Contents
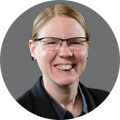
On-demand webinar
How Good is My Shield? An Introduction to Transfer Impedance and Shielding Effectiveness
by Karen Burnham
Black pad is a term that usually refers to nickel corrosion on electroless nickel and gold immersion (ENIG) surface finishes on PCBs. The defect is not seen as part of normal QC procedures, as the immersion gold masks the appearance of the nickel under the gold.
What does black pad mean?
The black pad represents the corrosion and oxidation of the electroless nickel, which primarily begins at the nickel nodule boundaries and then spreads as the corrosion increases. As the deposited gold thickness increases, the oxidation of nickel may increase. This particular issue results in reduced solderability and weakly formed solder joints. When those joints come under pressure, they break easily and leave exposed corroded nickel behind, hence known as black pad.
Initially, ENIG finish had several things working in their favor:
- Good shelf life
- Easy to inspect
- Since nickel protects the through-holes, it could stand up to testing better than some alternatives
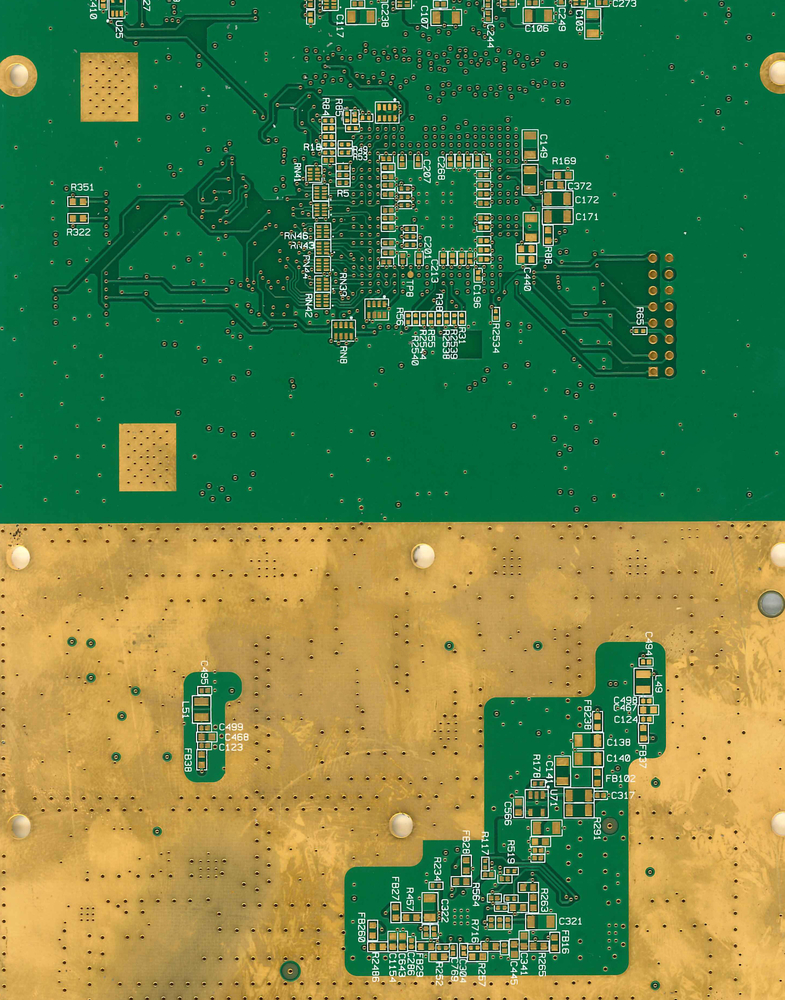
The ENIG process has become increasingly popular over time for several reasons, including the need to comply with the restriction of hazardous substances (RoHS) directive and the rising demand for lead-free soldering. Board manufacturers have gotten a lot better at understanding and working around black pad along the way, but it’s still a problem worth exploring.
What causes black pad?
There are several possible causes of black pad:
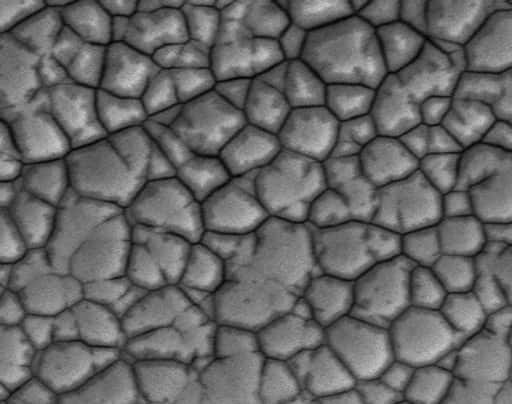
High phosphorus content
The reflows and repairs of the ENIG process increase the amount of phosphorus and ultimately weaken the board. As nickel dissolves, phosphorus remains behind. Overall, a high percentage of phosphorus is correlated with black pad errors.
Corrosion during gold deposition
When gold is deposited during the ENIG process, it relies on a corrosion reaction to place itself (the gold) on the nickel substrate. Aggressive gold baths, as well as high gold thickness, can increase the corrosion to a level approaching black pad. It is generally accepted to keep the gold thickness to 2-4 μin, as per the IPC-4552 ENIG specification.
Also read, What is Conformal Coating?
Brittle fracture
Sometimes what manufacturers label black pad is actually a brittle fracture. Black pad is similar to brittle fracture because it creates a cracked structure within the nickel after the gold has been deposited and then removed. Brittle fracture itself can occur when tin dissolves a portion of the nickel while also creating a thin layer of phosphorus that does not dissolve. Thermal stress, vibrations, and shocks can then weaken the metallurgical bonds.
What are the practical solutions to black pad?
- Generally, it is found after the PCB manufacturing process when the board is already populated. To identify the presence of black pad, it is required to look for certain flaws (cracked structure, non-planar surface, etc.) and to consider alternative finishes accordingly.
- It may be possible to rule out black pad after inspecting the surface of a finished board. For example, if there are no spikes and dark bands near the nickel boundaries, then it may not be an issue.
- Controlling the gold bath by maintaining the stoichiometry of nickel and gold can resist the black pad. It is also important to keep tabs on the pH level to know how much phosphorus will ultimately be plated.
- A well-controlled nickel bath is one of the keys to the elimination of this defect. For that, it is essential to verify any potential ENIG provider’s baths and processes. Many requirements have to be met across the ENIG line to minimize the risk of black pad, including pretreatment (removing oils and other residues to prepare for PCB etching) and use of chelating agents as well as stabilizers to prevent the nickel in the bath from plating out into the tanks.
Performance specifications for ENIG
In 2002, IPC issued a specification (IPC-4552) for ENIG. During that time, tin-lead solder was predominant in PCB assembly, and lead-free soldering was not a widely established concept.
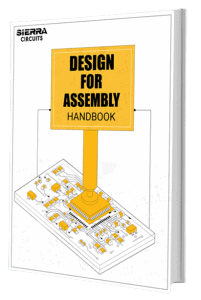
Design for Assembly Handbook
6 Chapters - 50 Pages - 70 Minute ReadWhat's Inside:
- Recommended layout for components
- Common PCB assembly defects
- Factors that impact the cost of the PCB assembly, including:
- Component packages
- Board assembly volumes
Download Now
According to IPC-4552,
- Electroless nickel thickness- 3 to 6 μm [118.1 to 236.2 μin]
- Immersion gold thickness- 0.075 to 0.125 μm [2.955 to 4.925 μin]
The specification was amended in 2012, due to the rising price of gold. The lower limit for gold thickness was decreased from 0.05 μm to 0.04 μm (1.6 μin).
At Sierra Circuits, we adhere to IPC specifications unless the customer specifies otherwise. The thickness of the coating can be measured using an XRF (X-ray fluorescence spectroscopy) technique.
A glance at IPC-4552 revisions
IPC-4552 revision A focuses on a thorough analysis of metal layer thickness measurement, composition, and nickel corrosion which is associated with the black pad defect. To meet these criteria, circuit board manufacturers must have the ability to measure and maintain electroless nickel thickness and its composition. The modification in the minimum gold thickness limit poses challenges in measurement systems and process control for satisfying the conformance to ENIG products.
Concerning the gold layer, the new thickness specification range will limit those who are driving down gold deposits to save money. An extremely thin coating of gold results in performance failure since a thin deposit may not withstand thermal conditioning and environmental exposure.
The current specification includes a section on measuring the phosphorus content of electroless nickel deposits. Previously, nickel-phosphorus (%P) level was described as low, medium, and high, but there was no industry standard for testing and controlling it over the bath life.
This revision introduces phosphorus content measurement and process control requirements. Finally, a clear explanation is provided on how to evaluate the corrosion potential of an ENIG deposit.
Nickel corrosion
The new revision is concerned with the electroless nickel layer’s resistance to corrosion due to poorly controlled electroless nickel plating processes during the immersion gold stage. It is crucial to focus on the chemical reactions of how the gold plating is done to understand nickel corrosion caused by immersion gold plating.
- Anodic reaction
Ni → Ni2+ + 2e–
- Cathodic reaction
2[Au(CN)2] – → 2Au+ + 4CN–
2Au+ + 2 e– → 2 Au
- Overall reaction
Ni + 2[Au(CN)2] – → 2Au + [Ni(CN)4] 2
The gold is deposited onto the nickel surface through an exchange reaction (displacement of Ni by Au atoms), also known as an immersion reaction. This reaction is determined by electron transfer and controlled by an electromotive series (an arrangement of elements and ions) stating that more noble metals will naturally plate onto less noble ones without any chemical reducing agents. It is necessary to transfer electrons from the metallic electroless nickel deposit to the gold ions in solution to deposit gold on the electroless nickel surface.
As the reaction proceeds, this electron transfer causes metallic nickel (corrosion) to be removed from the surface and builds up nickel ions in the immersion gold solution. There will always be some level of corrosion in gold plating since nickel needs to be removed from the surface of the electroless nickel deposit to facilitate the gold metal deposition.
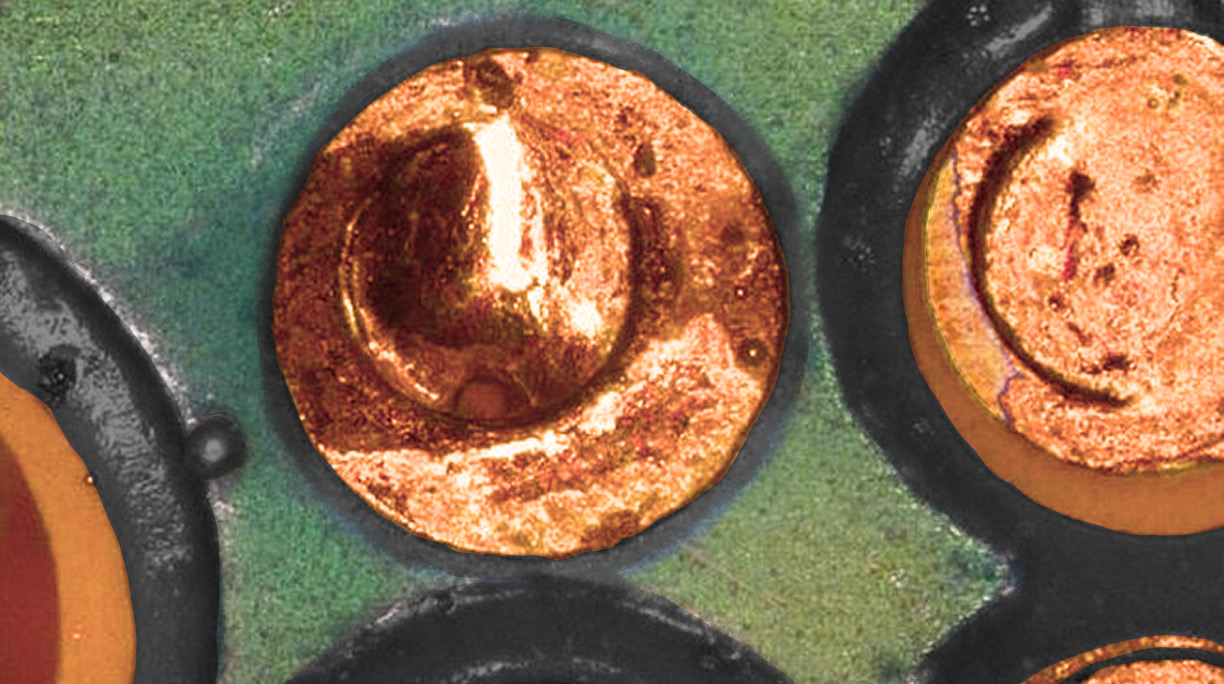
EPIG surface finish is one of the newer technologies, introduced as an alternative to electroless nickel immersion gold (ENIG). Unlike ENIG, it eliminates the use of nickel, avoiding nickel corrosion issues.
Hyper-corrosion of nickel
Black-pad defects are formed by the hyper-corrosion activity of the immersion gold process on the nickel surface. Gold and nickel atoms undergo galvanic hyper-corrosion, resulting in depletion of nickel and enrichment of phosphorus atoms in the localized area. Black pad, caused by a poorly formed joint at the solder/nickel-phosphorus interface, can lead to failures and de-wetting of the solder.
Hyper-corrosion involves the prevention of intermetallic formation and wetting of the surface (solder). This causes de-wetting, a solid-to-liquid bond failure, and interfacial fracture of the solder.
As per IPC-4552A, the average gold thickness should be three standard deviations above 1.58 μin and three standard deviations below 3.94 μin.
The gold thickness should have an average of
-3 s ≥ 1.58 μin, and
+3 s ≤ 3.94 μin
Where, = variable and s= standard deviation.
PCB manufacturers must comply with this thickness limit to maintain a high level of quality and reliability. The achievement of a lower limit of thickness and tight uniformity control improves the reliability of boards and reduces costs significantly.
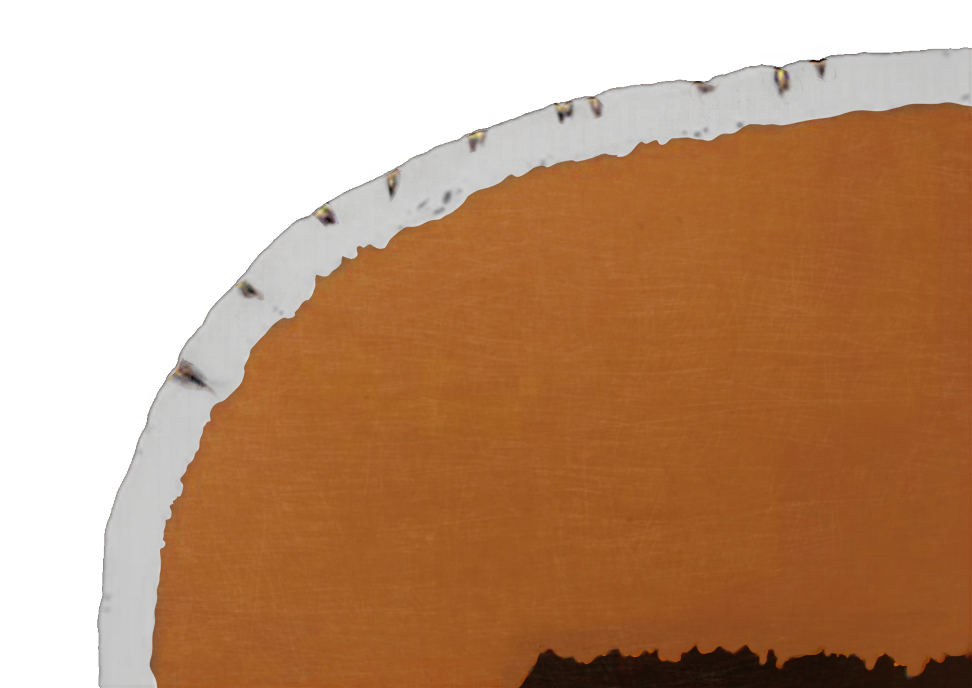
Here are a few important points to consider from a manufacturer’s perspective:
- It is always possible to find hyper-corrosion if sufficient samples are taken from a circuit board or if excessive magnification is used for inspection. However, a single instant of hyper-corrosion is acceptable.
- In hyper-corrosion, a non-wetting defect occurs (despite the gold being consumed) as a result of the lack of intermetallic compound (IMC) formation.
- Hyper-corrosion is acceptable if it does not interfere with the formation of a reliable solder joint, as defined by continuous IMC formation.
- Extreme hyper-corrosion in which the soldering is negatively impacted is rejectable. An optical microscope with a magnification of 1000x is recommended for inspecting hyper-corrosion.
- Non-wetting soldering error may occur for a variety of reasons, regardless of the final finish of the board. Hence, it is desirable to have a consistent, low level of electroless nickel corrosion to prevent any solderability failure from turning out to be a hyper-corrosion and therefore being rejected.
Also read, 8 Common Errors in Surface Mount Technology (SMT).
To achieve a durable ENIG finish, the Ni-P surface must be designed with chemistry and processes that will protect against hyper-corrosion. Additionally, solder joints containing nickel-tin intermetallic compounds are liable to brittle failure depending on the chemistry used. In this new ENIG, a barrier layer has been created at the Ni-P/gold interface, which overcomes the black pad defect and results in ductile solder joints that are not susceptible to brittle failures. Furthermore, the novel immersion gold chemistry is cyanide-free (environmentally friendly).
This new chemistry improves deposit composition uniformity and allows the ENIG products to be controlled so that they conform to important quality requirements. Let us know in the comment section if there is anything specific to black pad that you would like to know.
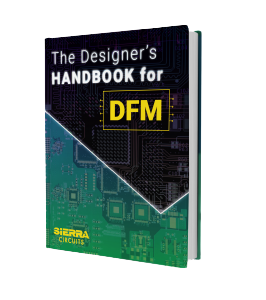
Design for Manufacturing Handbook
10 Chapters - 40 Pages - 45 Minute ReadWhat's Inside:
- Annular rings: avoid drill breakouts
- Vias: optimize your design
- Trace width and space: follow the best practices
- Solder mask and silkscreen: get the must-knows
Download Now