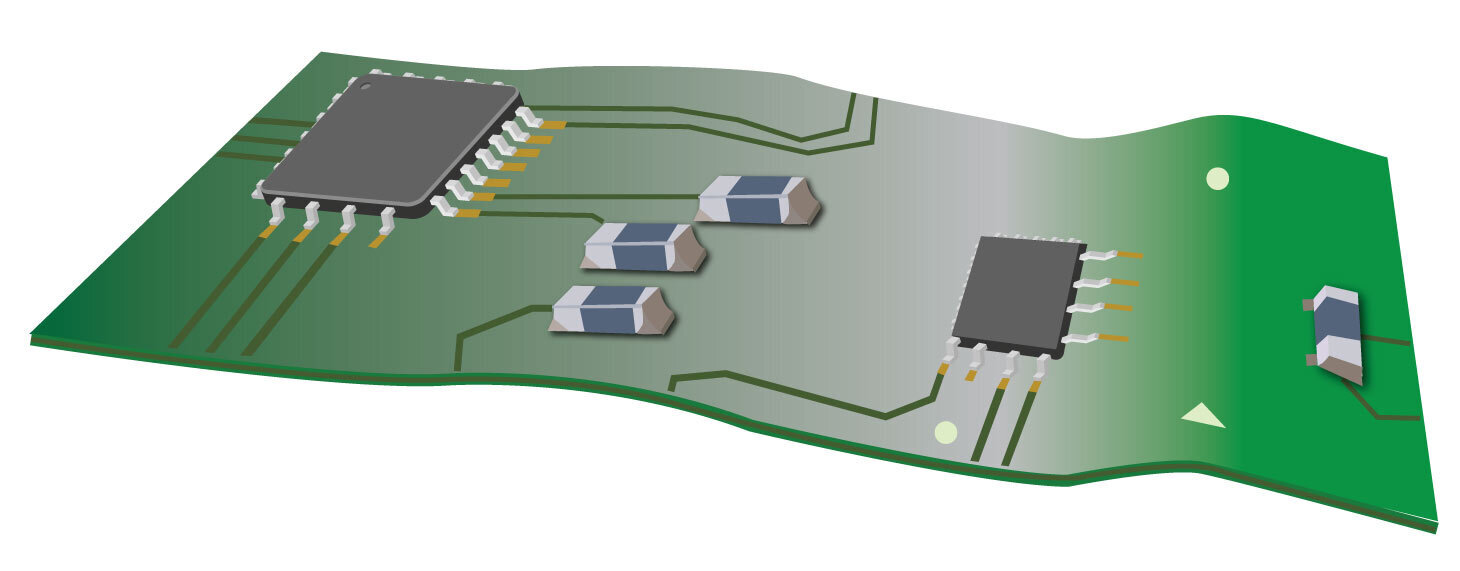
Chemically resilient with long linear-ordered structure
Electronic devices operate in a wide variety of environments; therefore, the material should withstand chemical reactions such as corrosion and ionic contamination. Polyimides are chemically stable, and their long linear-ordered structure makes them solvent resistant.
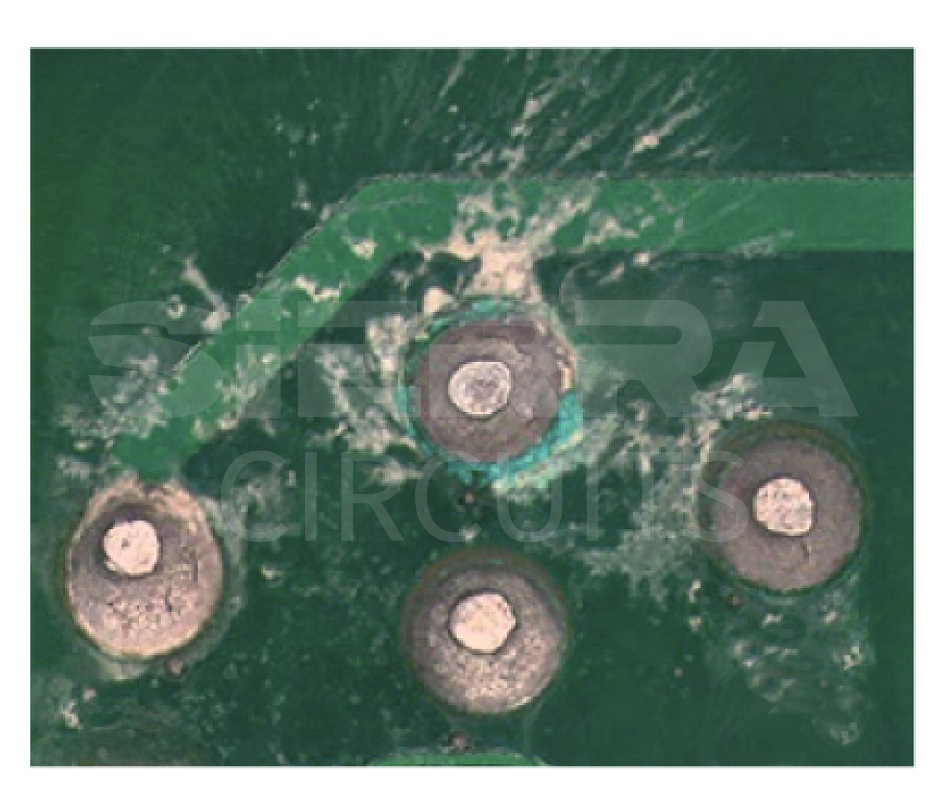
Thermal stability at high temperatures
During the manufacturing and assembly processes, the board materials are exposed to high thermal pressure. After fabrication, PCBs may have to withstand high operating temperatures based on your application.
To mitigate these challenges, you need to choose a substrate that endures high temperatures without any breakdowns. In addition to this, you should also implement thermal strategies such as thermal pads and heat sinks to effectively dissipate the heat.
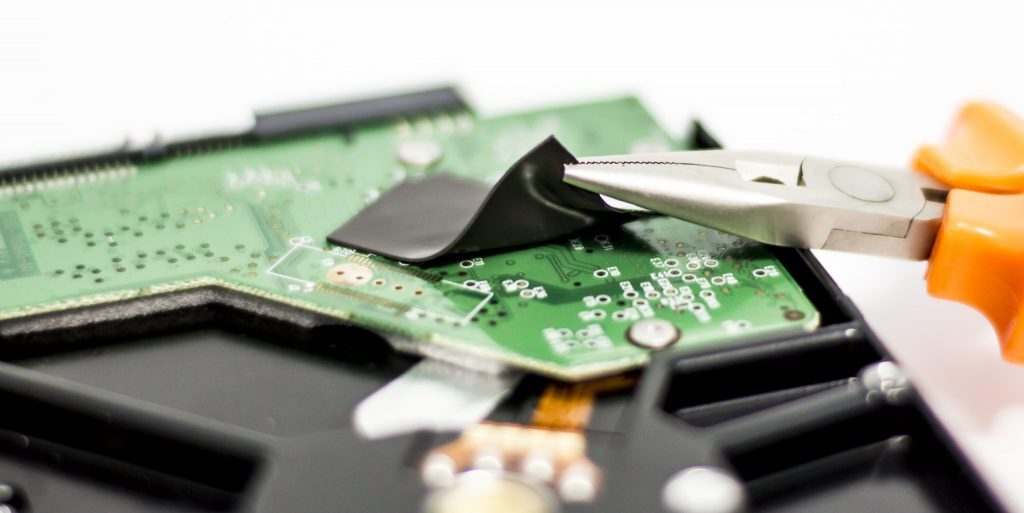
Polyimide substrates for PCBs are stable across a wide range of temperatures between 400-500°C and have good thermal conductivity. In recent applications, Kapton substrates have been successful in withstanding temperatures from -269°C to 400°C.
PI has a linear and stiff cyclic backbone in comparison to other thermoplastic polymers with coiled and flexible chains. This arrangement allows polyimide to have lower CTE. Hence, they exhibit better thermal stability. Additionally, their glass transition temperature (Tg) is also high (>300°C).
Possess the desired electrical properties
Good electrical characteristics are a basic requirement to avoid signal integrity issues. PI provides suitable insulation with the dielectric constant varying between 2.78 and 3.48 at 1Hz. It also has a lower dielectric loss that ranges from 0.01 to 0.03 at 1Hz. It also exhibits transparency in microwave circuits, and is resistant to radiation.
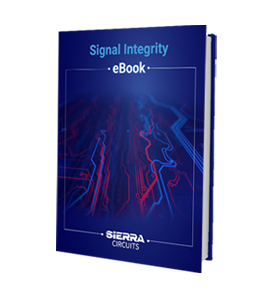
Signal Integrity eBook
6 Chapters - 53 Pages - 60 Minute ReadWhat's Inside:
- Impedance discontinuities
- Crosstalk
- Reflections, ringing, overshoot and undershoot
- Via stubs
Download Now
Popular polyimide PCB materials
There are many laminate compositions, and their properties can vary from manufacturer to manufacturer. Here are a few examples with their specifications:
Kapton HN film
DuPont manufactures this film laminate used for a wide range of applications. The properties of DuPont Kapton HN Film are as follows:
Parameter | Value | Test method/ standards |
---|---|---|
CTE (linear) | 20 ppm/°C | ASTM D-696-91 |
Thermal conductivity | 0.12 W/m K | ASTM F-433-77 |
Smoke generation | DM ≤ 1 | NFPA-258 |
Specific heat | 1.09 J/g K | Differential calorimetry |
Shrinkage | 0.17 % | IPC TM 650, Method 2.2.4A |
Tg | Between 360°C and 410°C | Varies depending on test methods |
Tensile strength | 231 Mpa at 23°C 139 Mpa at 200°C | ASTM D-882-91, Method A |
Stress- 5% elongation | 90 Mpa at 23°C 61 Mpa at 200°C | ASTM D-882-91 |
Tensile modulus | 2.5 Gpa at 23°C 2.0 Gpa at 200°C | ASTM D-882-91 |
Density | 1.42 g/cm³ | ASTM D-1505-90 |
Dielectric constant (0.5 mil) | 3.4 at 1kHz | ASTM D-150-92 |
Dissipation factor (0.5 mil) | 0.0016 at 1kHz | ASTM D-150-92 |
DuPont Kapton HN polyimide material datasheet
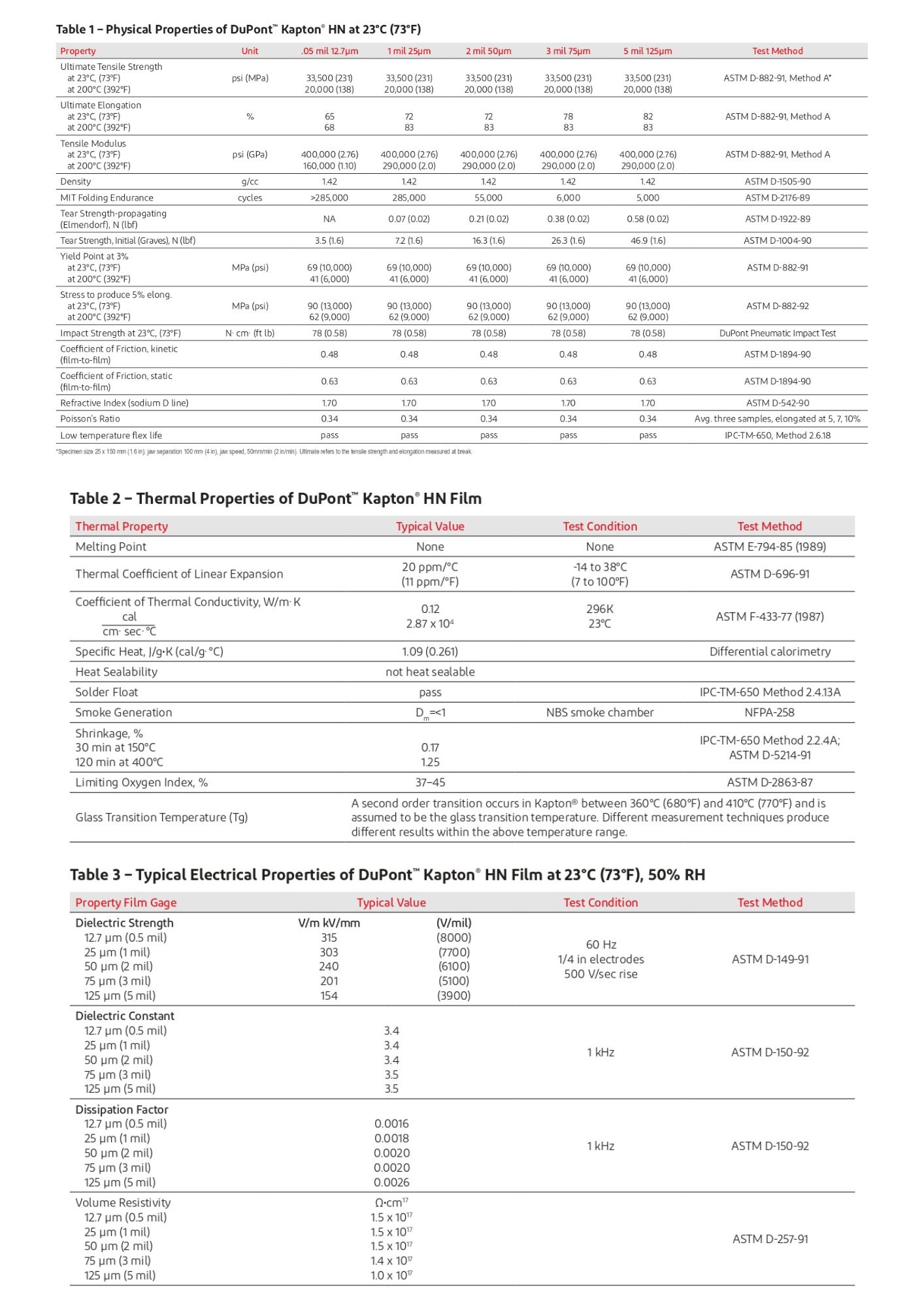
Isola P95 material
This PI laminate is infused with an E-glass weave. You can use this for normal speed and normal loss applications.
Parameter | Value |
---|---|
Dissipation factor at 1 GHz | 0.0172 |
Dielectric constant at 1 GHz | 3.78 |
CFA-resistant | Yes |
CTE, X/Y axis lower limit | 14 ppm/°C |
CTE, X/Y axis upper limit | 13 ppm/°C |
Electrical strength | 1100 Volt/mil |
RoHS compliant | Yes |
Tensile strength (Cross direction) | 36.1 Kpsi |
Tensile strength (Length direction) | 54.5 Kpsi |
Thermal conductivity | 0.4 W/m.k |
Isola P95 polyimide datasheet
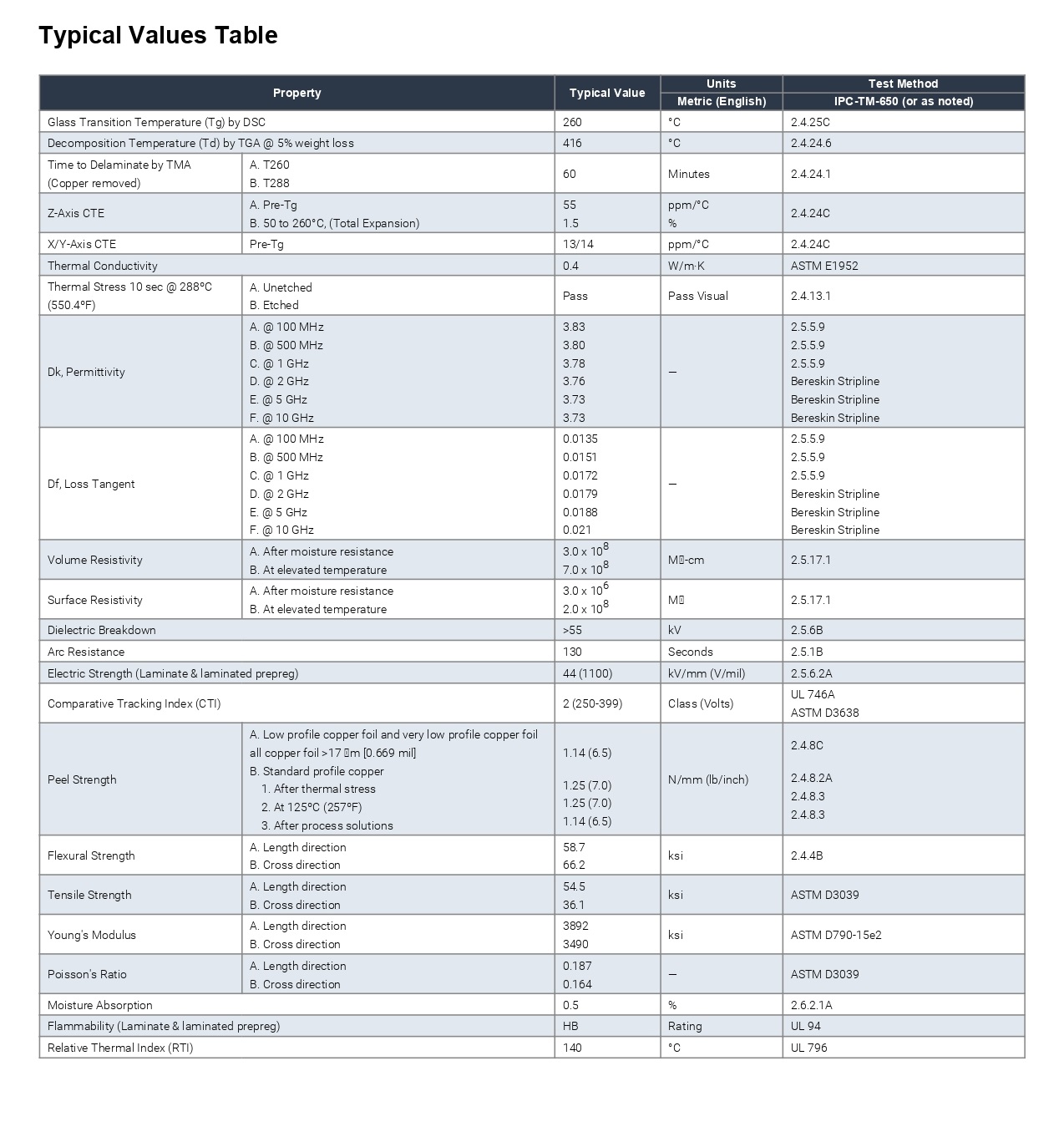
For interpreting the values of the datasheet, read our article on PCB Substrates: Knowing Your Dielectric Material’s Properties. Try our PCB Material Selector to explore the types of laminates available.
Polyimide Vs. FR4 – which is better?
Before comparing the materials, let’s briefly discuss what FR4 is.
FR4 stands for flame retardant, level 4. This is a substrate that comprises an epoxy resin and glass weave. It is a popular choice as the material has good mechanical and electrical properties and is also cost-efficient. The primary difference between polyimide and FR4 is flexibility.
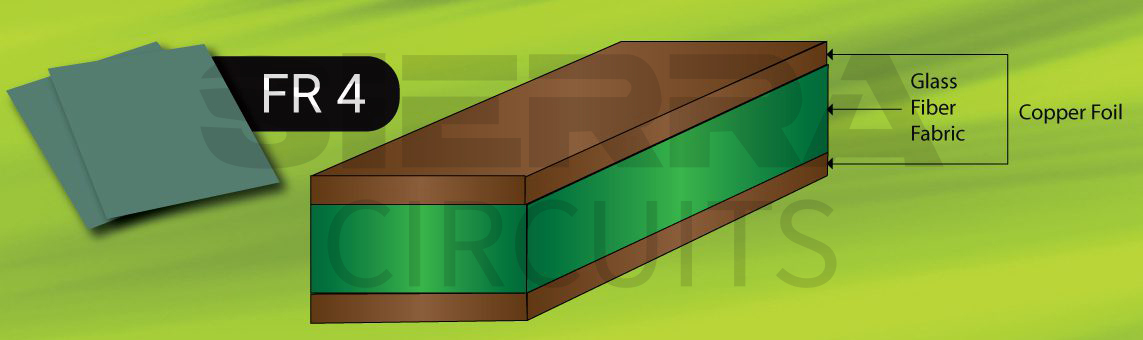
Additionally, FR4 can be fabricated with a standard manufacturing process, whereas PI needs a higher temperature. The choice of substrate depends on the circuit and application requirements.
The below table provides a detailed difference between polyimide and FR4 PCB materials. Knowing these differences will help you make the right decision.
Parameters | FR4 | Polyimide |
---|---|---|
Flexibility | Rigid | Highly flexible |
Chemical resistance | Good | Better |
Tensile strength | 70 Mpa | 231 Mpa |
Thermal stability | -50°C to 110°C | -200°C to 300°C |
Glass temperature | 135 °C | 195-220 °C |
Thermal conductivity | 2.2-2.5 cal/h.cm °C | 0.2 W/mK |
Thermal cycling | Good | Better |
Durability | Good | Better |
Elasticity | 24 Gpa | 4.0 Gpa |
Dk at 1GHz | 2.78 to 3.48 | 4.2 |
Df at 1 GHz | 0.016 | 4.0 |
Price | Low-priced | high-priced |
Polyimide Vs. Polyamide – what is the difference?
Both of them are thermosetting plastics that are heat resistant. However, the significant difference is in their chemical structure. Polyimide has an imide (-CO-N-OC-) group construction in resin form. Hence, we use it in board applications. On the other hand, polyamides have an amide (-CONH-) linkage, which is mostly in thread forms such as nylon. This is not suitable for circuit board construction. However, both these materials have outstanding electrical and physical characteristics.
Different kinds of polyimide PCB materials
Polyimide board substrates can be classified into different categories depending on the structure and the additives included.
Categorization based on the main chain composition
- Aromatic polyimide is a derivative of aromatic dianhydride and diamine, which have an open chain structure.
- Aliphatic is a combination of aliphatic dianhydride and diamine. These have both open and closed chains of compounds.
- Semi-aromatic has a part of aromatics (dianhydride or diamine) and a part of aliphatic.
Classification based on the inclusion of the additive
With no fillers
As the name suggests, this PI version does not contain additives such as brominated flame retardant. These are the pure and oldest kind of polyimide available and fall under the second-generation material. They are still popular as they are more flexible, strong, and thermally stable than other types of PI.
With flame retardants
These are updated versions of the 2nd generation with an added additive of flame retardants. This makes the polyimide PCB material more resistant to accidental fire.
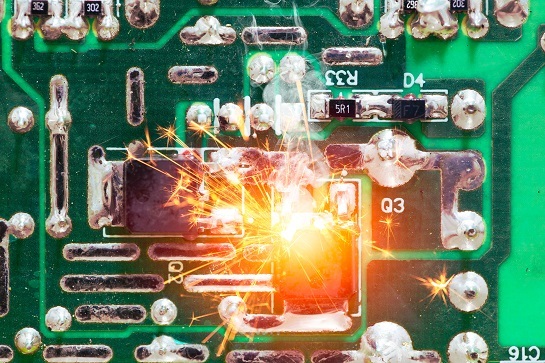
The inclusion of an additive lowers the time and temperature needed for producing the substrate. Hence, bulk production is possible. On the contrary, it reduces its thermal stability.
Many tests and regulations exist to check for the fire safety of a substrate. For instance, Underwriters Laboratory has set UL-94 flammability standards that categorize plastics into classes like V0, V1, V2, HB, etc. As an example, the DuPont™ Kapton HN polyimide falls under the UL-94 class V0.
With flow restrictors
The low-flow polyimides are built with flow restrictors and resin. Hence, they are not as flexible as other versions, and this stiffness becomes useful to withstand harsh environments. Choose this type of PI laminate if your design calls for higher durability materials.
Filled type polyimide
This PI is cured with various filler materials to avoid cracks or breakage in the resin during the lamination and drilling processes.
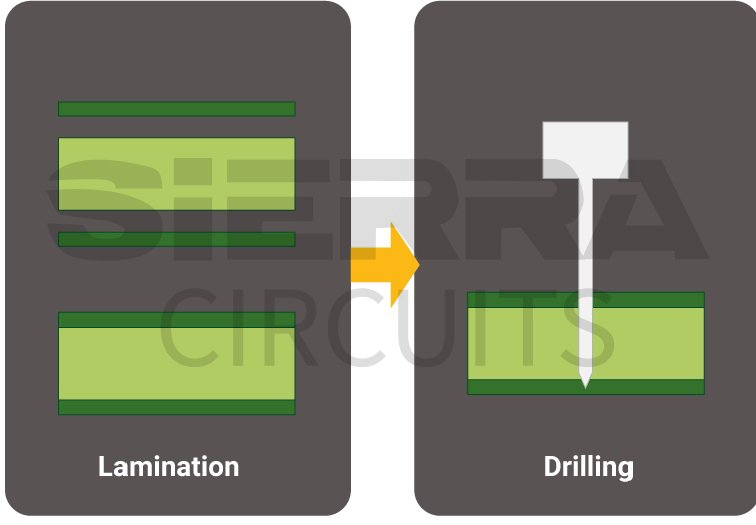
All the above substrates with additives fall under the 3rd generation polyimide category. In addition, 4th generation materials are expected to have improved adhesion properties and overall stability.
Polyimide PCB material applications
The versatility of PI makes it desirable for a wide range of applications in both domestic and advanced usage.
Consumer-based applications
With a constant demand for advanced, compact, and lightweight handheld devices, polyimide flex boards have enormous potential for consumer applications. Examples include computers, laptops, tablets, smartphones, video game consoles, and televisions. The material’s durability and thermal stability enable the gadgets to withstand heat and stress generated due to prolonged usage.
Polyimide circuit boards in the automotive industry
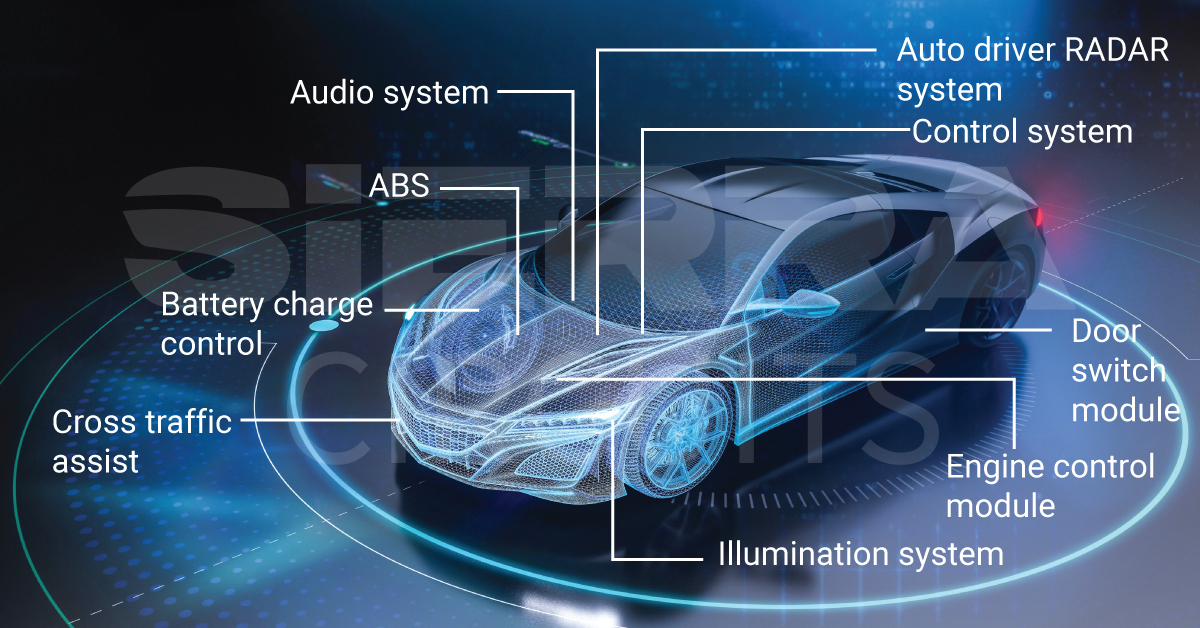
Cars and automobiles are built with many electronic devices such as engine control systems, audio systems, antilock braking systems (ABS), etc. These features ensure proper control and operation of the vehicle. Circuit boards in automobiles must withstand vibrations, temperature variation, and wear and tear.
Therefore, the materials used in these electronics should be robust. Polyimide flex PCBs have excellent mechanical strength and can bend to fit into irregular spaces. Hence, they are a popular choice for this application.
For more, see automotive PCB design guidelines.
Medical diagnostics and treatment equipment
The medical industry has increasingly relied on electronics for diagnostics and treatment. Equipment such as magnetic resonance imaging, ultrasound technology, and other advanced applications are aiding healthcare staff.
Circuit boards in medical devices can be exposed to contamination and temperature variations. Therefore, choosing a chemically resistant substrate is a prerequisite. To learn about standards, read MedTech PCB design considerations with IPC and Ul standards.
In cases like hearing aids and implants, the circuit needs to be compact and lightweight. Many prefer polyamide flex PCBs for these applications.
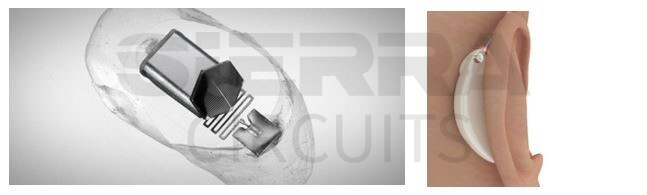
Military and aerospace applications
In military and aerospace applications, the boards have to operate in extreme environments. Therefore, the mil-grade laminate should have a high glass transition temperature (Tg). It is also ideal to have substrate materials with a low CTE and reduced losses.
A few applications that require advanced circuit boards are power distribution systems, digitized signal processing, flight instrumentation, communication, and navigation systems.
Even though they are not invincible, polyimide circuit board materials exhibit durability and thermal stability, which makes them the right choice for the military and aerospace industries. As this substrate can become brittle with heavy copper, choose a filled PI that is resistant to cracks.
All these advanced applications must comply with IPC standards and other regulations.
Prefer polyimide PCB material if you are working on flex designs that require higher thermal stability. These materials are tailored for operations in harsh environments. It can also be a good alternative for FR4 when there are no cost constraints. If you need anything more on PCB material selection, please comment below. We will be happy to help you out.
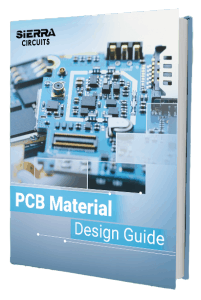
PCB Material Design Guide
9 Chapters - 30 Pages - 40 Minute ReadWhat's Inside:
- Basic properties of the dielectric material to be considered
- Signal loss in PCB substrates
- Copper foil selection
- Key considerations for choosing PCB materials