Contents
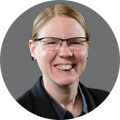
On-demand webinar
How Good is My Shield? An Introduction to Transfer Impedance and Shielding Effectiveness
by Karen Burnham
Surface mount technology is a part of the electronic assembly that deals with the mounting of electronic components to the surface of a PCB. Electronic components mounted this way are called surface-mounted devices (SMD).
SMT was developed to minimize manufacturing costs while making efficient use of board space. The introduction of surface mount technology has enabled manufacturers to fabricate smaller size complex circuit boards. There are various advantages and disadvantages of surface mount technology which we will discuss over the course of this article.
The advent of surface mount technology
Surface-mount technology was developed in the 1960s and was broadly used in the 1980s. By the 1990s, they were used in most of the high-end PCB assemblies. Conventional electronic components were redesigned to include metal tabs or end caps that could be attached directly to the board surface. This replaced typical wire leads which needed to pass through drilled holes. SMT led to much smaller components and enabled component placement on both sides of the board. Surface mounting enables a higher degree of automation minimizing labor costs and expanding production rates that results in the development advanced of boards.
Salient features of SMT and through-hole technology
SMT allows electrical components to be mounted on the board surface without any drilling. Most electronic applications prefer to use surface mount components since they are compact and may be installed on either side of a printed circuit. They are suitable for applications with higher routing densities. These components have smaller leads or no leads at all and are smaller than through-hole components.
The process involved in SMT assembly is:
- Apply solder paste to the fabricated circuit board using stencils. Solder paste is made up of flux and tin particles.
- Attach the surface mount components.
- Use a reflow method for soldering.
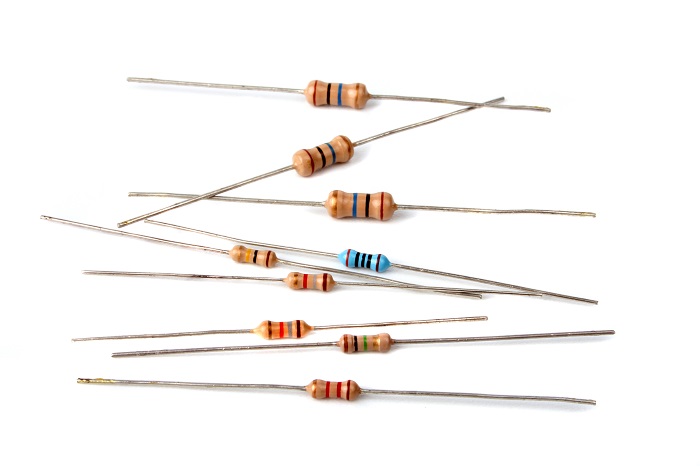
In through-hole technology, the component leads are inserted into the drilled holes on the board. These leads are then soldered to pads on the opposite side using wave soldering or re-flow soldering tools. Since through-hole mounting offers strong mechanical bonds, it is highly reliable. However, drilling PCBs during production tends to increase manufacturing costs. Also, through-hole technology limits the routing area for signal traces below the top layer of multi-layer PCBs.
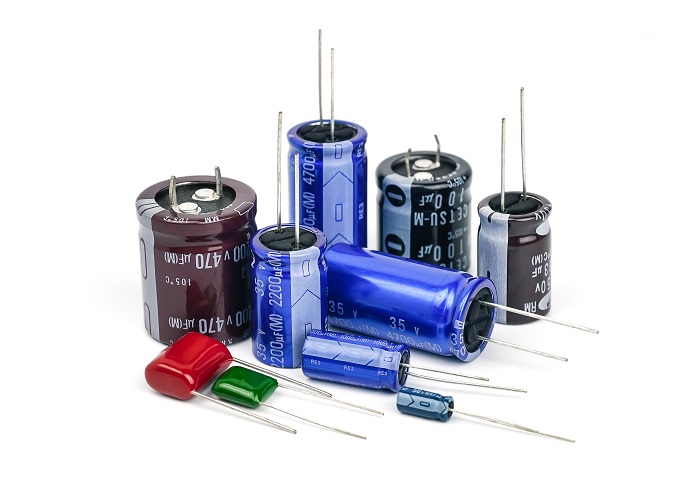
Major differences between through-hole technology and surface mount technology
- SMT frees up the limitation on board space posed by the through-hole mounting manufacturing process.
- Through-hole components involve higher manufacturing costs than SMT components.
- You require advanced design and production skills for using SMT when compared to through-hole technology.
- SMT components can have a higher pin count as compared to through-hole components.
- Unlike through-hole technology, SMT enables assembly automation which is suitable for high production volumes at lower costs when compared to through-hole production.
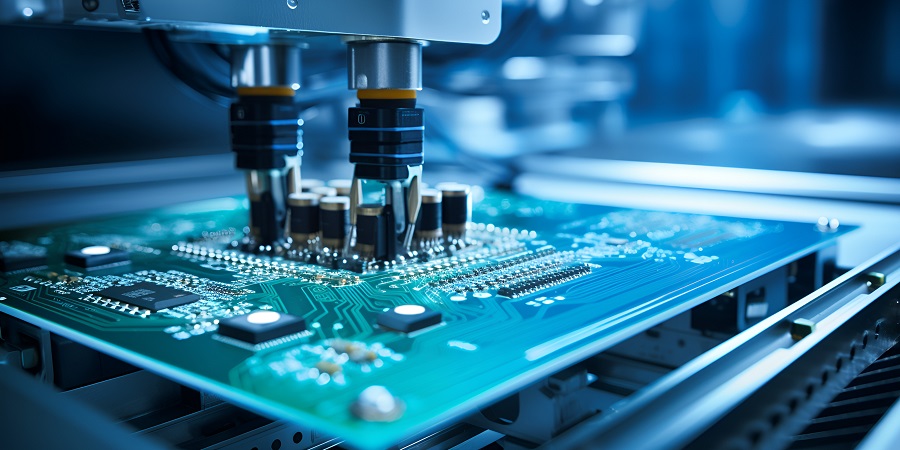
- SMT components are more compact leading to higher component density as compared to through-hole mounting.
- While surface mount leads to lower production costs, capital investment for machinery is higher than needed for through-hole technology.
- Through-hole mounting is better suited to the production of large and bulky components that are subjected to periodic mechanical stresses or even high-voltage and high-power parts.
- SMT makes it easier to achieve higher circuit speeds because of its reduced size and fewer holes.
Factors to consider before choosing SMT or through-hole technology
- Stability of the component when exposed to external stress
- Ease of thermal management/ heat dissipation
- Availability of the part and its alternative
- Cost-effectiveness of assembly
- High performance and life-span of the package
- Facilitate rework in case of board failure
Advantages of surface mount technology
SMT has many advantages over conventional through-hole technology:
- Surface mount technology supports microelectronics by allowing more components to be placed closer together on the board. This leads to designs that are more lightweight and compact.
- The process for SMT production setup is faster when compared to through-hole technology. This is because components are mounted using solder paste instead of drilled holes. It saves time and labor-intensive work.
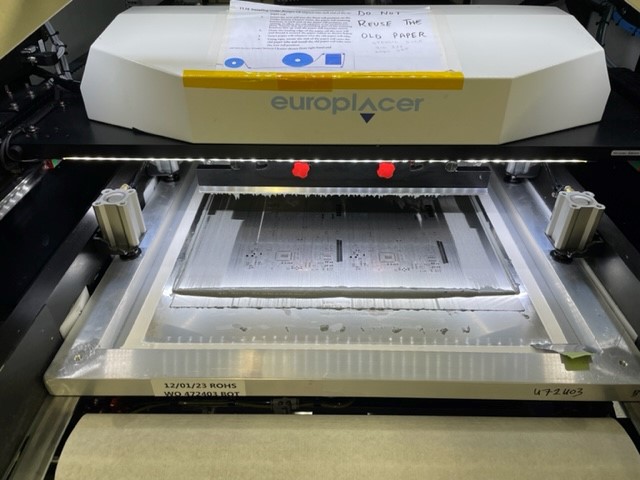
- Components can be placed on both sides of the circuit board along with a higher component density with more connections possible per component.
- Due to the compact size of the package, higher-density traces can be accommodated on the same layer.
- The surface tension of molten solder pulls components into alignment with solder pads, which automatically corrects minor placement problems.
- Compared to through holes, these do not expand in size during the operation. Hence you can reduce the inter-packaging space.
- Electromagnetic compatibility is easily achievable in SMT boards because of their compact package and lower lead inductance.
- SMT enables lower resistance and inductance at the connection. It mitigates the undesired effects of RF signals and provides better high-frequency performance.
- More parts can fit on the board easily due to their compactness, resulting in shorter signal paths. This enhances signal integrity.
- The heat dissipated is also lesser than through-hole components.
- SMT reduces board and material handling costs.
- Enables you to have a controlled manufacturing process. This especially opted for high-volume PCB production.
Ensure the manufacturability of your circuit design using the Better DFM tool.
Disadvantages of surface mount technology
Even though SMT has several advantages, the technology also comes with it certain disadvantages:
- When you subject components to mechanical stress, it is not reliable to use surface mounting as the sole method of attachment to the PCB. This is because you need to use component connectors to interface with external devices that are periodically removed and re-attached.
- Solder connections for SMDs might be damaged through thermal cycles during operations.
- You would need highly skilled or expert-level operators and expensive tools for component-level repair and manual prototype assembly. This is because of the smaller sizes and lead spaces.
- Most SMT component packages can’t be installed in sockets that enable easy installation and replacement of failed components.
- You use less solder for solder joints in SMT, therefore the reliability of solder joints becomes a concern. Void formation might lead to solder joint failures here.
- SMDs are typically smaller than through-hole components leaving lesser surface area for marking part IDs and component values. This makes identifying components a challenge during prototyping and repairing the PCB.
- The solder can melt when exposed to intense heat. Therefore, SMT cannot be implemented in electrical load circuits with high heat dissipation.
- PCBs that use this technology requires more installation costs. This is because most of the SMT equipment such as the hot air rework station, pick and place machine, solder paste screen printer, and reflow oven are expensive.
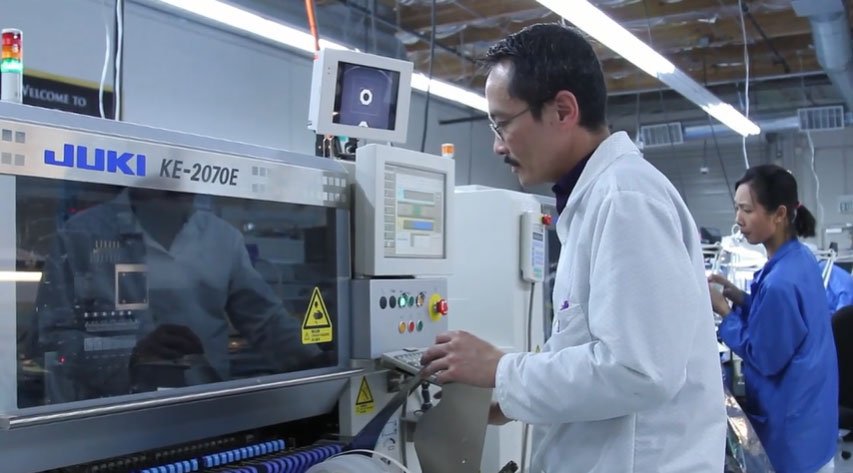
- Miniaturization and a variety of solder joints can make the procedure and inspection more difficult.
- Due to compact size, there is an increased chance of solder overflow that can result in short circuits and solder bridge.
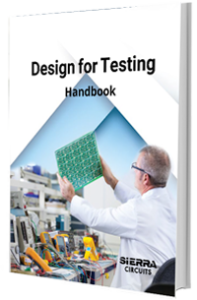
Design for Testing Handbook
7 Chapters - 28 Pages - 45 Minute ReadWhat's Inside:
- PCB testing strategies
- Guidelines to design and place a test point for FPT
- Directives to make your board ICT compatible
- Benefits and drawbacks of various testing methods
- Defects that you can identify through board testing
Download Now
When to use surface mount technology?
The majority of products manufactured at this time utilize surface mount technology. But SMT is not suitable in all cases. Consider SMT considered if:
- You need to accommodate a high density of components.
- The need is for a compact or small product.
- Your final product needs to be sleek and light despite component density.
- The requirement specifies the high-speed/frequency functioning of the device.
- You need to produce large quantities with automated technology.
- Your product should produce very little noise (if any at all).
Guidelines for SMT component placement
Here are some recommendations for SMD placement to maintain good signal and power integrity for your board.
- Keep the components as near as possible to minimize the routing distance.
- Adhere to the signal path as per the schematic while placing the components.
- Never place the components in the return path of sensitive signals. This leads to signal integrity issues.
- For high-speed devices, place the bypass capacitors closer to their power pins. This will reduce parasitic inductance.
- Arrange the SMD together for power supply circuits. This will help you to provide shorter routing and reduce the inductance in the connections.
- Try to keep SMT components on one side of the board to reduce costs associated with stencils and assembly.
- Maintain the minimal spacing between the test points and SMT components as specified by your manufacturer. This spacing may vary depending on the component’s height.
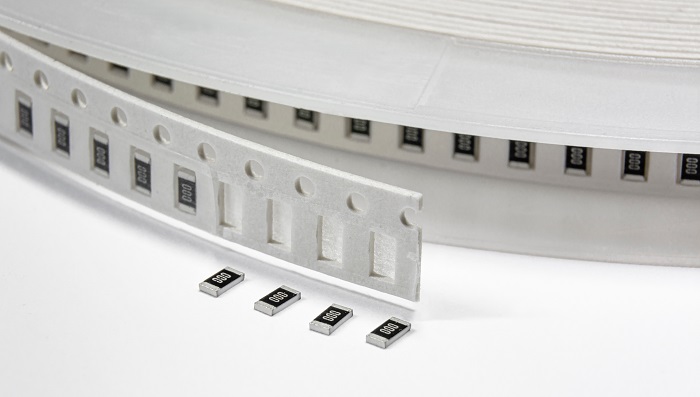
To facilitate the assembly process ensure that all component names, polarities, orientations, and placements are marked properly in the assembly drawing. The footprints present in the drawings should match with the actual parts. Consult your manufacturer for their kitting guideline if you are considering consigned assembly. Prepare your BOM accordingly.
Soldering techniques employed in SMT
Solder reflow and wave soldering are widely used to mount components onto the board. Depending on the nature of the components, the designer can choose one of these methods for surface mounting technology.
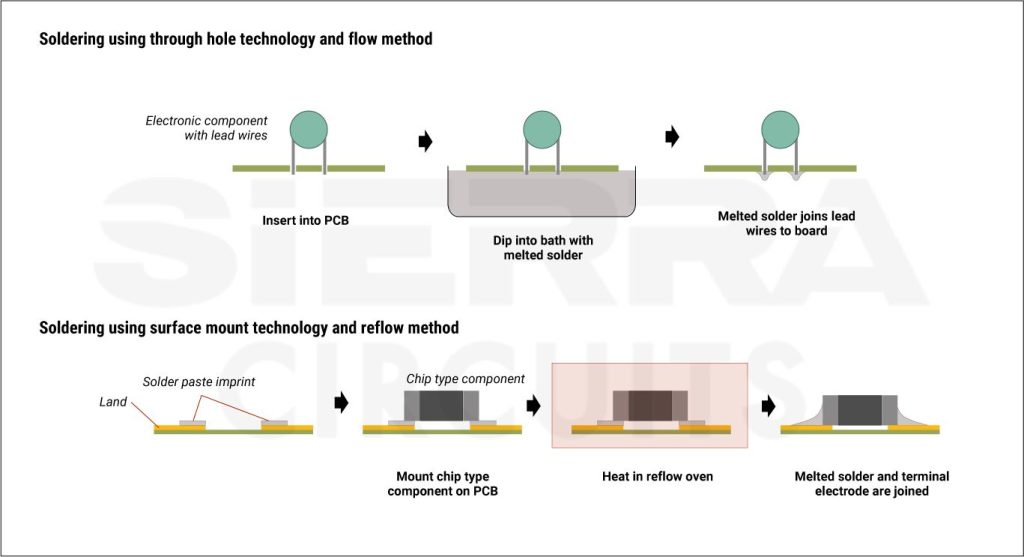
Wave soldering: Since the solder will flow through the holes to form a connection, wave soldering is mostly used for through-hole components. You can use wave soldering for most of the surface-mount components also.
Solder reflow: This process is generally preferred in SMT. Here, the solder on one pin melts and reflows faster than the other. The only disadvantage is that it causes a tombstoning effect, where the component peels away from the non-melted pad. This effect is common for surface mount components like resistors, capacitors, and inductors.
Surface mount device packages
SMD packages come in a broad range of shapes and sizes as given below:
Common passive discrete components: These components are mostly resistors and capacitors and are a part of most electronic devices available today. Given below are SMD package details for capacitors and resistors.
Transistors: The common type of packages for transistors are as follows:
- SOT-23 (Small Outline Transistor) with dimensions 3 x 1.75 x 1.3mm
- SOT-223 (Small Outline Transistor) with dimensions 6.7 x 3.7 x 1.8Mmm
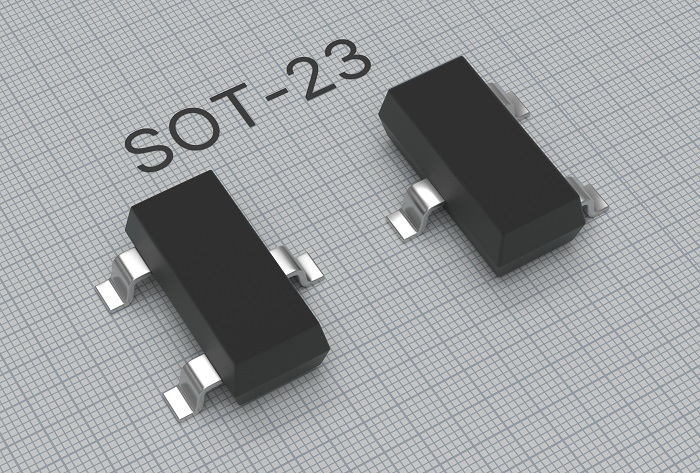
Integrated Circuit (IC) packages
Integrated Circuit packages come in a wide range as given below:
- Small Outline Integrated Circuit (SOIC)
Small Outline Package (SOP)
TSOP (Thin Small Outline Package) is thinner than SOIC
- Quad Flat Pack (QFP)
Quad flat packs are generic square, flat IC packages.
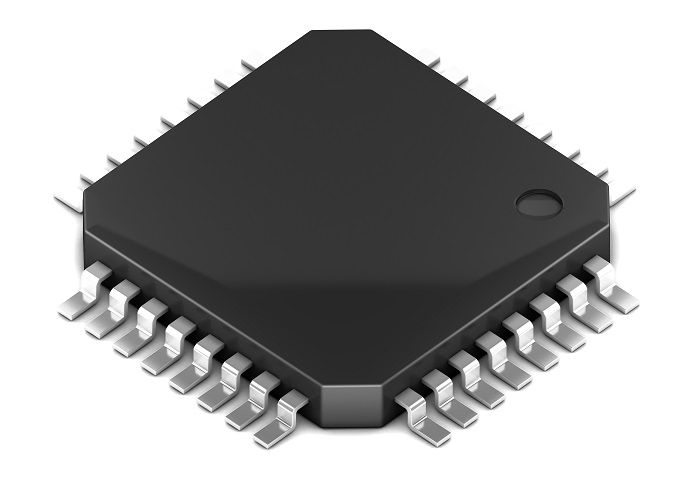
- Ball Grid Array (BGA)
BGA packages include an arrangement of solder balls on the chip underside in the place of pins. The ball spacing typically is 1.27, 0.8, 0.5, 0.4, and 0.35mm

- Plastic Leaded Chip Carrier
The chip is enclosed in a plastic mold. It can either be square or rectangular in shape.
Measurement of SMD size
Surface mount component standards are specified by the Joint Electron Device Engineering Council (JEDEC) Solid State Technology Association (JEDEC.org). JEDEC is an independent semiconductor engineering trade organization and standardization body that has its headquarters in Arlington, Virginia, United States.
You can measure SMD size in inches in the Imperial system and millimeters in the Metric system. For the 0201 imperial components, the dimensions are 0.02 x 0.01 inches. For the 0201 metric components 0.2 x 0.1 mm.
Understanding the advantages and disadvantages of surface mount technology is essential to comprehend its role in the electronics industry. This will always help in optimizing your design and assembly skills. Follow the guidelines listed in this article to completely benefit from the SMT process for component placement. Please comment below if you have any queries on employing surface mount technology for your design. We will be happy to help you.
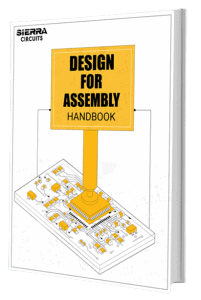
Design for Assembly Handbook
6 Chapters - 50 Pages - 70 Minute ReadWhat's Inside:
- Recommended layout for components
- Common PCB assembly defects
- Factors that impact the cost of the PCB assembly, including:
- Component packages
- Board assembly volumes