Contents
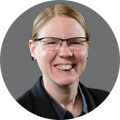
On-demand webinar
How Good is My Shield? An Introduction to Transfer Impedance and Shielding Effectiveness
by Karen Burnham
As you know, we’re a circuit board manufacturer that supports IPC-2581. We recently met with two Consortium members, Michael Ford from Aegis and Hemant Shah from Cadence. This was the perfect opportunity to ask them a few IPC-2581 FAQs.
The IPC-2581 questions
In this article, we will cover the main concerns PCB designers have about IPC-2581:
- IPC-2581 FAQs compared with other standards
- ECAD tools output
- Intelligent testing
- Schematics information
- Manufacturing
- Editing and traceability
- SMT programming
What are the advantages of IPC-2581 over older generic standards, like GenCAM or ODB++?
Hemant Shah: The majority of the people today, believe it or not, use Gerbers.
I would contrast it to Gerbers. So, 80-plus percent, probably 90-plus percent of the people today, use Gerbers. Gerber is a format that was first conceived in the 1980s, and it has evolved a little bit; 274X has come out and it’s gotten better. But it is a photoplot format. It is artwork, essentially.
There’s no intelligence in it. What IPC-2581 offers is intelligent data. You have intelligent data in your design, and there’s no need for you to dumb it down into artwork to then give it to somebody else that has to reverse engineer that into intelligent data to then go fabricate the board or assemble the board.
What IPC-2581 offers is an intelligent transport and handoff of design data to manufacturing so that the intelligence is preserved, the relationships between elements that are required to manufacture boards are preserved.
ODB++ can also be used for that.
H.S.: Correct. ODB++ is also an intelligent format. In fact, IPC-2581 was actually created with the combination of GenCAM and ODB++. ODB++ donated their standard to IPC, and what came out was a better standard IPC-2581, which is a super set of ODB++ and GenCAM. So that’s one part.
The second part is that ODB++ is a proprietary format, so if you’re not a customer, a paying customer of ODB++ or their tools, you are not likely to get the same level of support that you would need to address your issues if you ran into any issues. That tells me that it’s not the standard; it is a format for a particular company’s CAD tool.
Are the ECAD tools able to output IPC-2581?
H.S.: Yes. All of the ECAD tools output IPC-2581, so that’s the great news. All the vendors do it. We also have companies that do analysis that import and export IPC-2581. We have companies that have PLM software; they import and export IPC-2581. We also have software companies that support the manufacturing space; they also import and export IPC-2581.
So DFM companies, EDA companies, analysis companies, testing companies… All of them support IPC-2581.
How does IPC-2581 help intelligent testing?
H.S.: All of the data required for testing is included in the test data. So not just the netlist; anything else that’s associated with the test pads, etc., all of that is included in IPC-2581.
It’s defined. From your design, it takes it and puts it in IPC-2581.
Whatever your CAD tools support for testing instructions and testing data, that is transferred. It doesn’t invent anything new out of that, but it makes it easy for you to transfer the test intend in electronics.
IPC-2581 is a way for you to communicate your intent. Whatever you have to do in your native tools to create that intent will still exist. And tools will be different. Some tools do it easy, some do it difficult, right? So whatever you’re doing or creating design intent or testing intent in this case, that same thing will exist but IPC-2581 enables that data to be transferred easily.
Are the schematics information completely there?
H.S: The netlist data is the format and is completely there. Cadence is there. Bill of materials is there. So you have everything to manufacture your board with any variations that you want.
Are there any specific guidelines designers should follow to make the data their own?
H.S.: Every tool has a different sequence of steps that they follow to output the data. For Cadence, we asked the Consortium members who’ve used Allegro to output IPC-2581, we asked them to document it. It’s a simple one-page sequence of steps. Here are the steps you take to produce IPC-2581. Very simple format.
And we went to the Consortium members because they have done it, it’s proven, and they’re doing it on a daily basis.
What if designers forget to remove some traces, planes, etc. that could create a problem in manufacturing when they create a Gerber? Can IPC-2581 handle these issues?
Michael Ford: One thing that you have to remember is that the Gerber data isn’t the design data. It’s a graphical output that’s intended for use in fabrication. So the actual outlines of things, I mean, even these kinds of fragments of design that you’re talking about, they aren’t necessarily part of the original design.
When creating the Gerber, it adds in various elements to compensate for the manufacturing process. This actually introduces errors and potential mistakes. So this is kind of like a correction process for that. With IPC-2581 there should not be these kinds of issues. And if there are, the designer needs to be called to task. But you should find that IPC-2581 data is clean and immediately usable.
Also read: How to Export Gerber and Production Files in Altium Designer
Could you elaborate on the use of IPC-2581 in Industry 4.0?
M.F.: The data for all of manufacturing is contained within one file. Now, there are various elements that different machines will require. And so, whether it’s location of components, component shapes and geometries, whether it’s test points or anything like that, you could say it’s kind of a translation. You choose which machine in the line will perform each task and then you allocate the data accordingly. But what you mustn’t forget is that the line isn’t only machines. There are people also doing manual assembly operations.
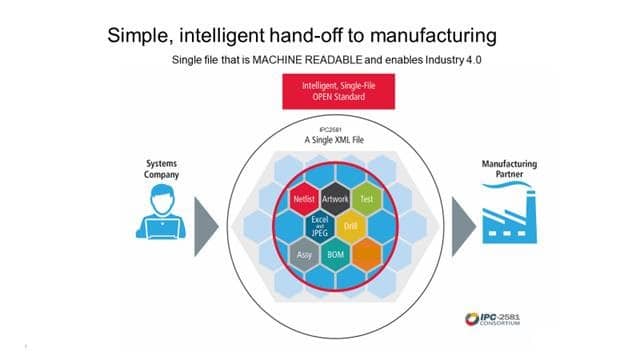
And so the IPC-2581 file includes the base information with which to create documentation such that when we assign jobs to manual operators which typically today in a modern factory will be using paperless operation with lots of little videos in there to it, show exactly how things are done, we want to make sure that we reference the exact design intent as part of that documentation so that there’s no kind of challenges to, well, this document shows this but this document, it seems different. That happens today but it all comes from the same source. Through IPC-2581 it’s the same consistent data.
What happens with IPC-2581 when a manufacturer modifies the original customer’s data for manufacturing?
M.F.: The real challenge is to make sure that the designer’s intent is captured and that should any modifications be made that they are consistent with the designer’s intent and also that we have information fed back to the designer. So at the moment if people are using Gerber and making manual editing that there’s no track of reference. You don’t know what somebody did.
If something then later goes wrong who has the responsibility? Very, very difficult to go back. One example is that you have any products these days where you have a lot of different variations. Some of those variations are driven by the features of a particular product, some of them are driven by cost performance, you know, reducing the cost, exchanging materials or changing layouts a little bit. So I understand how these kind of changes are made and to save time you can implement them within manufacturing.
So with IPC-2581 you’ve got the original digital content.
M.F.: Yes, and by editing that original content you could then create the record of that change being happened. This is all subject to manufacturing and customer relationships because in many cases it should be spun back to the original designer.
But for example, where materials to be used are obsolete and you need to substitute a different material with a different package shape so you have a different land pattern, you need to change the design. Does that go back to the designer who forgot about this design two years ago? And, you know, it’s going to take a long time for him to get back up to speed.
Or could we modify it locally and just do it, just get it done. But let’s get it done in a way that we’ve got traceability so that everybody can understand that this has happened and can approve it, can see it. I think that is the answer.
So it is possible to do editing and also maintain traceability?
M.F.: Yes, absolutely. The really great things about IPC-2581 is that is an XML format which means that a human can read it and a system can read it. And so you can very quickly see if somebody were to change it. Then you can see where the change is and you can then sort of put a record to say who changed it and how it was changed.
But tools in manufacturing could also re-output an IPC-2581 and then you would be able to see the version difference.
In SMT programming, you create a SMT program based on X, Y data. Is this going to change in the IPC-2581 scenario?
M.F.: Yes. The market has changed significantly. Because the problem was always how do you optimize and SMT machine? Do you use an external software to be able to look at the line and then make the optimization? But then you send the programs to the machine and they have to change and then you end up with a line that’s not balanced. That kind of operation has almost disappeared now.
What the machine vendors can offer in an Industry 4.0 environment is to be able to make a very high level of sophisticated optimization, not just for this product that we’re making.
But what is the next one coming, and the next one and the next one? Where are my common factors for my feeder setups? The machine vendor knows best of all how to do that. But what they don’t have until now is the reliable information with which to do that. And the reason for that is because it used to take so long to get all of the information, sort it out, correct it, revised, checked, signed off, trials done. With IPC-2581 you don’t do any of that. You simply have the data, you know it’s correct, you send it out. And the machine vendors can optimize their own environment.
Imagine you have the IPC-2581 files of ten jobs which have to be done in succession by a set of lines. Can you send them all to the machines and everything will be taken care of?
M.F.: Yes, absolutely. And today that’s a luxury. It’s a feature that many machine vendors offer and it provides a better support. In the future when we’re all Industry 4.0 that is essential. Nobody will be able to not do that.
What should designers know about IPC-2581?
H.S.: IPC-2581 has all of the data that you need to manufacture a board. So a designer today has to integrate the Gerber files, the drill file, the netlist file, and all of the different instructions that you have are created in multiple different file formats, and they have to be correlated. If a designer was creating an output format, he gets interrupted, and he forgets to output a file or he changes the design and doesn’t re-enter the files, then the dataset sent to the manufacturer will be inconsistent and it will be the designer’s fault, right?
So if the designer makes a mistake, the designer has to pay for it. The designer’s company has to pay for it. It’s the same thing when you pass it on to a manufacturer. If a manufacturer makes a mistake in reverse engineering that dataset, the manufacturer pays for it.
And there’s no need to do this because you’re going from intelligent data in your board to intelligent set up on your manufacturing floor. Why to dumb down that information? There’s no need to. Push a button, create an output in IPC-2581, and send it to your manufacturer. If you’re wanting to send only fabrication data, IPC-2581 supports that. If you want to send just the assembly data, IPC-2581 supports it. Just test data, you can do that.
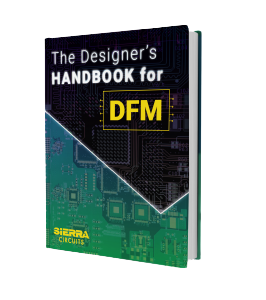
Design for Manufacturing Handbook
10 Chapters - 40 Pages - 45 Minute ReadWhat's Inside:
- Annular rings: avoid drill breakouts
- Vias: optimize your design
- Trace width and space: follow the best practices
- Solder mask and silkscreen: get the must-knows