Contents
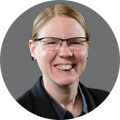
On-demand webinar
How Good is My Shield? An Introduction to Transfer Impedance and Shielding Effectiveness
by Karen Burnham
In the PCB assembly, stiffeners are a typical necessity in numerous flex circuit designs. Flexible circuit boards are one of the popular printed circuit boards now on the market. Flex PCBs will fit into the places where we find it difficult to integrate the rigid boards.
What is a stiffener in flex PCB?
A stiffener isn’t an electrical piece of the PCB, yet assumes the job of offering mechanical support. It is an additional mechanical piece that provides mechanical support to the PCB during the assembly.
Flex PCBs have their downsides as well; they may be too flexible! They may not be rigid in places that need stiffness. This is where human experience came into action. We created PCB stiffeners for these situations.
What are the uses of stiffeners?
We utilize a stiffener when we have to harden a specific area in the flex circuit. First, we need to understand that the PCB stiffener is not an integral part of the electrical circuit board design. This will not let the circuit bend and will protect the integrity of the part’s solder joint. Here are some enlisted reasons to call for stiffeners:
- Mechanically support the specific areas of the board that contain SMT and/or PTH components.
- Keep up the legitimate thickness in the flex circuit.
- Support PCB components and connectors.
- Constrain the flexible parts to rigid areas as per requirement.
- Facilitate better handling of a thin flimsy circuit board.
- Keep certain areas of flexible circuits flat and stable.
- Meet Zero Insertion Force (ZIF) connector specifications.
- Increase the bend radius of the circuit at the intersection of the rigid and flex part. This will avoid the stress on the flex part during multiple bending operations.
- Route and retain arrays. In order to achieve this, the stiffener material will be extended into the array.
Why do flex PCBs need stiffeners?
Stiffeners are required when:
- Components are placed in a flex zone.
- The weight of the components placed in a flex zone stresses the flex material.
- There is a requirement of creating a flat and rigid surface on the flex for the placement of SMT pads components.
- Connectors that require multiple insertions would need a stiffener to help reduce the stress of the pads.
The flex PCB stiffener material
Selecting the right material for the PCB stiffeners is vital as it provides a wide range of benefits in our application. In this section, we will learn about the typically used stiffener materials in the flex circuits. Typically, PCB stiffeners are made up of FR4 or Rigid Polyimide.
FR4 is a woven glass-fiber laminate impregnated with epoxy resin. Polyimide is produced using high-temperature polymer formed into a thin film layer. Numerous layers can be stacked to attain greater thickness. Kapton is one of the classic polyimides used in PCB stiffeners. Kapton is frequently used when the flex ends need to be thickened and inserted into a ZIF connector.
In certain situations, you may need to use other materials such as stainless steel or aluminum, for your PCB stiffener. However, these materials are more expensive.
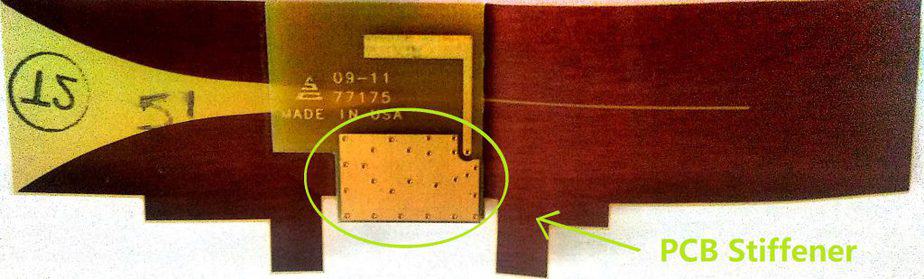
Typical stiffener thicknesses:
The thickness of the stiffener ranges from 0.002″ to 0.059″. The thickness of the Kapton stiffeners range from 0.002” to 0.010” and the thickness of the rigid stiffeners range from 0.008” to 0.059”. The thicker the PCB stiffener is, the more support it will offer. But every design seeks a different thickness. If you want your circuit board to be thicker, you will have to use polyimide stiffeners.
How to use PCB stiffeners?
When we use a stiffener for plated-through hole (PTH) components, the stiffener(s) should be located on the same side of the flex from which the components are inserted. This allows access to solder pads on the flex circuit. You can also attach stiffeners to both sides of a part but then the PCB assembly will require an array configuration review. When we require an assembly array for flex circuit designs, it is common and cost-effective to include the FR4 stiffener throughout the array border. This concludes into a rigid array. This, in most cases, allows the parts to run through automated assembly in the same manner as a rigid circuit board design. It also eliminates the need for any additional tooling plates, etc.
Typically, we will use heat and pressure (thermal bonding) to attach the stiffener to the circuit. We can also attach PCB stiffeners with a pressure-sensitive adhesive.
The two popular types of adhesives generically fall under Pressure-Sensitive Adhesives (PSA) and thermally bonded adhesives. The selection of the adhesive depends on the various performance requirements like thermal exposure, chemical resistance, and adhesion to various materials.
Difference between rigid-flex and rigidized PCBs
- Rigidized flex is a flex PCB, yet it’s bonded with FR4 stiffener to strengthen the rigidity during assembly. Rigid-flex circuits are known as hybrid flex circuits involving rigid and flexible substrates. We laminate them into a single structure.
- There are no traces on a rigid part of rigidized flex, even on pads. This rigid part only strengthens the rigidity of this location. That is to say, it just provides mechanical support to the flex. However, for the rigid-flex PCB, both the rigid and the flex parts are designed with traces and we connect them via holes. That is to say, it’s not mechanical support but an electrical connection for the rigid-flex PCB.
Rigid-flex PCBs have electrical connections whereas rigidized PCBs are for mechanical support.
To know more about rigid-flex PCBs read our article Rigid-Flex Cuts Electronic Product Assembly Costs.
PCB stiffener considerations
- Stiffeners should overlap bared coverlay by .030” to relieve stress. Coverlay acts as a solder resist for the flex PCB.
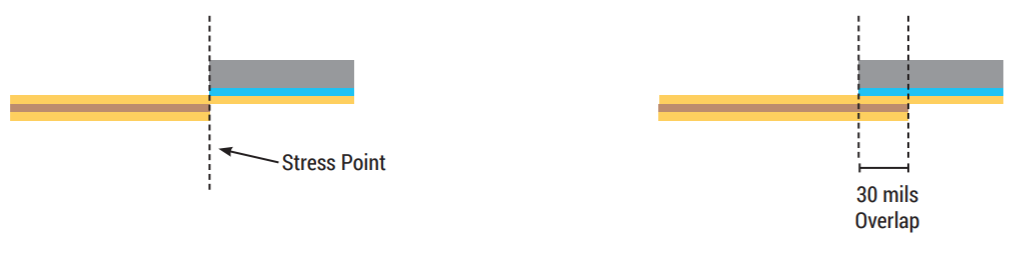
- Maintain the same stiffener thickness when using multiple stiffeners.
To know more about flex design considerations check out Avoiding Common Flexible PCB Errors and Designing for Success
Advantages of using PCB stiffeners
- Stiffeners strengthen solder joints due to which abrasion resistance will be increased.
- Stiffeners can be used for strain relief and heat dissipation.
Flex PCBs come with numerous advantages. To know more about it read our article The Advantages of Flex PCBs And Their Applications
Sample rigid-flex stackup with stiffeners
Let us have a look at a few sample rigid-flex stackup with PCB stiffeners.
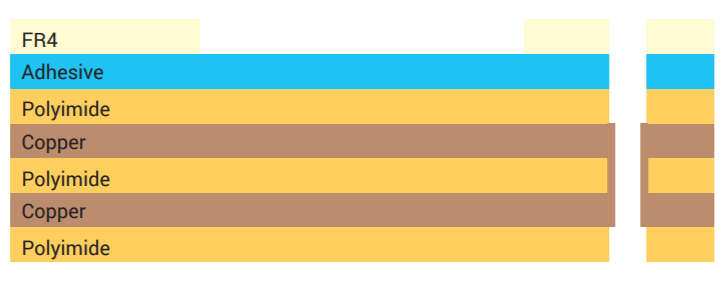
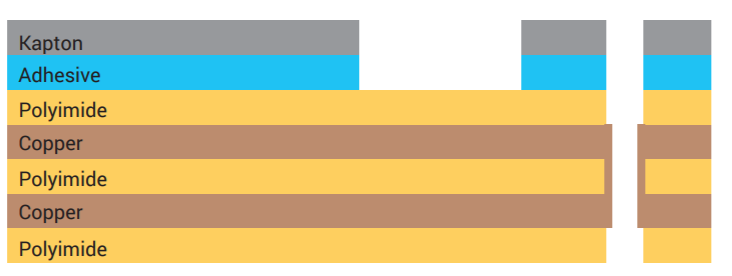
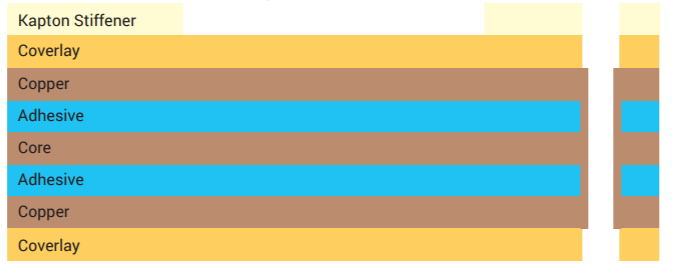
We use a stiffener when we require a rigid area in our flex circuit, to protect components or connectors attached there. This will protect the circuit from bending and the integrity of the solder joints is shielded. FR4 materials are commonly used for stiffeners, this material can be attached with thermally cured acrylic adhesive or pressure-sensitive adhesive. This serves our requirement of rigidizing the specific area in our flex circuit.
To learn more about rigid-flex design, read our blog IPC-2223 standards and design violations for rigid-flex boards
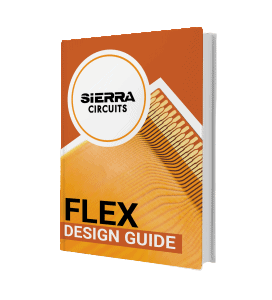
Flex PCB Design Guide
10 Chapters - 39 Pages - 45 Minute ReadWhat's Inside:
- Calculating the bend radius
- Annular ring and via specifications
- Build your flex stack-up
- Controlled impedance for flex
- The fab and drawing requirements
Download Now