Contents
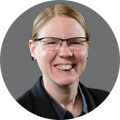
On-demand webinar
How Good is My Shield? An Introduction to Transfer Impedance and Shielding Effectiveness
by Karen Burnham
The development of flex PCBs for satellite application has gathered significant interest among several space agencies. Numerous benefits of flex technology are the primary reasons that drive industry players towards the adoption of flexible PCBs.It is evident that the design and development of space-based commercial satellite products are given primary importance in comparison with other electronic devices.
How does a satellite operate?
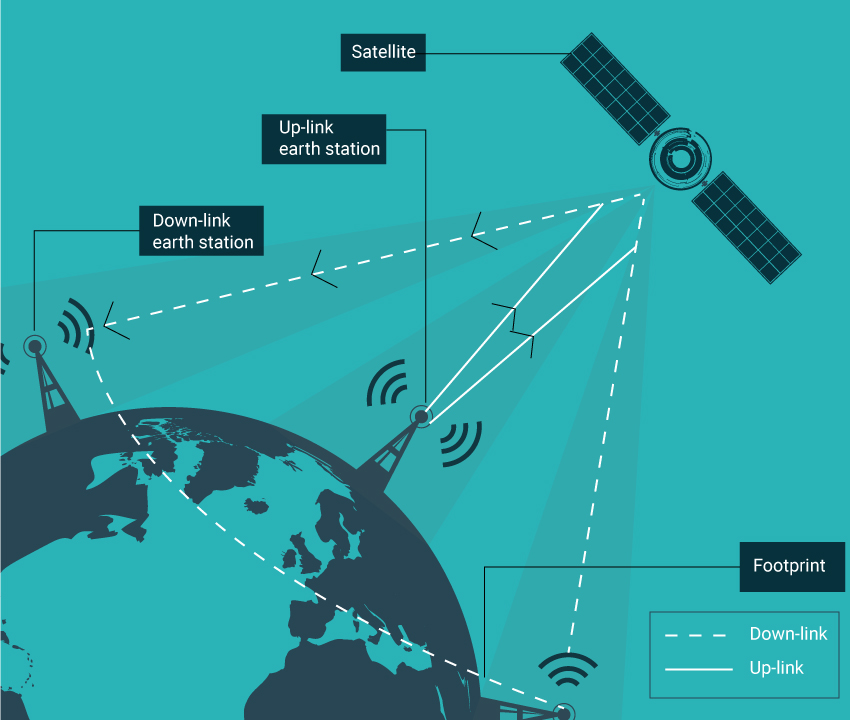
The basic elements of a satellite communication system are shown in the figure above. The operation begins at an earth station where a transceiver is deployed to transmit and receive signals from a satellite in the earth’s orbit. The transceivers on the earth transmit information in the form of high-frequency signals to the satellites. The satellites receive these signals and re-transmit them back to the earth where they are received by other earth stations in the coverage area (satellite’s footprint). The area at which the transceivers receive the signals of useful strength from the satellite is called the satellite’s footprint.
Satellite systems consist of three main circuitries, which include satellite, receiver, and transmitter. The communication between a transmitter, present on Earth, and a satellite is referred to as uplink, while the communication between a satellite and a receiver, present on Earth, is termed as the downlink. Satellites are used for disaster risk management, weather forecasting, remote sensing, geo-positioning, and navigation.
Other applications of satellites include television, telecommunication, and emergency response monitoring. Electronic components within these circuitries are set to cover highly specific wavelength ranges. These wavelength ranges are within the electromagnetic spectrum.
Types of satellite services
The satellites are classified into three different types based on the services they provide:
- Fixed Satellite Service (FSS),
- Mobile Satellite Service (MSS), and
- Broadcast Satellite Service (BSS)
Fixed Satellite Service (FSS)
The Fixed Satellite Service (FSS) uses fixed receiving stations, which supplies to the end-user. The common application of Fixed Satellite Service (FSS) includes cable TV and internet relay stations. The fixed services only utilize the terrestrial stations.
Mobile Satellite Service (MSS)
Deals with mobile ground systems and mobile phones. These services are also used for communication among ship vessels and fleet vehicles.
Broadcast Satellite Service (BSS)
This broadcasts TV and radio signals directly to users. For instance, the satellite dishes used for broadcasting TV channels to subscribers.
With this basic knowledge, let’s talk about the PCBs that go into these satellites.
Why are flex PCBs used in satellite applications?
Flex PCBs have several advantages over rigid PCBs when it comes to satellite applications. Features of flex PCBs like reduced weight and increased reliability make flex PCBs the best choice for space applications. Let us have a look at a few features of flex PCBs that are suitable for space applications.
Reliability
When designing PCBs for space applications, the reliability of the PCB becomes very important. There are examples of satellites that have been operational for 30 plus years. Dynamic flexible circuits can withstand greater stress than a rigid PCB. Flex PCBs can substitute the connectors which are more likely to cause interconnection failures. Most of the connections in the flex PCBs are made with the substrates.
Since satellites are subjected to harsh conditions, the flex PCBs are built to withstand them. The flex PCBs are designed in such a way that they can flex thousands of times during their operation. This will enable the flex PCBs to work in unfavorable conditions.
Versatility
Operating an electronic system in space is very challenging. Designers would require versatile electronic components to overcome the hurdles. Flex PCBs are more adaptable than any other type of PCBs, as they enable the designer to implement odd shapes. A flex circuit can be formed in complex shapes in three dimensions with branches to multiple connectors, which would be impossible to achieve with a rigid PCB. At times, it is not feasible to place a large rigid PCB in a small section of a spacecraft. Flexible circuits can conveniently fit into the surfaces they are mounted on.
Compact and lightweight
The flexible circuits have thinner copper layers and insulating layers. Due to this the bend radius of the flex PCBs can be as minimum as required. As a result, these PCBs can adapt to tighter spaces.
To know more about the advantages that the flex PCBs offer read our article The Advantages of Flex PCBs And Their Applications.
Important factors to be considered while designing flex PCB for space application
As we have already discussed, PCBs used in space applications operate in very harsh conditions. It is very important for the designers to consider the below points before they begin their flex PCB design for space application.
Operating temperature
Though the PCBs are not directly exposed to the space conditions, they should be designed such that it suits the internal environment of the space applications. Material selection for such PCBs becomes very crucial. The material that has an operating temperature of more than 120 °C should be chosen for space applications. You should also ensure efficient thermal management in your aerospace circuit design to increase reliability.
Limiting outgassing
Application of PCBs in a high-pressure vacuum environment can release gasses trapped in the PCBs during the fabrication process. This leakage of gas can condense on the other sections of the equipment. Heat application on the PCBs during its operation in a high-pressure vacuum can force the gasses out of the PCBs, this is called outgassing. Outgassing can be minimized by choosing a material with good thermal resistance for your PCB design.
Sustain orbital collisions
Satellites are subjected to revolve around the earth in a circular orbit. There is a fair chance of collision between the other celestial bodies while orbiting the earth. The PCBs should be able to tolerate these minor collisions. To make that happen the flexing capability of the flex PCBs should be high. Flexibility/Bendability is an important factor to be considered while designing a flex PCB for space application.
To know more about flex PCB design, read our article 5 Must-Knows for Your First Flex PCB Design.
Flex PCBs standards for space applications
Space agencies are implementing their own standards for developing commercial satellite products. These standards are specifically developed to guide the flex PCB design and development process.
Common standards applicable for space application
AS9100: This standard is created by the International Aerospace Quality Group (IAQG). AS9100 describes the requirements for creating/maintaining reliable products for the aerospace industry. AS9100D is the most recent version of this standard.
Military-grade PCBs and aerospace PCBs should be manufactured as per the following standards: MIL-PRF-50884, MIL-PRF-31032, and MIL-PRF-55110. To know more about military-grade PCBs read our article Military-Grade PCB Design Rules and Considerations.
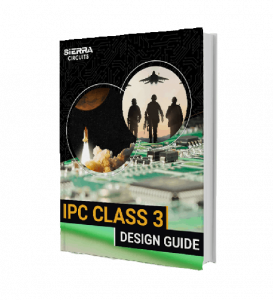
IPC Class 3 Design Guide
8 Chapters - 23 Pages - 35 Minute ReadWhat's Inside:
- IPC guidelines for manufacturing defects
- IPC standards for assembly processes
- Common differences between the classes
- IPC documents to set the level of acceptance criteria
Download Now
PCB materials used in satellite
The development of ceramic, hydrocarbon, thermoset polymer composites by Rogers Co., and Isola, Inc., have allowed manufacturers to develop highly reliable satellite PCBs. Most of these PCB materials have dielectric constants (Dk values) from 3.27 to 12.85 in the z-axis. These materials are expected to exhibit a particular set of characteristics. These materials are well-suited to operate in the challenging conditions of the orbiting satellites.
Flexible PCBs are made up of many materials. One of the widely used materials is Kapton. Kapton is a flex polyimide that has already been used in many space applications. The reason for Kapton material to be chosen is its lightweight. Kapton is also known for its vibration resistance. These unique features of Kapton keep the solar cells and optical sensors safe during application. This material has all of the qualities that it can be used for your flex PCBs in satellite applications.
The viability of flex PCBs for satellite applications is dependent on the capability of the PCB design to operate without fault anywhere up to 10 years. This has led to an intensified race several PCB manufacturers flexing their muscles in developing high-end PCBs. Satellite technology was considered an elite area a few years back. However, the rising footprint of comparatively smaller players in the global landscape will likely increase competition on the ground.
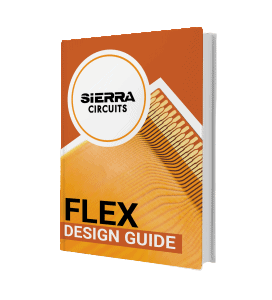
Flex PCB Design Guide
10 Chapters - 39 Pages - 45 Minute ReadWhat's Inside:
- Calculating the bend radius
- Annular ring and via specifications
- Build your flex stack-up
- Controlled impedance for flex
- The fab and drawing requirements
Download Now