Contents
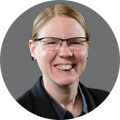
On-demand webinar
How Good is My Shield? An Introduction to Transfer Impedance and Shielding Effectiveness
by Karen Burnham
PCB component management services help you secure high-quality electronic parts against supply chain risks, ensuring your projects progress as per schedule within the budget.
By preventing stockouts, managing lifecycles, and streamlining procurement, component procurement vendors help transform your designs from prototype to production without setbacks.
In this article, we will explain the challenges PCB designers and electrical engineers face in part procurement and how they can benefit from electronic part management services. This will help you source reliable components and accelerate your product’s time to market.
Highlights:
Electronic component supply chain management services help you:
- Avoid delays and quality issues by ensuring high-quality, vetted parts through supplier evaluations and accurate BOM handling.
- Maintain optimal inventory levels with real-time tracking and precise forecasting, preventing costly shortages or excess stock.
- Stay ahead of obsolescence by identifying component end-of-life risks early on.
- Secure reliable alternatives in time.
- Cut costs through strategic procurement and supplier negotiations, reducing unexpected expenses and material wastage.
13 challenges PCB designers and electrical engineers face in component procurement
The table below highlights common issues you may face while sourcing electronic parts and how a component stocking vendor can help you tackle them:
Challenges | Description | Solutions by PCB component management services |
---|---|---|
1. Component stockouts and long lead times | The selected parts may go out of stock or have long lead times, resulting in last-minute redesigns and delays in production schedules. | Provides real-time availability data and diverse sourcing options to minimize delays and redesigns. |
2. Part obsolescence | It typically occurs 4 to 7 years after the introduction of the part. | Monitors product change notifications (PCN) from manufacturers. Tracks component lifecycles and recommends replacements before obsolescence. |
3. Mismatch between component and product lifecycle | Components with short lifecycles may not align with the intended product lifespan, creating long-term maintenance and replacement challenges. | Checks for components’ end-of-lifecycle (EOL) and sources parts aligned with your product’s durability. |
4. Time-consuming footprint creation and library footprint errors | Creating custom component footprints takes significant time, and incorrect library land patterns can cause assembly issues like misaligned pads or wrong pinouts. | Offers verified, ready-to-use footprints, reducing design time and avoiding assembly issues. |
5. Lack of real-time supplier data | Without real-time visibility into inventory and supplier data, communication gaps can arise between design and procurement teams. | Provides real-time supplier and inventory data to align design and procurement, minimizing sourcing gaps and delays. |
6. Counterfeit or substandard parts | Procuring parts from unverified suppliers increases the risk of receiving low-quality or counterfeit electronic components. | Procures exclusively from authorized distributors, ensuring authenticity and quality. |
7. Bill of material inaccuracies | Incorrect part numbers or specifications in the BOM can lead to production delays or faulty PCBAs. | Implements rigorous BOM validation to ensure accuracy and consistency before procurement. |
8. Geopolitical disruptions | Political instability or global events can interrupt established supply routes and impact part availability from certain regions. | Employs geographically diverse sourcing to safeguard supply against regional instability. |
9. Minimum order quantity (MOQ) and pricing constraints | Supplier MOQ or bulk pricing structures may not align with actual project requirements, resulting in overstock. | Negotiates with suppliers to achieve flexible MOQs and pricing that meet your project needs and reduce costs. |
10. Complex supplier coordination | Managing multiple suppliers for one project complicates quality control, delivery schedules, and communication workflows. | Centralizes sourcing through trusted vendor networks to streamline quality control and communication across the electronic manufacturing supply chain. |
11. Logistics and customs delays | International sourcing introduces risks like shipping delays and customs clearance issues, which can stall production timelines. | Manages end-to-end logistics and customs clearance to avoid shipping delays. |
12. Regulatory compliance restrictions | Components must comply with environmental regulations (e.g., RoHS, REACH), and unclear documentation can delay projects. | Ensures all sourced components comply with environmental and industry regulations. |
13. Supply chain price volatility | Fluctuating prices can disrupt budgets and force costly redesigns with alternative parts. | Continuously monitors pricing trends and proactively recommends stable, cost-effective alternatives. |
Download our eBook to learn how to avoid assembly delays due to design issues.
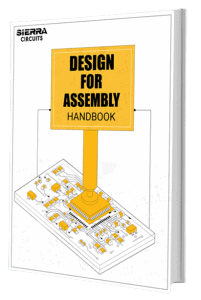
Design for Assembly Handbook
6 Chapters - 50 Pages - 70 Minute ReadWhat's Inside:
- Recommended layout for components
- Common PCB assembly defects
- Factors that impact the cost of the PCB assembly, including:
- Component packages
- Board assembly volumes
Download Now
What is PCB component management service? How does it work?
Component procurement and stocking services take care of your electronic component requirements for your circuit board assembly. It helps you source high-quality parts from trusted suppliers on time, ensuring a robust electronics supply chain management.
The block diagram below shows the workflow of the part management services:
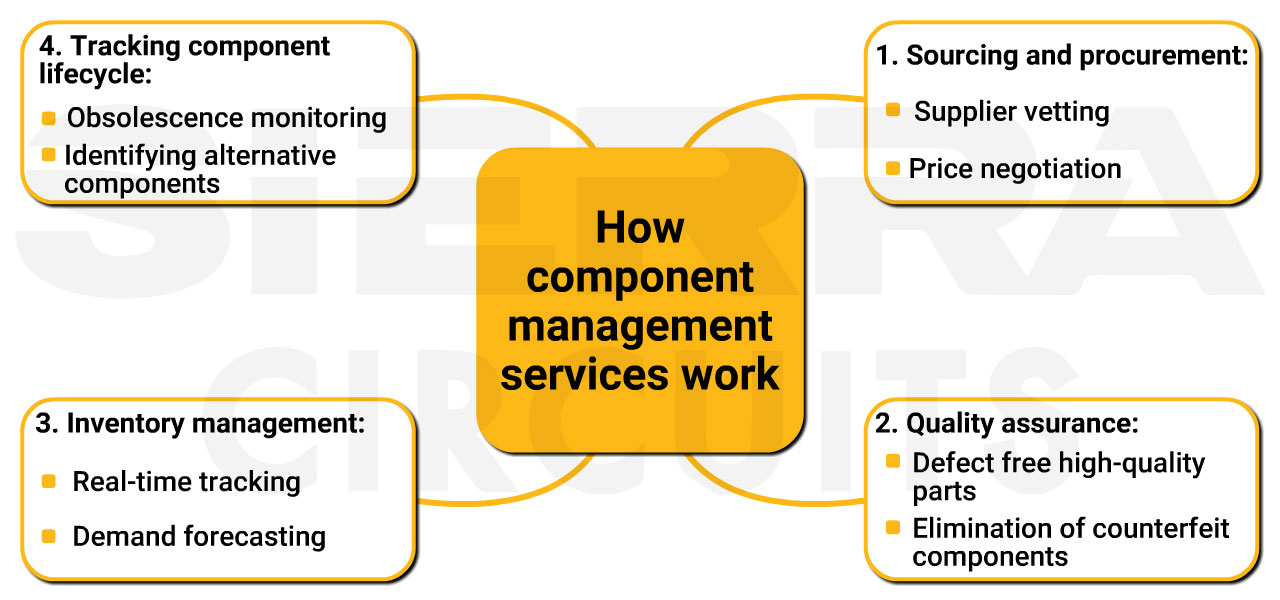
Strategic sourcing and procurement
Component procurement vendors begin by carefully selecting trusted suppliers through rigorous vetting processes, securing competitive pricing, and coordinating timely deliveries. The PCB bill of materials plays a key role by outlining all necessary parts, their specifications, and approved vendors to ensure accuracy and alignment during procurement.
Quality assurance
All incoming components are inspected for authenticity, damage, and compliance to catch counterfeits or defects before they hit your production line.
Inventory management
The component stocking vendors track component usage in real-time and forecast demand to avoid shortages or overstocking. This balance helps you reduce holding costs and avoids delays due to unavailable parts.
Tracking component lifecycle
The EOL status of components is continuously monitored to identify potential obsolescence early. When risks are detected, suitable alternatives are recommended to help you avoid redesigns, production delays, and disruptions in the electronic components supply chain.
Why choose PCB component management services?
Sourcing, managing, and tracking electronic parts can be complex. However, component management solutions simplify the process and enhance assembly efficiency. As a PCB designer, you’ll see these benefits:
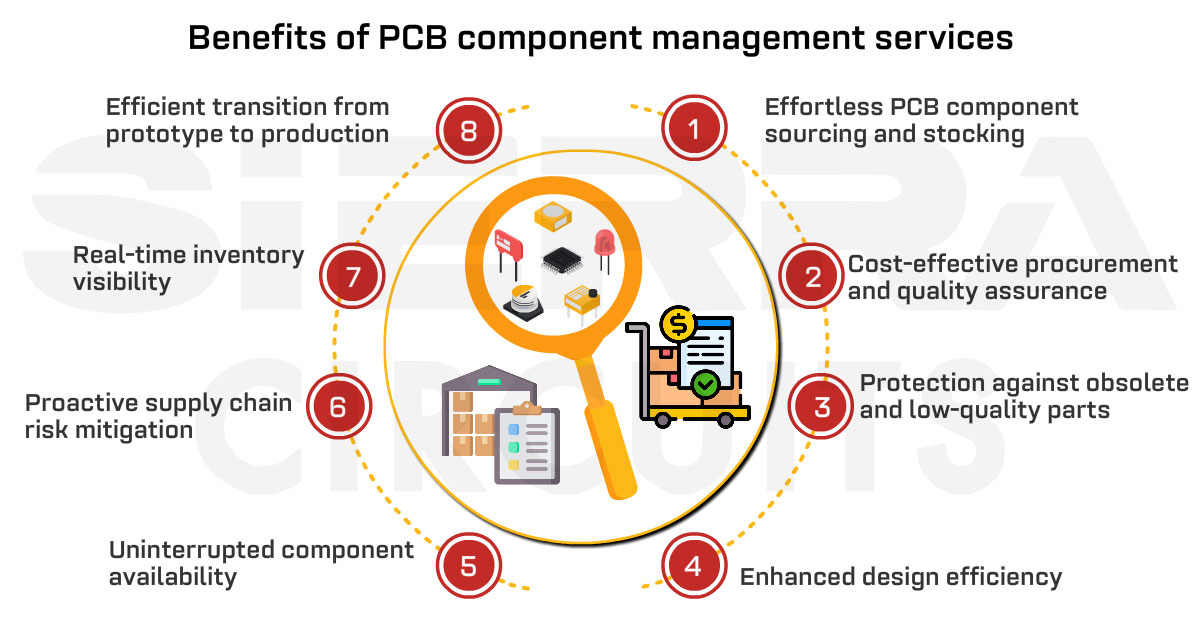
- Effortless PCB component sourcing and stocking: Part procurement vendors handle sourcing and stocking parts, simplifying your electronic supply chain management and freeing up your resources. It lets you focus more on design and innovation.
- Cost-effective procurement and quality assurance: With professional procurement teams and stringent quality inspection processes, the service providers secure favorable pricing and ensure that all products meet high-quality standards, preventing defective parts from entering production and lowering overall costs.
- Protection against obsolete and low-quality parts: Component stocking vendors implement rigorous quality checks and proactively manage obsolescence to eliminate the risk of using counterfeit, obsolete, or low-quality parts. With this, you can ensure a clean BOM.
- Enhanced design efficiency: Selecting standardized electronic parts eliminates the need to create custom footprints and reduces the risk of manual errors, leading to faster, more accurate designs.
- Uninterrupted component availability: Ensuring sufficient parts through extensive supplier networks and proactive management significantly reduces the risk of shortages and prevents production delays, leading to faster product launches.
- Proactive supply chain risk mitigation: By monitoring market trends and supply conditions, service providers proactively alert you to potential obsolescence or disruptions and offer alternatives for design continuity.
- Real-time inventory visibility: Access to updated inventory data helps you monitor part usage and availability, allowing you to avoid part overstock and shortages.
- Efficient transition from prototype to production: With sourcing, inventory, and lifecycle management handled by the component stocking vendor, you can move confidently from prototype to full-scale production without delays or last-minute part changes.
To help you eliminate potential supply chain disruptions, Sierra Circuits offers customer-owned inventory (COIN) services. By leveraging COIN, you can reduce the risk of counterfeit components, gain better control over inventory and logistics, and free up your time to focus on design aspects.
How Sierra Circuits’ COIN services ensure an uninterrupted supply chain
Customer-owned inventory services provide electronics supply chain solutions by helping you procure, store, and manage high-quality parts.
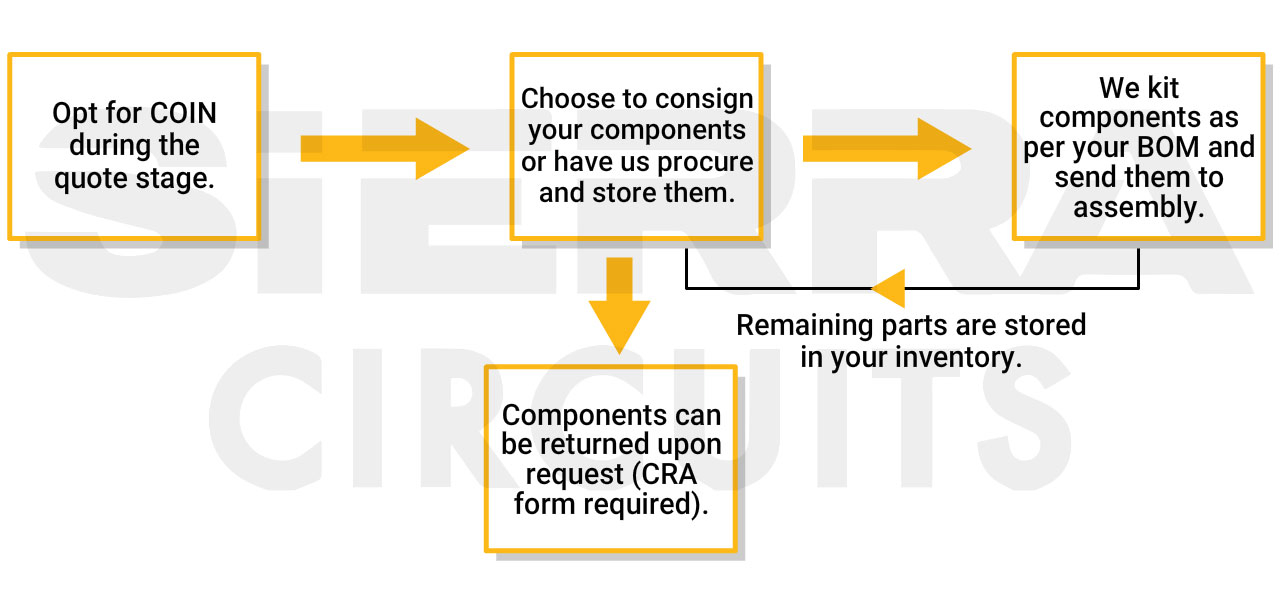
Here, Sierra Circuits handles the entire process from component sourcing, storage, and kitting for PCBA. You can consign items or have Sierra procure them based on your BOM preferences. See our FAQs on CCI for guidance on component consignment.
The stocked parts will be sent to assembly as per your work order needs. See our FAQs on CTB to confirm parts availability.
The remaining components (post-assembly) are restored to your inventory for future use if they meet the kitting guidelines.
If you want the unused parts returned, submit a component return authorization (CRA) form. You can get this form from your account manager. Once we receive your request, we’ll ship the parts back. See our FAQs on CST to learn how to resolve post-shipment issues
To opt for COIN, talk to your account manager during the quote stage.
See our FAQs on COIN services.
Here’s how Sierra Circuits’ COIN supports each part of the electronic components supply chain:
- Procures components only from our approved vendor list (AVL) to minimize the risk of counterfeits.
- Maintains high standards and follows a strict counterfeit control policy to reduce the risk of purchasing substandard parts.
- Manages obsolescence, EOL, and lifespan mismatches by monitoring lifecycles and sourcing compatible alternatives, ensuring long-term product reliability without redesigns.
Electronic component life cycle. - Stores parts in a secure, moisture-free environment with dry cabinets at our San Jose, CA, facility following IPC-J-STD-033D standard.
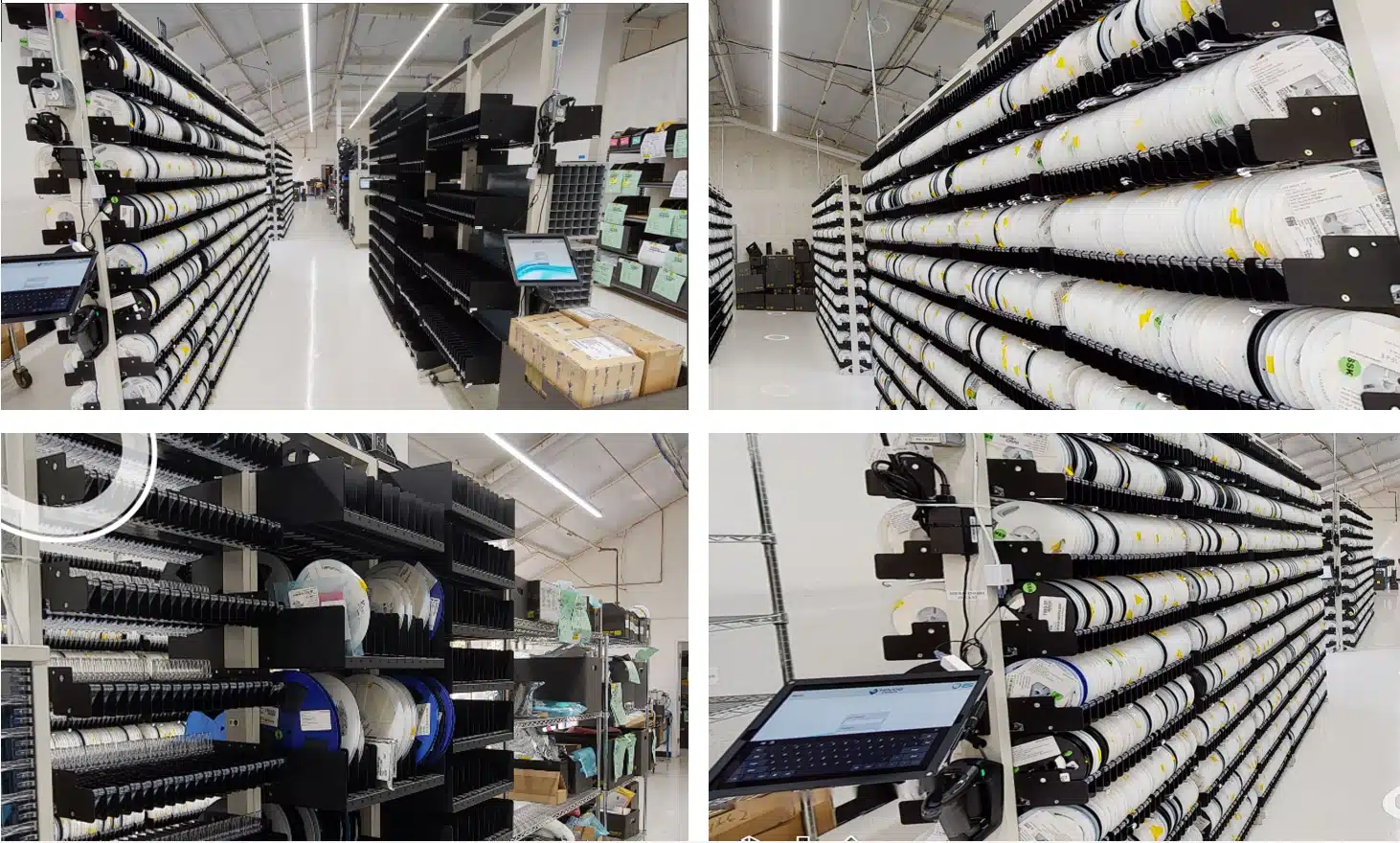
- Follows the IPC-1601A standard for part handling and storage.
- Enforces strict kitting guidelines to ensure assembly-ready products. We require SMDs on continuous tape, ICs in tubes or trays, passives in pick-and-place format, and through-hole/DIP properly packed or in tubes to prevent damage and oxidation. Furthermore, connectors and sockets will remain in their original waffle packaging, guaranteeing reliable PCBAs.
- Provides 24/7 real-time visibility to your inventory. A dedicated support team works closely with you to meet your supply chain and project goals.
- Offers shortage reports that help you identify part shortages before assembly commences. This allows you to restock components or adjust procurement plans, ensuring that production remains uninterrupted. Hence, solving the unavailability issue.
Download our eBook to learn how to design a cost-efficient PCBA.
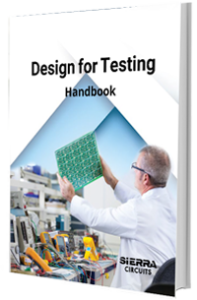
Design for Testing Handbook
7 Chapters - 28 Pages - 45 Minute ReadWhat's Inside:
- PCB testing strategies
- Guidelines to design and place a test point for FPT
- Directives to make your board ICT compatible
- Benefits and drawbacks of various testing methods
- Defects that you can identify through board testing
Download Now
What kind of tests are performed to identify counterfeit components
Engineers perform the following tests to detect counterfeit electronic parts:
Inspection method | Description |
---|---|
Visual inspection | Verifies components’ MPN and validity. |
X-ray inspection | Tests the parts’ internal structure. |
Electrical test | Evaluates the electrical behavior of parts. |
XRF technique | Analyzes part composition. |
Scanning acoustic microscope | Detects anomalies such as voids and delamination inside the components. |
Scrap test | Examines a small portion of the electronic part to ensure the composition is as per your requirement. |
Decapping test | Checks for deviations in die markings. |
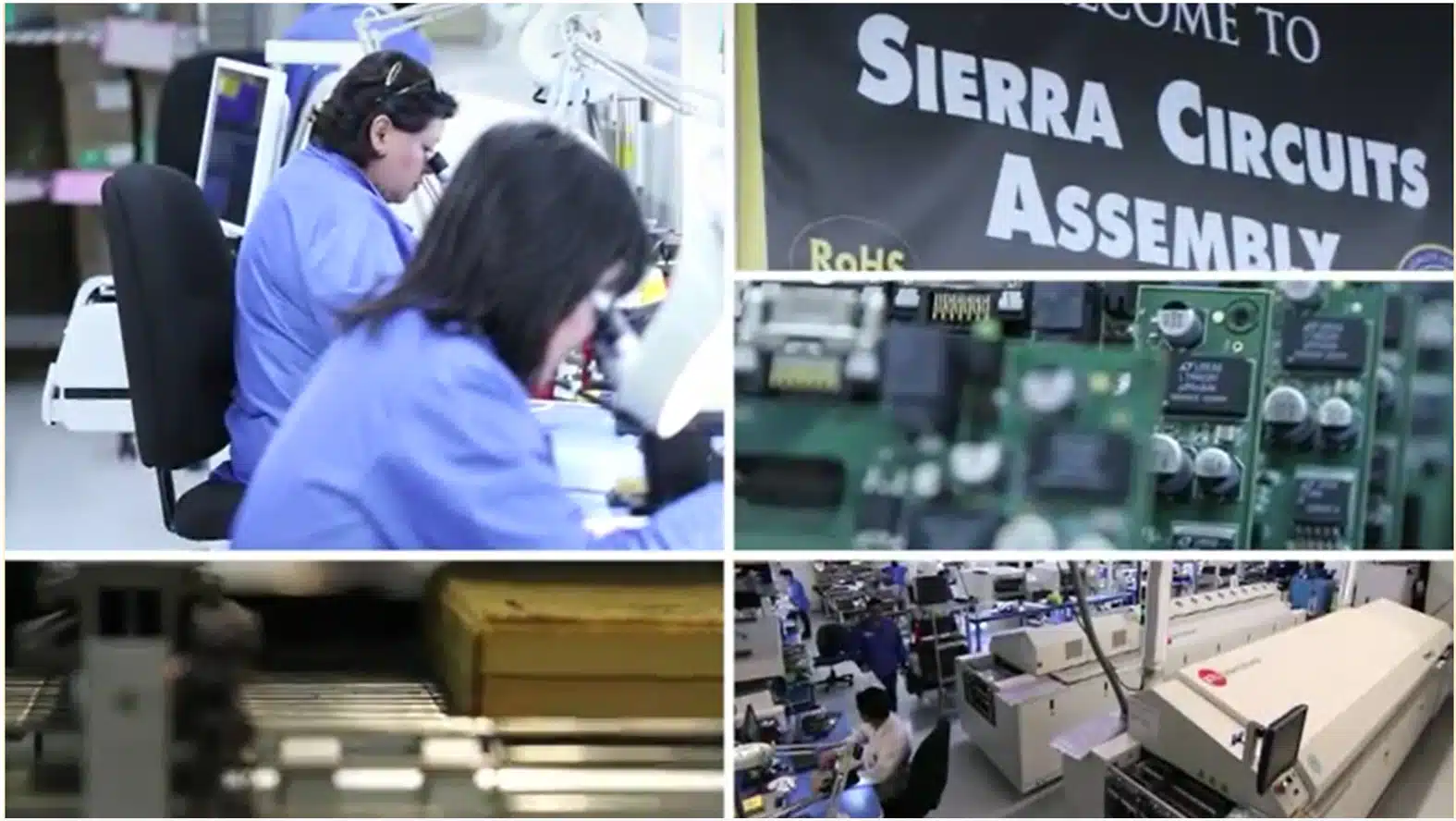
Key takeaways:
- Component sourcing solutions accelerate the transition from prototype to production, helping you meet tight deadlines.
- Electronics supply chain management services improve communication between design, procurement, and production teams, ensuring alignment on part availability and project needs.
- They can handle larger quantities and complex logistics without compromising quality or speed, strengthening supply chain management in the electronics industry.
- Proactive monitoring and real-time updates allow part management services to quickly identify and mitigate potential shortages before they impact production.
By using PCB component management services, you can reduce the time-to-market of your product. It also reduces the risks of using low-quality parts for your circuit board. Have any PCB design or manufacturing queries? Post them on our forum, SierraConnect. Our experts will answer them.
Start the discussion at sierraconnect.protoexpress.com