Contents
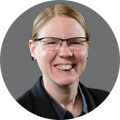
On-demand webinar
How Good is My Shield? An Introduction to Transfer Impedance and Shielding Effectiveness
by Karen Burnham
Modern electronics manufacturers often face contradictory requirements when integrating complex circuits into a finished application. The product needs to be light in weight, yet durable enough to survive in environments where heat, vibration, and moving parts would tax traditional connections. Additionally, manufacturing cost means that circuit integration cannot involve a lot of expensive, error-prone human assembly: it requires the repeatability and quality levels of IC design. Finally, product lifecycles demand rapid prototyping and implementation, as time to market can make or break a product line. Flexible printed circuit boards offer advantages in all of these areas and can be used in a wide range of applications, from medical and aerospace to consumer electronics.
If you have been a regular user of electronic devices at any point in the past 30 years—or have just looked up at the procession of phones, laptops, and MP3 players—you have likely noticed some dramatic design changes. For starters, many of these devices have gotten progressively smaller.
Innovations like flexible PCBs offer significant amounts of design freedom, so products can be both lightweight and durable, as well as assembled as part of a streamlined and highly efficient economy of scale. With that in mind, let’s look at how flex PCBs differ from rigid PCBs and how they can enable a wide range of advantages—from more compact devices to fewer errors during manufacturing.
What Is a Flex PCB?
As the name suggests, flex PCBs are flexible circuits with very thin substrates and high levels of bendability, tensile strength, and physical flexibility. They can also be molded into complex three-dimensional shapes for use across a diverse range of applications, such as heads-up displays for aerospace piloting, wearable technology, and minuscule devices (e.g., modern hearing aids) for medical care.
The material used in flex PCBs can be just a few microns thick, yet still, be reliably etched. This often makes them preferable to rigid PCBs in certain applications, in addition to the benefit of removing traditional wiring harnesses and ribbon connectors, in particular contexts.
For example, a flex PCB can be routed at tough angles within the tight confines of a device such as a satellite, while still sporting a sufficiently high conductor density.
To know more about flex PCBs used in satellite applications read our article Flex PCBs in Satellite Applications: Lighter Than the Clouds.
This adaptability is not possible when using ribbon cables. Moreover, flex PCBs unlock many physical design advantages, including:
- 360-degree bendability.
- Superior resistance to vibrations and other disruptions within harsh environments.
- Support for compact, lightweight design; product weight can be greatly reduced.
- Small, flexible cables that take up less space than typical wires.
- The ability to be warped or contorted without any associated breakage.
On the manufacturing side, flex PCBs are similarly advantageous. They permit better airflow and heat dissipation than many other PCBs. Their modest counts of interconnections and components also mean that their assembly costs are much lower than those for traditional wiring harnesses. Plus, there is less overall susceptibility to assembly errors, since the manufacturing process is streamlined and standardized, without the problematic manual input required for building many of these harnesses.
Flex PCBs are often the best choice for connecting complex electronics internal systems. Flexible circuits are ideal for devices within the aerospace, medical and consumer technology fields, as they are more versatile and—dare we say—flexible than their rigid alternatives. Thinner, more compact products are an obvious result of flexible circuits as well.
To know the applications of flex PCBs in the medical industry read our article Why Are Flex PCBs Used in Medical Devices and Wearables?
Why Should You Go for Flex PCBs?
Flex connections have mechanical advantages over conventional ribbon cables in various applications but in some cases, they also have better chemistry.
A flex circuit can be formed in complex shapes in three dimensions with branches to multiple connectors, which would be impossible to achieve with a ribbon cable. Moreover, flex circuits can be interfaced with rigid boards without the relatively tall and bulky connectors flat cables require, or in the case of rigid-flex construction, they can be integral with the boards and eliminate external connectors altogether. Furthermore, the conductor density of flex circuits can far exceed that of ribbon cables.
There are some subtle advantages of flex circuits versus conventional ribbon cables beyond the many clear distinctions. One of the materials commonly used for flex circuits, Kapton, has extremely low outgassing in ultra-high-vacuum environments, such as space. Though Kapton-insulated ribbon cables are available, they have a limited number of conductors and cannot be routed at angles in tight confines.
Ribbon cables insulated with Teflon and other plastic materials outgas fluorine or reactive compounds when subjected to high vacuums, which can attack electronics in closed containers if care is not taken to completely vent the gases.
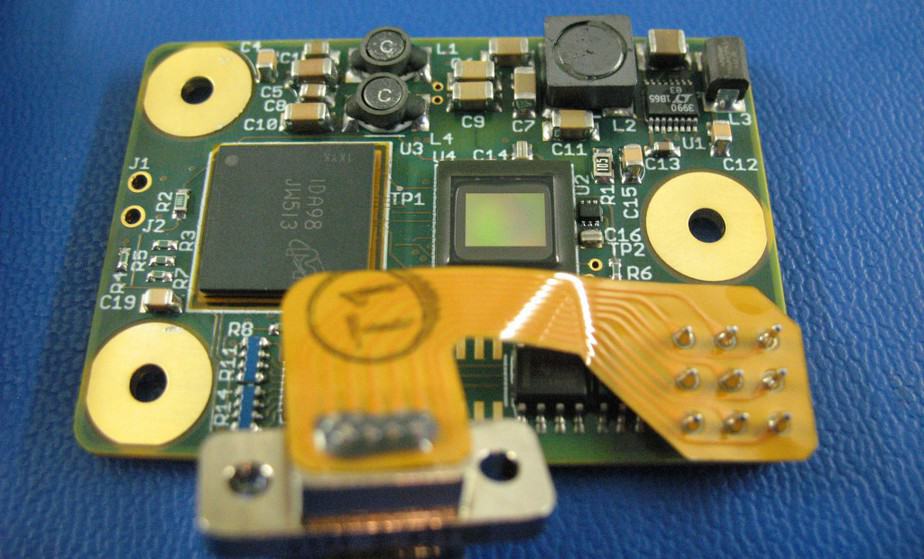
The Space, Weight, and Cost Savings of Flex
Redesigning a product to use flex PCBs rather than rigid PCBs delivers immediate benefits in weight. Customers commonly see weight reductions of up to 75% when compared to traditional designs. This comes from using incredibly thin substrates made of polyester or polyimide material—films that can be as thin as 12-120 microns thick. Conductive material traces are etched on the flex PCB, in as many layers as the PCB design requires. Typically, a coverlay is then applied to protect the layers from moisture, dirt, and damage.
One important use of flex PCB design is the replacement of wiring harnesses and ribbon connectors once used to link together different boards—for example, to connect the engine control unit in an automobile to the dashboard or lighting components. The standardization and economy of scale that goes along with this also reduces assembly cost by reducing the number of components and interconnections and allowing for high-quality mass production. Many flex PCB users find that they can reduce the cost of connections by up to 70% versus traditional wiring harness construction. And with the reduction in connection cost comes a reduction in costs associated with inconsistent quality—flex PCB’s standardized construction also eliminates the source of potential errors from hand-built harnesses.
The History of Flex PCBs
At the beginning of the 20th century, early researchers in the burgeoning telephone industry saw the need to alternate layers of conductors and insulators to produce standardized, flexible electric circuits. An English patent from 1903 describes coating paper with paraffin and laying flat metal conductors to provide the circuits. Around the same time, Thomas Edison’s notebooks suggested coating linen paper with cellulose gum, then tracing circuits on the gum with graphite powder. The late 1940s brought in mass production techniques, resulting in a number of patents for photo-etching circuits on flexible substrate as a way of replacing wiring harnesses. More recently, the addition of active as well as passive components to flexible circuits has introduced the term “flexible silicon technology,” referring to the ability to integrate semiconductors (using technologies that include thin-film transistors) onto the flexible substrate. The combination of traditional advantages found within flexible circuit construction combined with onboard computing and sensing capability has led to exciting developments in several areas, most especially in applications in the aerospace, medical, and consumer electronics fields.
Aerospace Applications
The heads-up display (HUD) as used in aerospace is a familiar technology with a clear purpose: displaying operational data directly in the pilot’s field of vision alleviates the need to look away from a potential target to read critical operational data during flight. A recent extension of the HUD, applied to wearable technology, provides remote 3D holographic images in a flip-down visor mounted to a helmet. The holographic waveguide helmet-mounted display (HWVD) from HoloEye Systems provides high-resolution true 3D imaging, using flexible PCB cables to drive the waveguide optical system, which uses HoloEye’s liquid crystal on silicon (LCOS) display technology. The flexibility, reliability, and performance of the flex PCB cables make the HWVD effective in realtime use for avionics, and the light overall weight makes it feasible to mount the display directly on the pilot’s helmet, instead of in the aircraft.
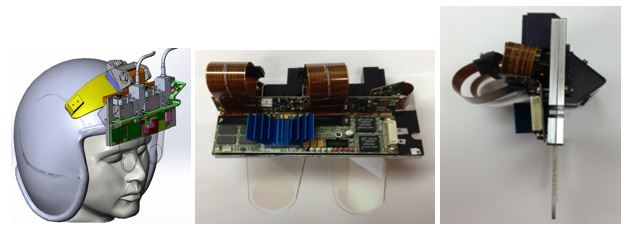
Medical Application
A medical device company utilizes flex PCB designs as important components of a new class of hearing-assist devices, providing higher range and resolution (125 Hz to 10,000 Hz) than currently available hearing devices. The underlying premise is revolutionary: a small photoreceptor and micro-actuator are placed inside the ear canal, with the micro-actuator in contact with the eardrum. Outside the ear, as in conventional hearing devices, a microphone captures the sound and a digital signal processor (DSP) converts it to digital signals to be sent into the ear. But here’s where things get exciting: the digital signals actuate an infrared laser located inside the ear canal, which in turn excite the photoreceptor, turning the digitized audio into a small current which drives the micro-actuator, causing the eardrum to vibrate.
Flex PCB design permitted the engineers to mount the microphone, DSP, and battery in a tiny, compact package that fits behind the ear, and which allows the laser to provide both power and signal to the passive photoreceptor and micro-actuator. While this is currently still an investigational device, the technology is promising and exciting.
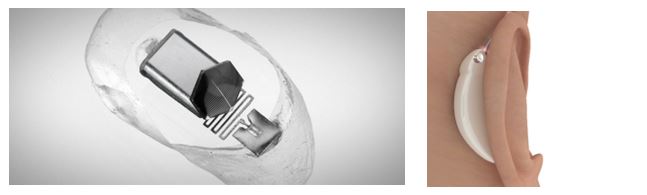
The amount of applications and uses for flex PCBs within the consumer industry is too exhaustive to list. But simply put: if you wear it, carry it, or drive it, there’s a good chance it has flexible PCBs in it.
The first flex PCB most people think of is typically the connector between the keyboard and screen of a laptop. Similarly, flip phones use flex PCBs to connect the two halves of the phone. The moving print head of modern printers use flex PCBs in place of the older-style ribbon connectors; likewise, the read/write head of disk drives—which require billions of flexing operations during the product’s lifecycle—have benefited from the increased reliability and cost-effectiveness of flex PCBs.
Automotive applications, in particular, carry a number of advantages, not only in the usual arena of reliability but even more so for the weight savings that a flex PCB offers compared with a standard PCB and wiring harness. Weight is the enemy of fuel efficiency (or range, for electric/hybrid vehicles), and flex PCBs greatly reduce the labor involved in manufacturing a traditional automotive wiring harness. And the inherent resistance of flex PCBs to vibration makes them ideal for the harsh environment inside a motor vehicle.
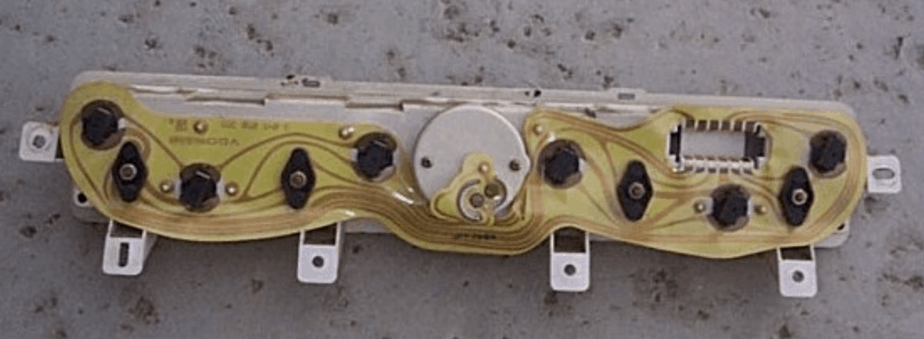
Whether for cost reduction, longevity, improved product quality or performance, flexible PCBs offer an effective way to connect the various modules of an electronic system.
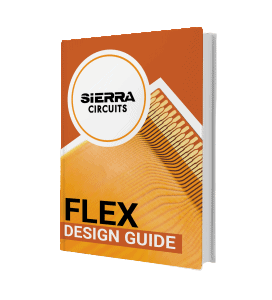
Flex PCB Design Guide
10 Chapters - 39 Pages - 45 Minute ReadWhat's Inside:
- Calculating the bend radius
- Annular ring and via specifications
- Build your flex stack-up
- Controlled impedance for flex
- The fab and drawing requirements
Download Now
Flex classification is crucial for identifying the type of flexible printed circuit board you are designing. Make sure you know what the standards and requirements are before beginning your design. This will save you time and effort in the long run. Let’s delve a bit deeper into what the different flex classes and types are, as well as the differentiators for both.
Flex Classification
Flex classes vary depending on the level of inspection and testing required, and the performance requirements of the finished product. There are three different classes.
Class One
Suitable For: General Electronic Products
Includes consumer products, some computer and computer peripherals suitable for applications where cosmetic imperfections are not important and the major requirement is the function of the completed printed board. Requires minimum inspection, testing, and performance standards. Applications include disposable electronics.
Class Two
Suitable For: Dedicated Service Electronic Products
Includes communications equipment, sophisticated business machines, instruments where high performance and extended life is required and for which uninterrupted service is desired but not critical. Requires medium inspection, testing, and performance standards. More expensive than class one, the applications of these boards include cameras, smartphones, and medical diagnostic equipment.
To know more about flex PCB manufacturing class, read our article Choosing IPC Class for Medical Flex PCBs
Class Three
Suitable For: High-Reliability Electronic Parts
Includes equipment and products where continued performance on demand is critical. Equipment downtime cannot be tolerated and must function when required such as in life support items or flight control systems. Printed boards in this class are suitable for applications where high levels of assurance are required and service is essential. Requires the highest inspection, testing, and performance standards. These are the most expensive flex boards. Applications include medical devices and military/aerospace electronics.
To know more about military-grade PCB specifications, read our article: Military-Grade PCB Design Rules and Considerations.
What Are the Types of Flex PCB?
Flex type depends on the number of conductive layers, construction and materials, and the presence or absence of plated-through holes.
IPC Type 1
Single-sided flexible printed circuit board. This is the most common type of flex circuit, ideal for dynamic flex applications. Contains one conductive layer. Can be found with and without stiffeners. SMT lands accessible only on one side.
IPC Type 2
Double-sided flexible printed circuit boards. Contains two conductive layers with plated-through holes. Can be found with or without stiffeners. Copper is bonded on both sides of the base material, then drilled, plated, etched and insulated on both sides by a top and bottom dielectric coverlayer.
IPC Type 3
Multilayer flexible printed circuit board. Contains three or more conductive layers with plated-through holes. The plated-through holes are used to create the interconnection of the conductive layers. Can be found with or without stiffeners.
IPC Type 4
Multilayer rigid and flexible material combinations containing three or more conductive layers with plated-through holes.
IPC Type 5
Flexible or rigid-flex printed circuit boards. Contains two of more conductive layers. No plated through-holes.
What Makes Sierra Circuits’ Flex PCBs and Processes Unique
Sierra Circuits is an experienced, reliable manufacturer of flex PCBs. What is special about how we approach flex? For starters, we serve as a single point of contact throughout the entire process of quoting, designing, ordering, manufacturing, and delivery. Plus, our flex PCB solutions have several key differentiators that make them suited for several use cases:
- We produce only the highest quality boards, with polyimide film and thin copper foils on trace and space as small as 50 microns. Even with this level of precision, we can deliver them to you on deadlines as short as 24 or 48 hours after ordering. Our process has been honed over nearly 30 years to provide as a one-stop shop that meets all your PCB requirements, from in-house fabrication to turnkey services.
- Our top-of-the-line flex PCBs have already proven themselves in applications in a wide range of industries and devices. Our boards have been used in handheld as well as implantable medical equipment. They can also be implemented in aerospace and automotive applications or in consumer electronics such as laptops.
- In addition, to flex PCBs, we also make rigid-flex PCBs and High-Density Interconnect (HDI) flex PCBs. Rigid-flex PCBs bridge traditional and flex designs and are often used to connect several rigid-flex boards using flexible circuits. HDI for flex PCBs may be needed to free up more space for other features on the board and make the most of the small package size.
Something else that sets Sierra apart is the level of assistance we offer during the design process. We have drawn up many guides for ensuring the best possible results for your prospective flex PCB, rigid-flex PCB, or HDI flex PCB. We have also published some of these tips on this blog, such as how you can get optimal flex stack-ups and use the best possible materials.
To learn more about flex design guidelines, watch our webinar Flex PCB Design Guidelines for Manufacturing.
When manufacturing flex PCBs, we use only state-of-the-art machinery for the completion of crucial tasks such as laser drilling and direct imaging. All of our design, manufacturing, and assembly is done in a spacious, high-tech facility in Sunnyvale, California. From here, we offer an easy-to-reach point of contact along with quick turnaround times for the leading tech giants in the area. Sierra is also ISO 9001:2008, ISO 13485:2003, MIL-P-55110, and RoHS certified.