Contents
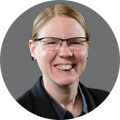
On-demand webinar
How Good is My Shield? An Introduction to Transfer Impedance and Shielding Effectiveness
by Karen Burnham
There are various challenges when it comes to PCB design and manufacture, and one of them is retaining signal integrity. When you transmit a signal, the signal received will be subjected to distortion from signal noise, crosstalk, and other undesired effects.
Incorporating design and manufacturing practices limits such effects and increases signal integrity. Via stubs often contribute to a decrease in signal integrity which can be resolved through the use of the back drilling process.
Through the course of this article, we will cover how to minimize the effects of a via stub on the signal integrity in a PCB through back drilling.
What is back drilling or controlled depth drilling in PCB?
High-speed PCB design faces many challenges in terms of retaining signal integrity which can be overcome through proper design and manufacturing practices.
A via stub, a non-functional part of a via, causes significant signal integrity issues in high-speed design. Via stubs result in the reflection of signals from the stub end, and this reflection will interfere with the original signal.
To counter this, back drilling is done, where most of the via stub is removed by re-drilling with a slightly larger sized drill bit.
Back drilling involves drilling a hole slightly larger in diameter than the PTH to remove the conductive via stub.
The back drilled hole should bring down the stub length to 10 mils. If the stubs are greater than 10 mils, then signal reflections will be produced.
Why is back drilling required?
Back drilling or Controlled Depth Drilling (CDD) is a technique used to remove the unused portion (stub) of the copper barrel from a through-hole (via) in a printed circuit board.
As these holes are back-drilled to a predetermined, controlled depth, this type of drilling is also called controlled depth drilling. Ideally, the via stub left after back drilling should be less than 10 mil.
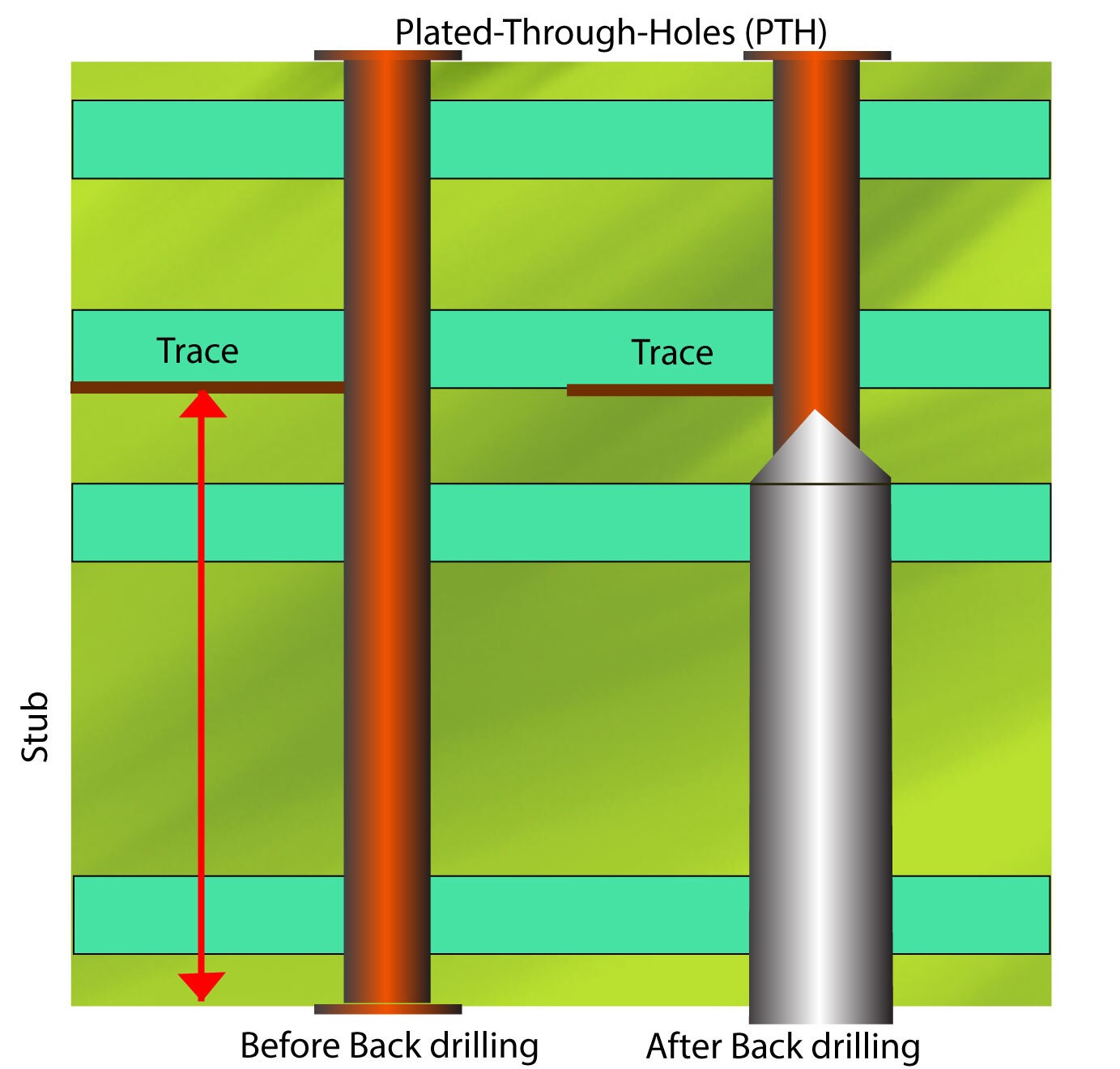
The images given below illustrate the steps involved in CDD to reduce signal reflection due to via stubs.
Step 1: In the below image, we can see a board with a via stub extending beyond the signal path.
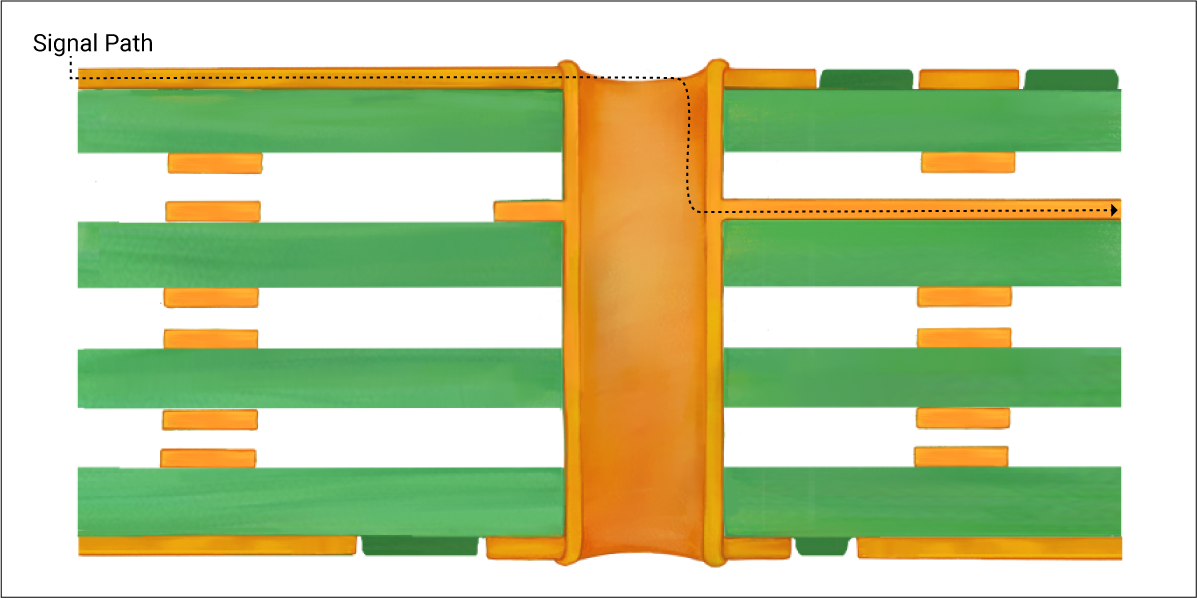
Step 2: Back drilling is done with a slightly larger drill bit.
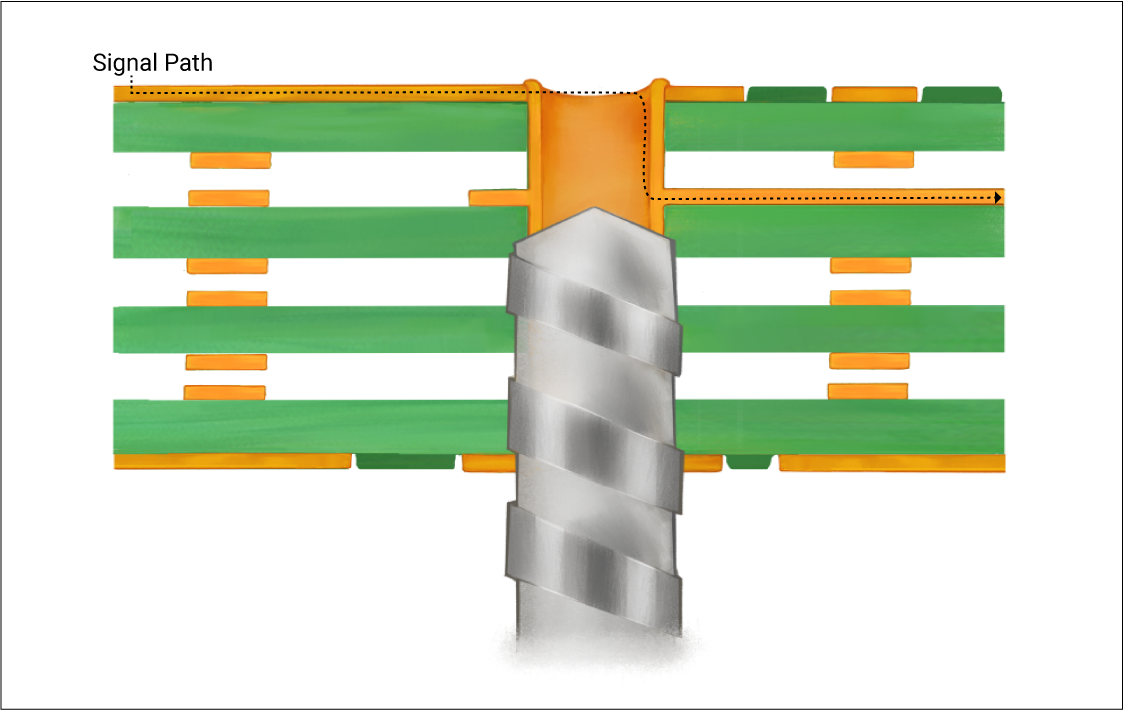
Step 3: Via stub reduced through back drilling.

Via fundamentals: Via stubs, PTH, NPTH
Vias are miniature conductive pathways drilled into the PCB to establish electrical connectivity between the different PCB layers. You can read about vias and their significance in the article how PCB vias interconnect circuit board layers.
A via stub is part of a via that is not used for signal transmission. Via stubs reflect signals and cause a number of signal integrity issues, especially in high-speed signals, which you can read about in this article signal integrity and via stubs.
Through-hole technology, which involves through-holes that go completely through the PCB, has been a part of PCB assembly since the 70s and 80s. Even though through-hole technology has been largely replaced by surface mount technology, it is still in use today.
Through-holes can be plated (PTH) or non-plated (NPTH). While PTH serves as a conductive path from one side of the board to another, NPTH is used for mounting purposes of PCB and rarely to mount components on the board.
Given below is a flow chart of where back drilling fits into the PCB manufacturing process:
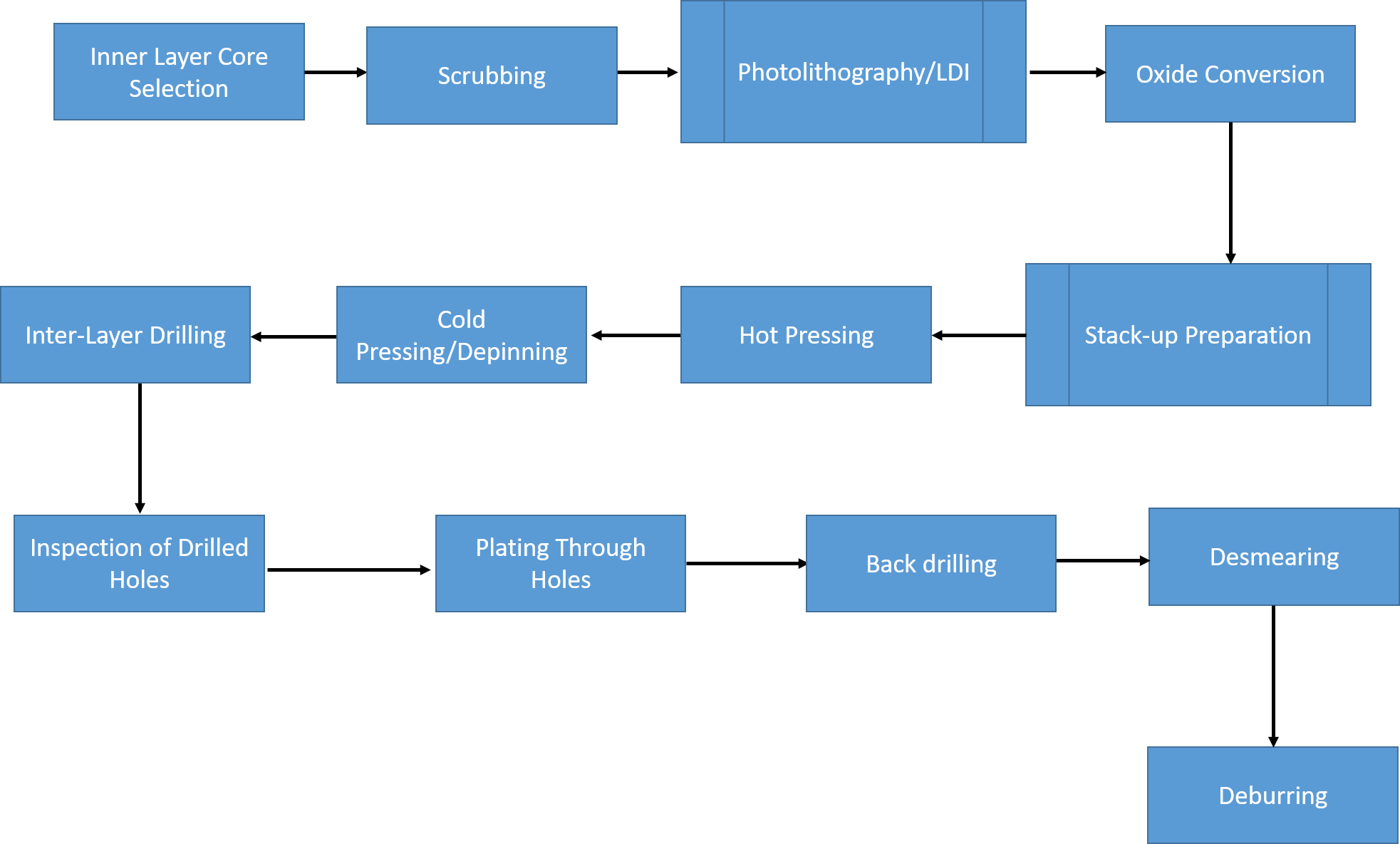
To learn about via design, read PCB Via Design Using Altium Designer
Back drilling example
Let us say you have a through-hole via going from layer 1 through 12 in a 12-layer stack-up. But the via is only meant for the signals from layers 1 to 3. So, a via stub will be created after layer 3 to layer 12, which will create resonance and reflections at very high frequencies.
It will attenuate the signals at the resonant frequency. Back drilling is performed to remove copper plating after layer 3 up to layer 12 to reduce the stub length. The back drill should be bigger than the original hole size to clear out the unwanted copper.
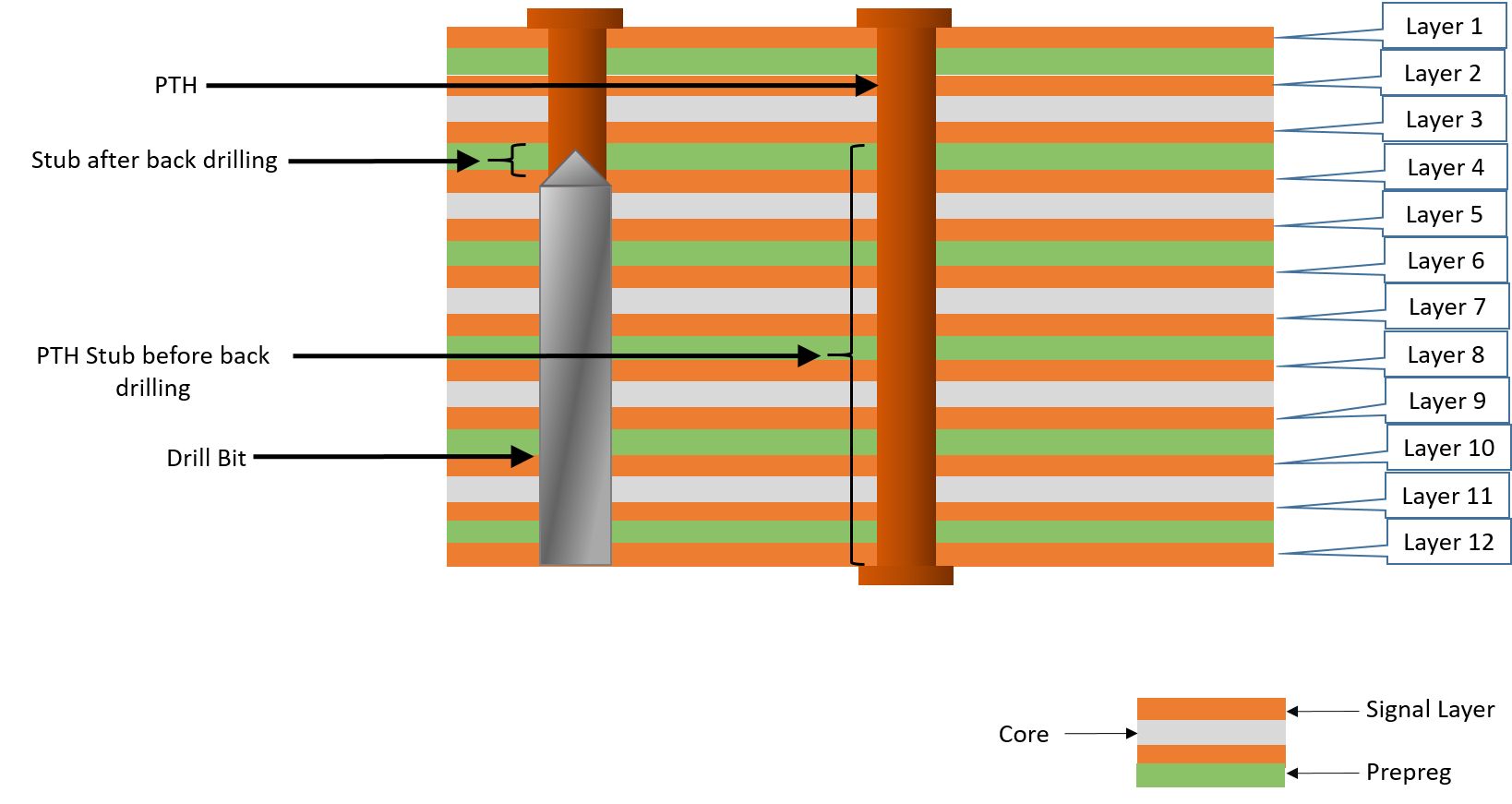
Back drill DFM tip
The back drill diameter needs to be slightly larger than the primary drill diameter. The back drill bit size (diameter) is usually 8 mils over the primary drill size, with 10 mils larger preferred.
Trace and plane clearances need to be large enough that the back-drilling process does not accidentally drill through traces and planes located adjacent to the back-drilled hole. Minimum plane and trace clearances (spacings) of 10 mils are preferred.
Back drilling from a manufacturing perspective
You can note that alternate construction techniques could also be used to minimize stub length. These include laser-drilled vias (microvias), or blind and buried vias, and alternative stack-up arrangements – where traces are moved to layers closer to the end of the via stub.
Also, back drilling is not necessary for high-frequency (greater than 3GHz) boards since alternative strategies are used to reduce signal reflection.
However, in many high-density PCBs and backplanes/midplanes, these options are not always viable from both manufacturing and cost standpoints.
In such a scenario, the only option is to remove the via stub by back drilling. Back drilling is necessary for high frequency (greater than 1GHz within 3GHz) boards when blind vias are not viable.
Back drilling terminology
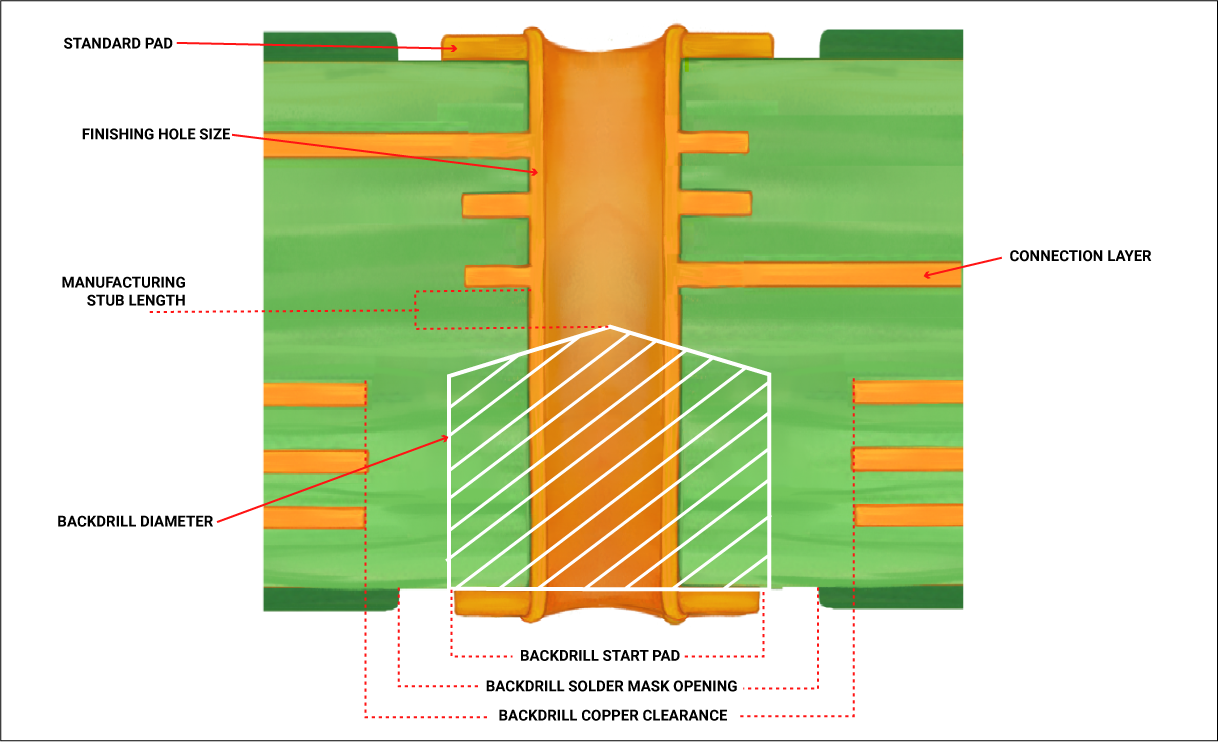
Advantages of back drilling PTH vias
- Via stubs give rise to a signal distortion issue named deterministic jitter. Jitter with regard to signal transmission in a PCB refers to timing errors caused by EMI, signal crosstalk, and noise. Deterministic jitter can be defined within the minimum and maximum variations.
- The Bit Error Rate (BER) is the number of bit errors per unit time and is largely dependent on deterministic jitter. Decreasing the deterministic jitter by back drilling will considerably decrease the overall BER of the signal.
- Reduces signal attenuation because of enhanced impedance matching and mitigates EMI/EMC radiation from the stub
- Reduces excitation of resonance modes.
- Decreases via-to-via crosstalk.
How much residual stub length can remain?
Once you decide to back drill, you will need to decide how much residual stub length can remain. The decision will depend on several interrelated factors including the desired signal integrity performance and practical (cost-effective) manufacturing considerations and limitations.
Usually, increasing the number of vias that need to be back-drilled and decreasing the maximum residual stub length will increase the manufacturing costs of the PCB/backplane. Given below is a table that details the signal loss corresponding to a residual stub length.
Remaining Residual Stub Length (mils) | Approximate Signal Loss (Percent) |
---|---|
1 | 0.25 % |
2 | 0.5% |
5 | 1.25% |
10 | 2.5% |
20 | 5% |
40 | 10% |
60 | 15% |
100 | 25% |
200 | 50% |
Approximate signal loss for various stub lengths (typical 6.25Gb/s backplane/midplane construction)
Controlled depth drilling from a design perspective (using the Altium Designer tool)
Here are the steps required to set up a back drill via according to the requirements:
Selecting the circuit segment
In this demonstration, we are choosing the ethernet section, and within the ethernet section, we are choosing the RX segment.
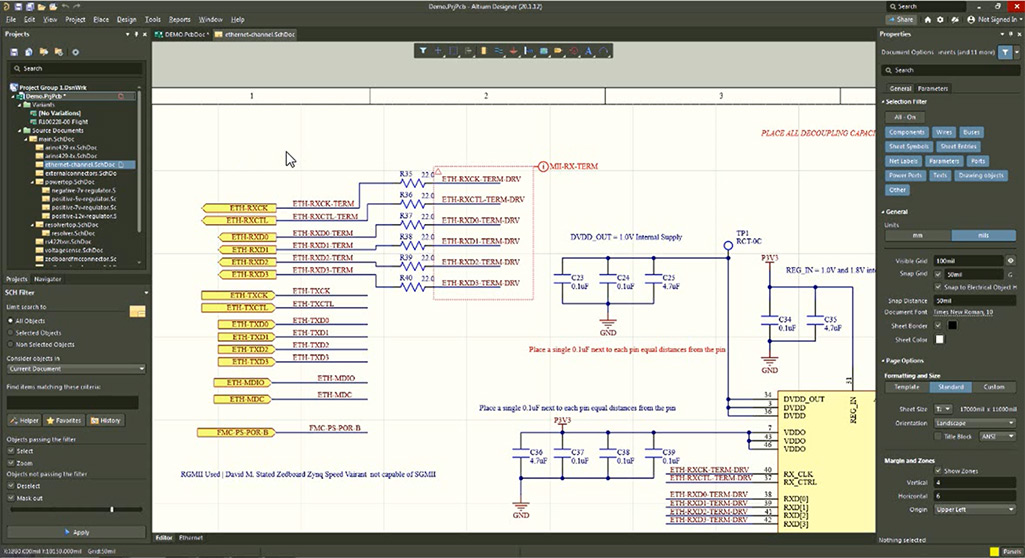
Before we take up routing, we need to carry out the back drill setup.
Adding a back drill via
Go to Design and then Layer Stack Manager. Over here we need to add a back drill via.
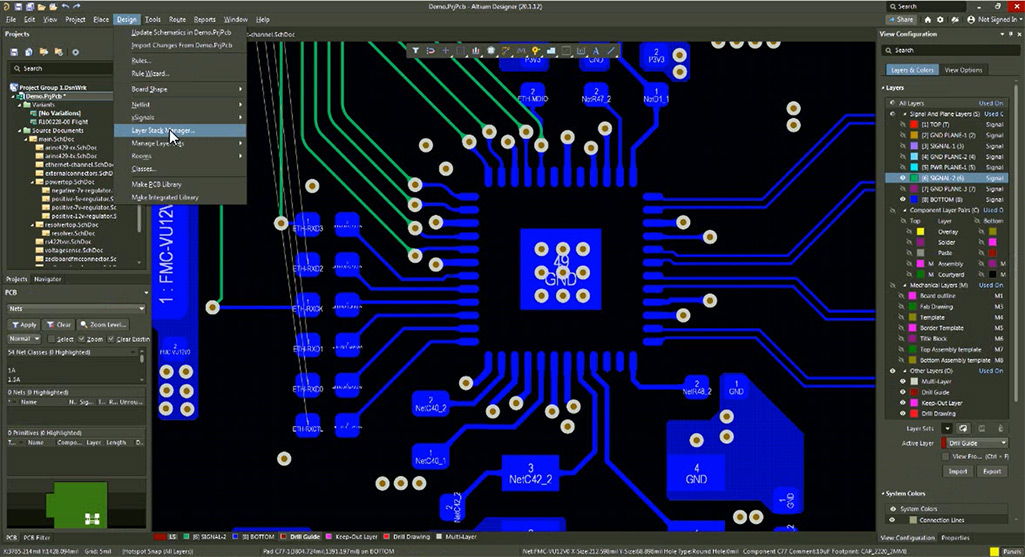
To do that, click the Features tab at the top right corner of the screen. Within the drop-down list, select the feature called Back Drills.
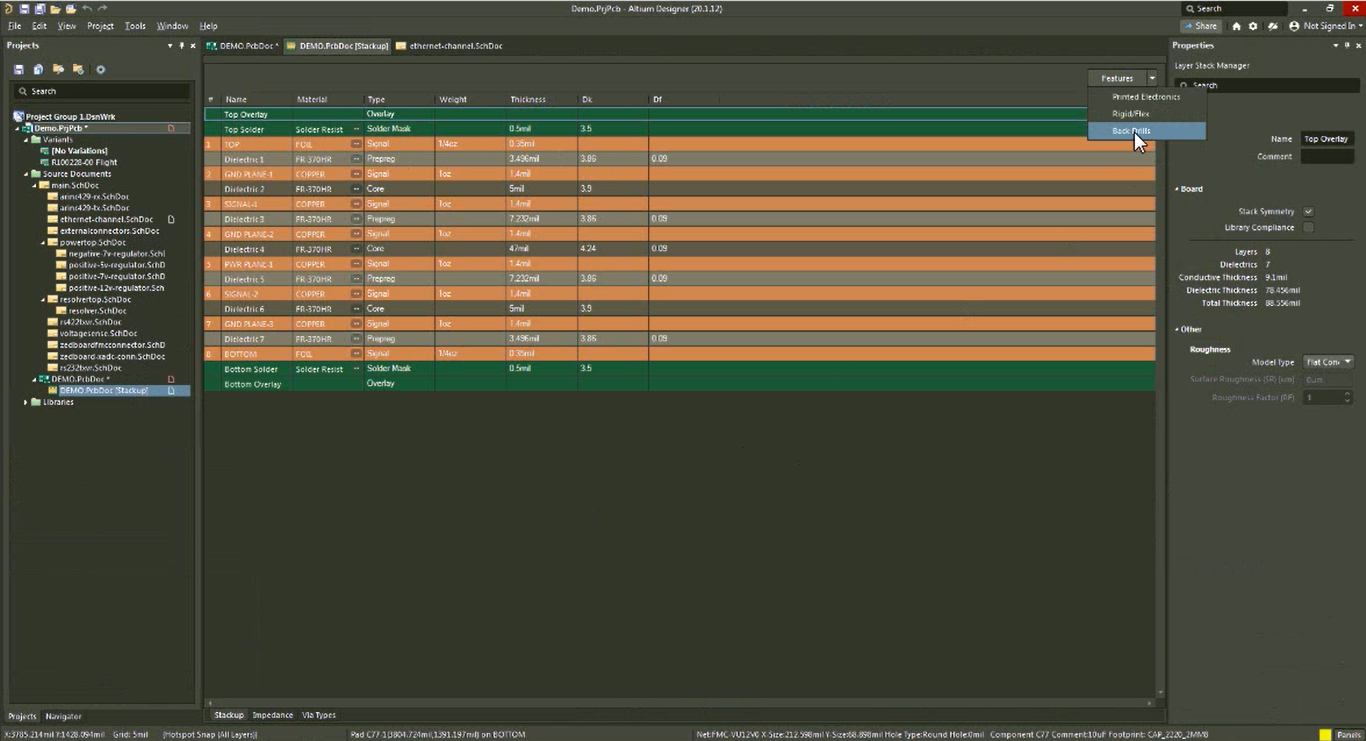
After that, at the bottom left portion of the screen, select the Back Drill tab. Once you click that, the back drill option is displayed. This is where you will get to add the various back drill parameters.

By clicking on the plus tab, you can add more back drills. You can also use the delete option shown with a bin symbol, to delete back drills you don’t require.
Selecting the start and stop layer
In the Layer Stack Manager, you can select the First and Last layers from the Properties panel on the left side. Here we are selecting the top layer as the first layer and the fifth layer as the last layer. You can see that the backdrill figure will also change to reflect your selection of the first and last layers.
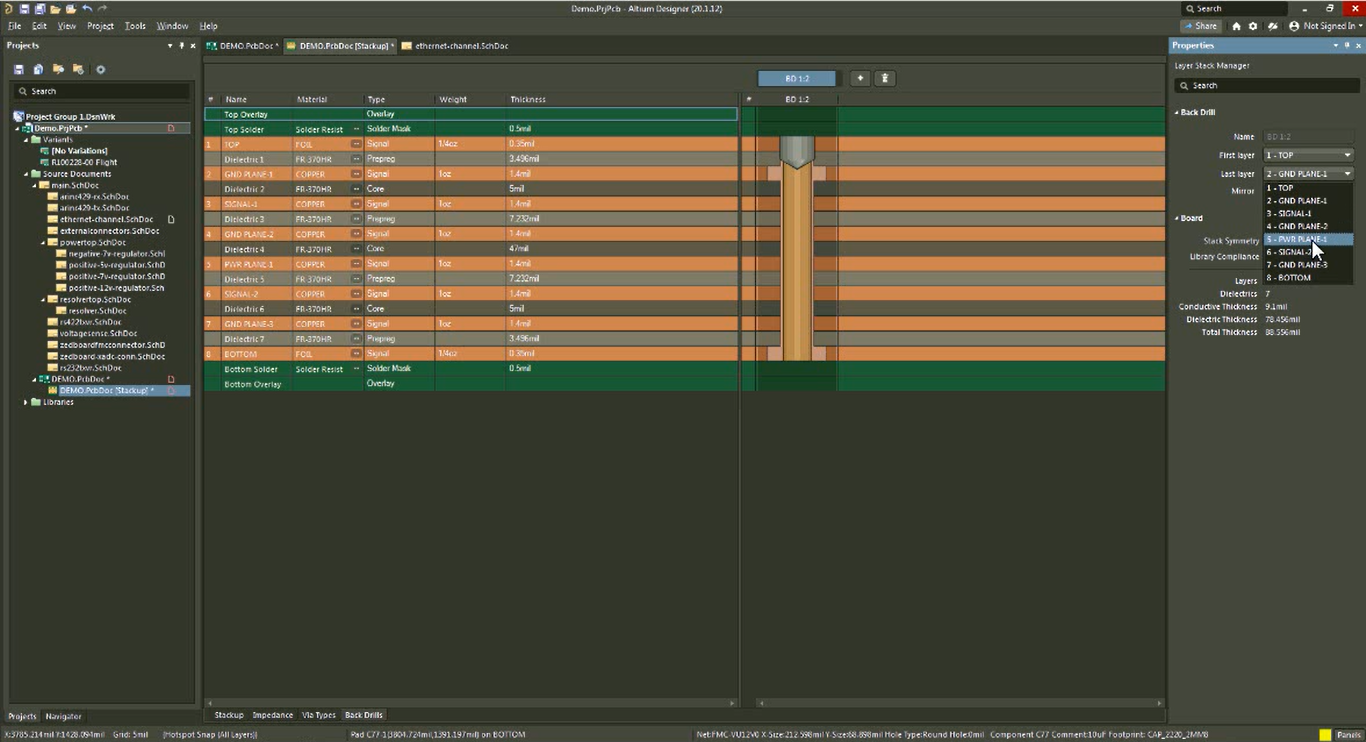
Now save your work in the Layer Stack Manager and click Close.
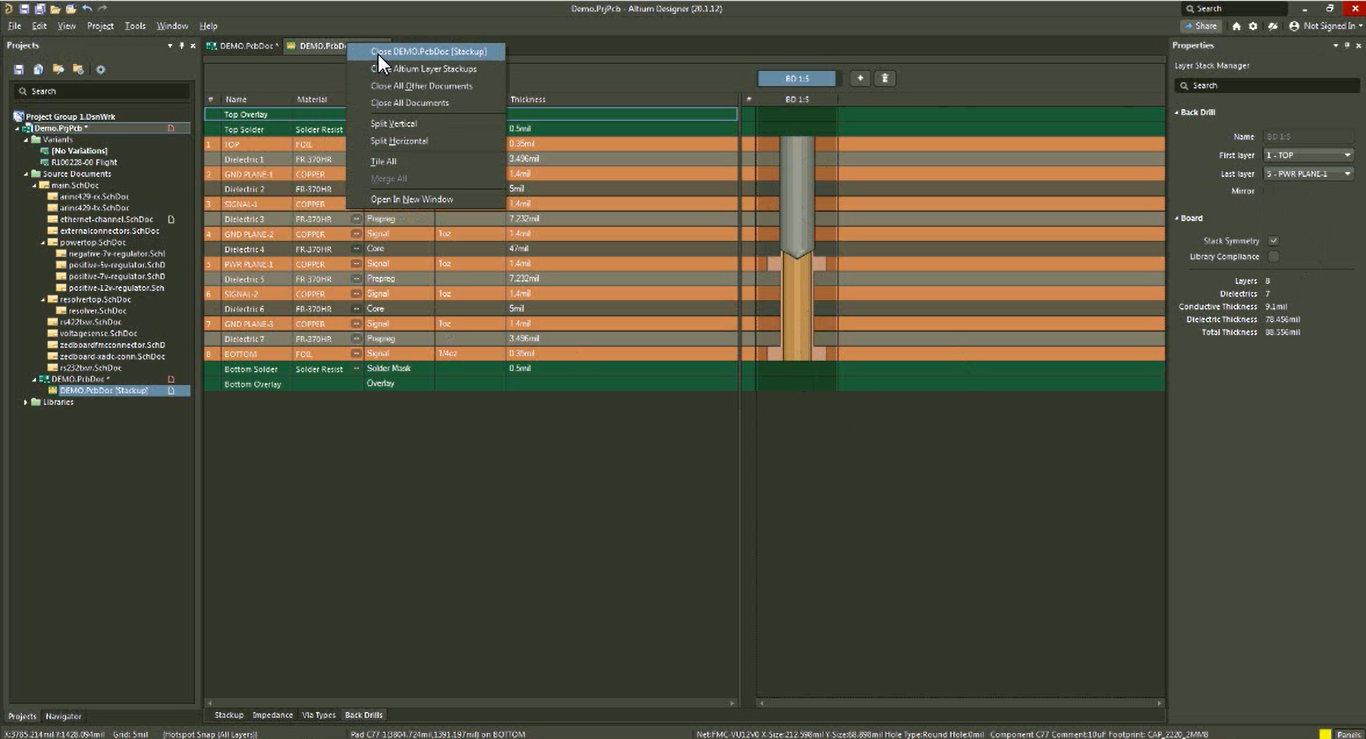
Next, go to Design and click on Net classes.
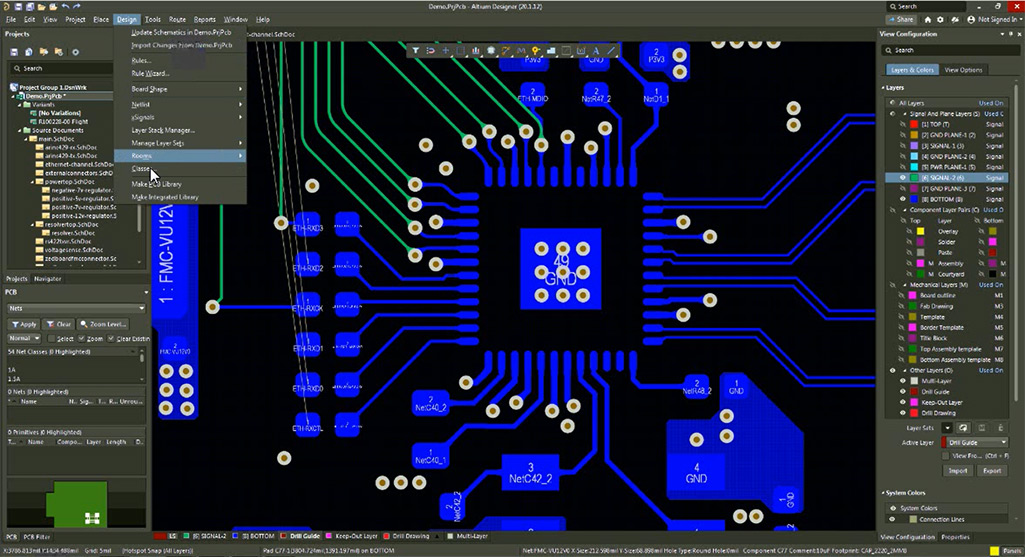
This will open the Object Class Explorer window. Then, right-click on Net classes and select add class in the drop-down menu. Now you need to name the class as backdrill.
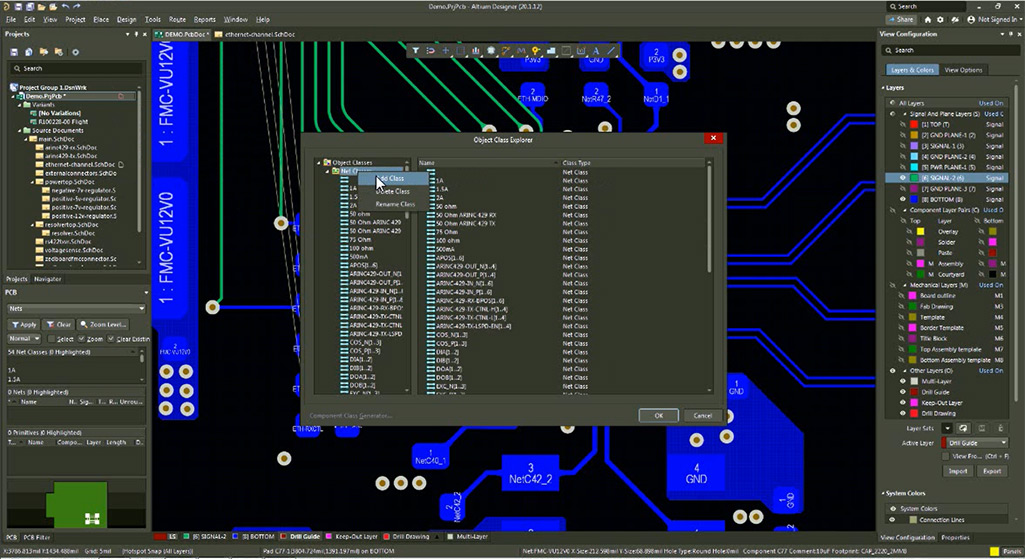
Now you need to add the nets which need backdrill vias. We will select the ethernet RX nets and click on the > icon to add the nets as members for the backdrill operation. Click OK.
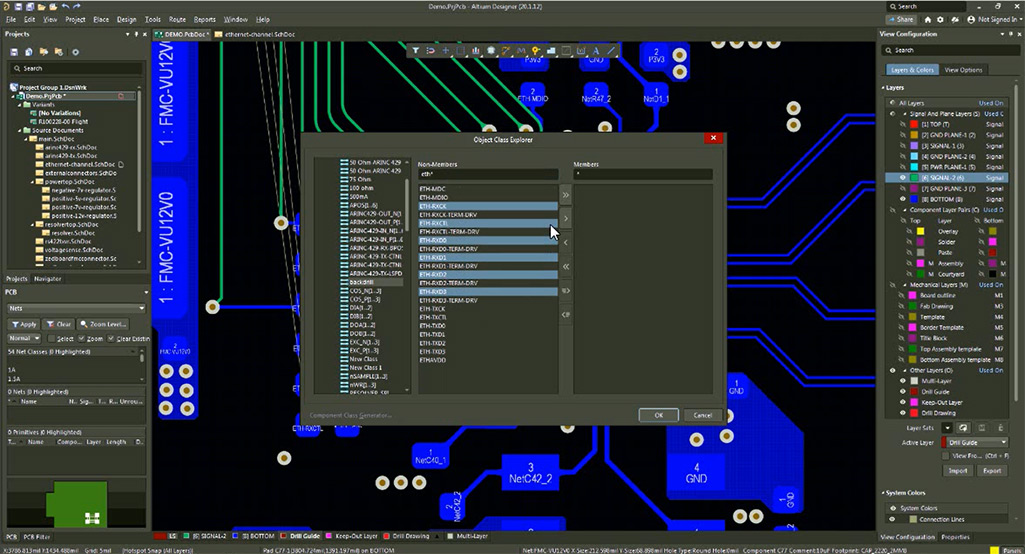
Adding a design rule
Next, you need to set the stub length and the oversize parameters. Go to Design and then click Rules.

Back drilling addresses the issues regarding signal integrity and resonance in vias. Hence, manufacturers and designers need to consider the use of back drilling in order to maintain signal integrity in high-speed signal PCBs.
The PCB Rules and Constraints Editor will be displayed. Select High speed and click Maximum stub length.
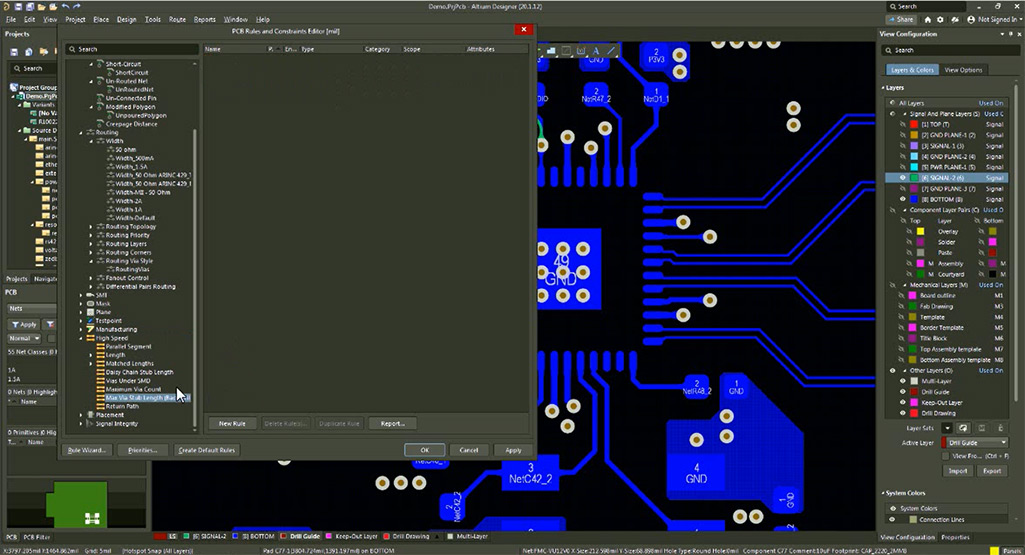
Click the New Rule tab at the bottom of the screen.
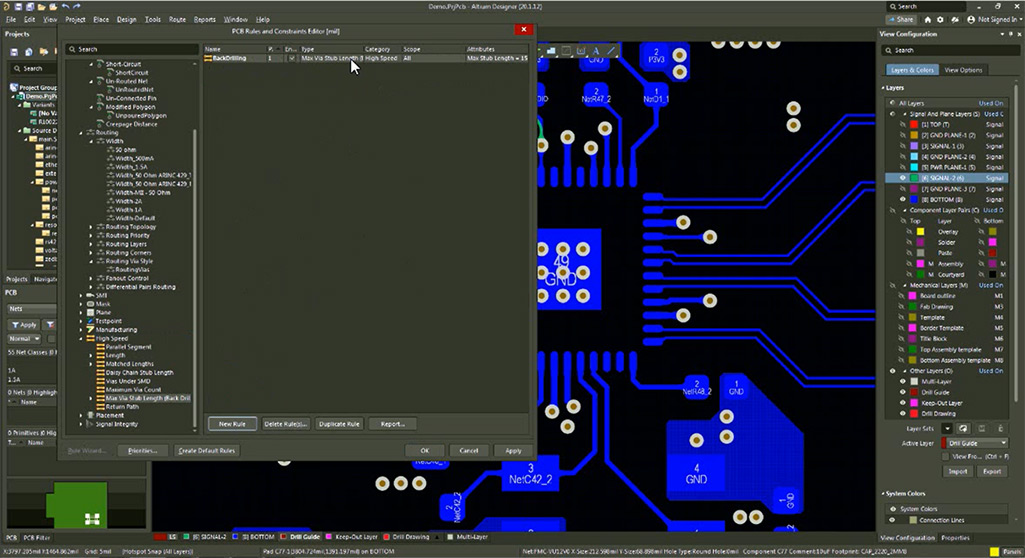
The back drilling rule is then added. Now, double click the rule to set the required values.
After this, select the net class and then select back drill. Click Apply, then OK. The next step is to perform the required routing.
We are going to keep the stub length as 15 mil. This is the oversize of the back drill which we will set as 10 mils. The tolerance will be set as plus and minus 3 mils.
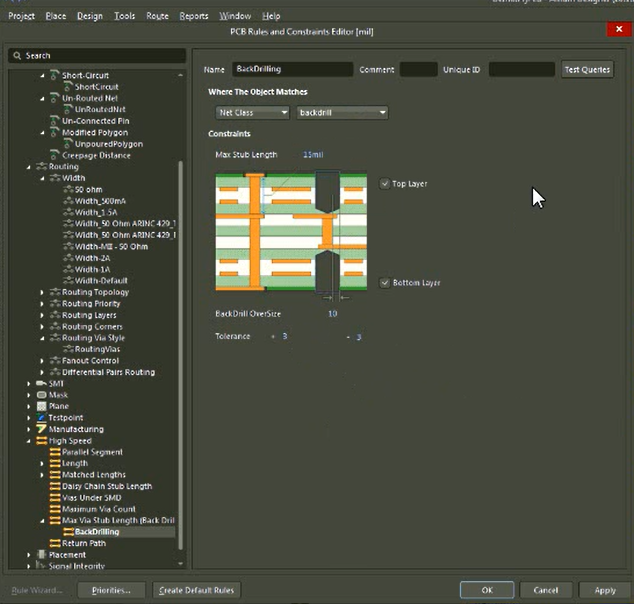
Checking the back drills
Once the routing is done, we need to check if the back drills have been set properly. To check the same, switch on all layers. You can see that the circumference of the vias is displayed with dual colors.
In this case, the red color indicates the First Layer or start layer and the blue color indicates the Last layer or stop layer.
You can clearly see the difference between the back drilled vias and the other vias. Only the back drilled vias show up in dual colors.
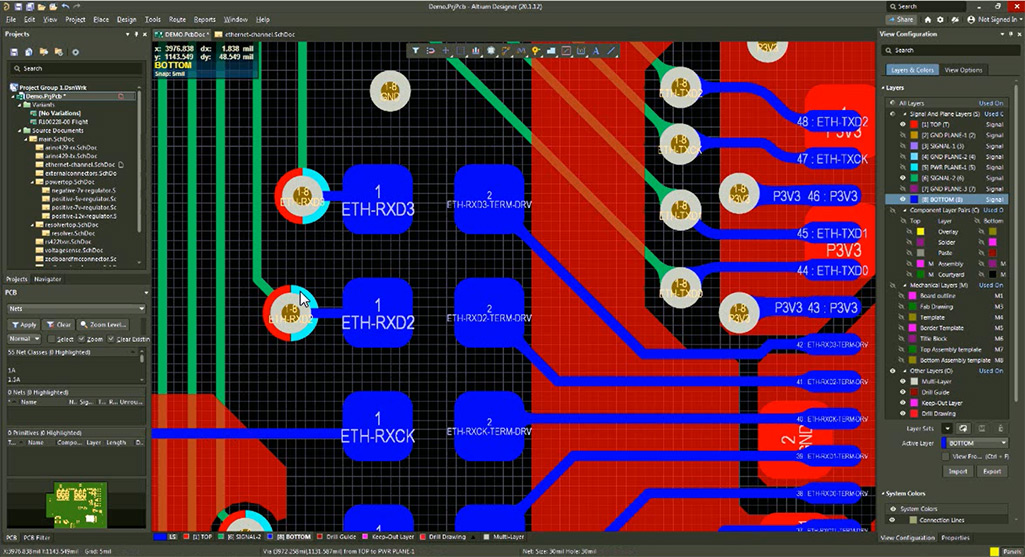
To view how many vias and PTH, and other holes have been drilled, select the Place option from the main menu and click Drill Table.
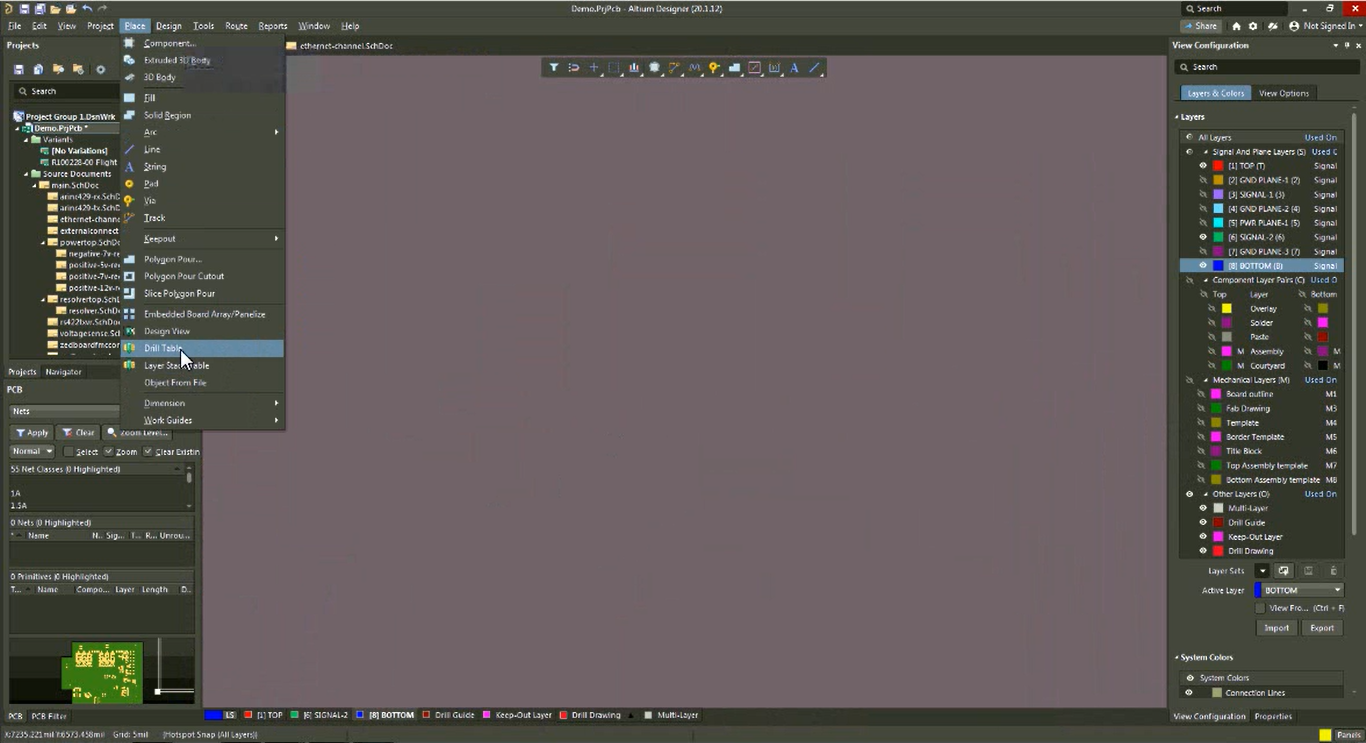
Viewing the Drill Table
You can select and view vias according to their properties using the Property option and selecting the required Layer Pair. Here you can see the Drill count is 12, Hole Size is 30 mil, type of plated hole is NPTH, and the drill hole tolerance as well.
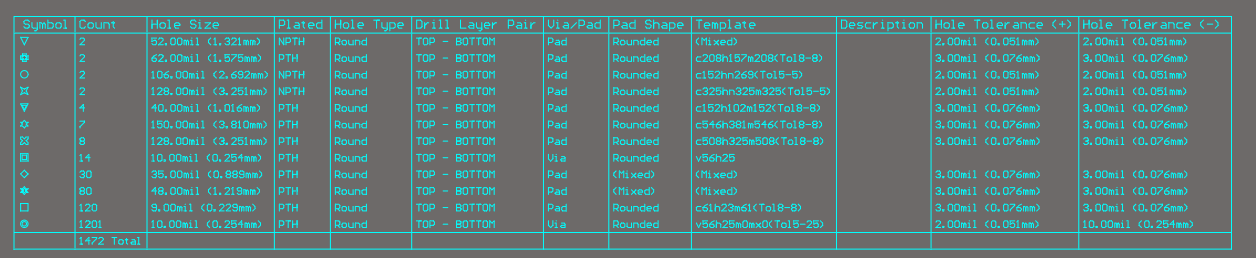

Back drilling addresses the issues regarding signal integrity and resonance in vias. Hence, manufacturers and designers need to consider the use of back drilling in order to maintain signal integrity in high-speed signal PCBs.
Back drilling FAQs
Q1. Why is back drilling also called control depth drilling?
A- Back drilling is also known as controlled depth drilling, as these holes are back-drilled to a predetermined, controlled depth.
Q2. What is the maximum stub length that can be retained after back drilling without significantly affecting signal integrity?
A- 10 mil
Q3. Name alternate construction techniques that could be used to minimize stub length other than back drilling.
A- Laser-drilled vias (microvias), or blind and buried vias, and alternative stack-up arrangements where traces are moved to layers closer to the end of the via stub.
Q4. What is the main manufacturing parameter to consider in back drilling?
A- Hole depth or Z-axis depth.
Q5. Why are smaller stub lengths (<10 mil) hard to achieve during back drilling?
A- Minimizing stub length below 10 mil calls for more accuracy in the drill machine, which makes it more challenging. Also, it increases manufacturing costs; hence, it is difficult to reduce stub length. If your manufacturer is using the latest drilling equipment, there is a possibility of achieving 2 to 3-mil stubs. Check with your manufacturer.
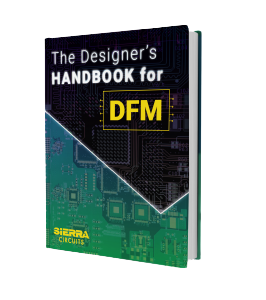
Design for Manufacturing Handbook
10 Chapters - 40 Pages - 45 Minute ReadWhat's Inside:
- Annular rings: avoid drill breakouts
- Vias: optimize your design
- Trace width and space: follow the best practices
- Solder mask and silkscreen: get the must-knows
Download Now