Contents
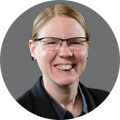
On-demand webinar
How Good is My Shield? An Introduction to Transfer Impedance and Shielding Effectiveness
by Karen Burnham
Flex PCBs are widely used in medical devices and wearables as they offer some great advantages. The demand for fitness wearables and medical devices is expected to increase even more in the upcoming years. Choosing an appropriate flex PCB manufacturing class is essential to ensure all the necessary requirements are met.
Before we talk about flex medical PCBs, let us have a look at the standard IPC classes.
Three IPC classes
The different manufacturing classes for PCBs were established by IPC, the trade association devoted to connecting electronics industries. The higher the quality standard, the higher the classification.
IPC class 1
Class 1 PCBs are classified as general electronic products.
IPC class 2
Class 2 flex PCBs are used in electronic products, such as cameras and smartphones.
IPC class 3
Class 3 PCBs are used in high-reliability electronic parts. This category includes any item in which the devices require 100% reliability and accuracy at all times. For example, medical applications generally use class 3 flex PCBs.
To understand the difference between class 2 and class 3 standards, read our article IPC Class 2 VS Class 3: The Different Design Rules.
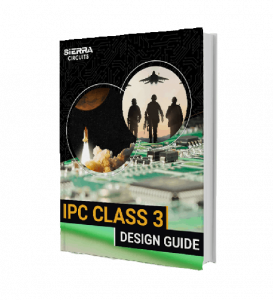
IPC Class 3 Design Guide
8 Chapters - 23 Pages - 35 Minute ReadWhat's Inside:
- IPC guidelines for manufacturing defects
- IPC standards for assembly processes
- Common differences between the classes
- IPC documents to set the level of acceptance criteria
Download Now
Copper plating guidelines for medical flex PCBs
As a PCB manufacturer or designer, it is important to know the difference between class 2 and class 3. Most of the time, even if the end product only requires class 1, class 2 PCBs are produced to ensure better performance. Void standards are among the biggest differences between classes. In the further sections, we will have a look at the standards for copper plating voids and surface finish coating voids.
Plating copper through-holes or vias are necessary for multi-layer or double-sided PCBs. Class 3 PCBs cannot have any evidence of voids in copper plating holes. For class 2, a single void in any hole is acceptable as long as no more than 5 percent of holes have voids. No void is more than 5 percent of the hole length, and the void is less than 90 degrees of the circumference. Also read, what is conformal coating?
Class 3 flex PCBs copper plating standards
- No voids are allowed in copper plating holes of class 3 PCB.
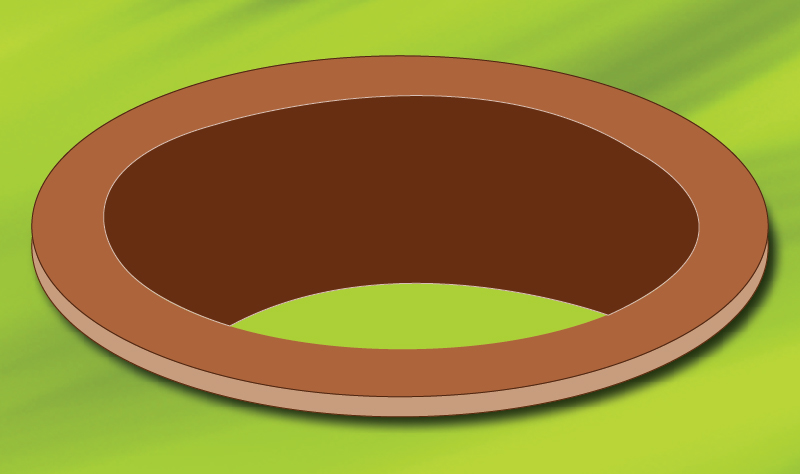
Class 2 flex PCBs copper plating standards
- No more than one void in any hole
- Not more than 5% of the holes should have voids
- Any void should not exceed 5% of the hole length
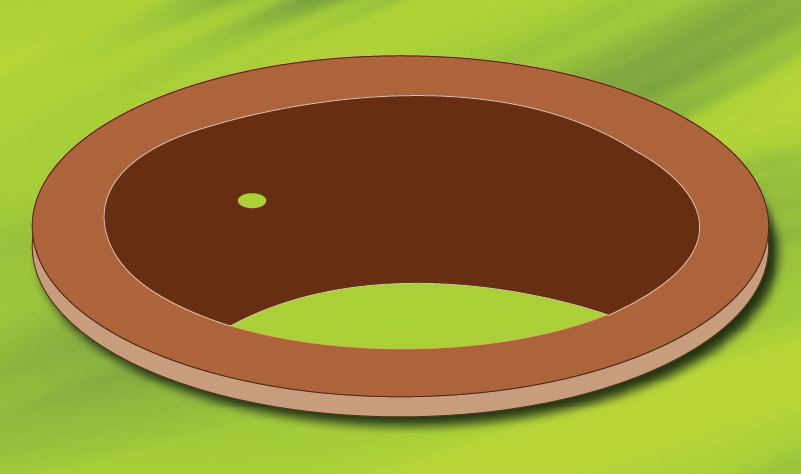
To know more about flex PCB design, read our article 5 Must-Knows for Your First Flex PCB Design.
Flex PCB surface finish guidelines
There are similar stipulations when it comes to the surface finish coating.
- Class 3 boards cannot have more than one void per hole, no more than 5 percent of holes can have voids, and the void cannot be more than 5 percent of the hole length.
- For class 2, three voids per hole are acceptable, but all other requirements remain the same.
- Class 1 boards are acceptable if they have five voids or fewer in any hole, 15 percent or fewer of the holes have voids, and no void is more than 10 percent of the hole length. For all three classes, the voids cannot be more than 90 degrees of the circumference.
For more detailed discussion on IPC standards, read our blog IPC-2223 standards and design violations for rigid-flex boards
These relatively small distinctions determine not just the classification of circuit boards, but also their reliability and capabilities. It should also be noted that flex PCBs that are used in medical devices should be manufactured as per the IPC class 3 standards. To ensure that a given circuit design meets the right qualification, it’s imperative that designers choose the right manufacturing class with the help of a reputable manufacturer that can deliver reliable products. In this article, we have studied the manufacturing class of medical PCBs. Let us know in the comment section if there are any specific topics that you would like to read more about.
To learn more about flex design guidelines, watch our webinar Flex PCB Design Guidelines for Manufacturing.
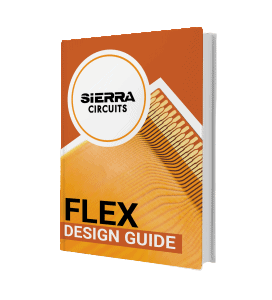
Flex PCB Design Guide
10 Chapters - 39 Pages - 45 Minute ReadWhat's Inside:
- Calculating the bend radius
- Annular ring and via specifications
- Build your flex stack-up
- Controlled impedance for flex
- The fab and drawing requirements