Contents
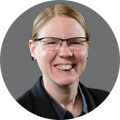
On-demand webinar
How Good is My Shield? An Introduction to Transfer Impedance and Shielding Effectiveness
by Karen Burnham
From signal integrity to roughness of the copper and stack-up design, here are a few PCB design tips you could use:
- Insertion loss and attenuation
- Signal integrity for automotive electronics and IoT
- Fine lines
- Copper for ground and power planes
- Roughness of the copper
- Stack-up design
- Work with your fabricator
Rick Hartley’s 7 PCB Design Tips
1. Insertion loss and attenuation
Insertion loss and attenuation are very important for designers, especially at very high speeds. For lower clock frequencies, if designers can slow down the rising and falling edges, they aren’t as concerned. But people operating in the gigabyte domain certainly have to pay attention, especially to attenuation and losses. I did a class at PCB West on that very subject. There are a lot of good materials available to help calm the effect of losses, such as the I-speed material. I haven’t used that exact material but have used other materials with similar loss characteristics, so I know the advantage they offer.
There is one bit of good news for the design world on that front. The ICs that are being designed and manufactured today often have pre-emphasis and equalization built into the driver and receiver stages. The result is that high-speed materials are less needed today even though speeds are going up. You can buy ICs that handle the losses by altering the shape of the waveform either before it’s sent or at the receive end. That’s a good thing for the design world. It doesn’t mean designers won’t need high-speed materials, simply that the demand is not as severe. When they get into the 10s of gigabytes, they’re going to need both, equalization and/or pre-emphasis, as well as a low loss PCB material.
2. Signal integrity for automotive electronics and IoT
People in the automotive and IoT world typically want to stay with very low layer count boards, if they can. That’s very important because low layer count means low cost. The key is that people need to learn to design 1, 2, and 4-layer boards, yet maintain high-quality signal integrity and control EMI. That is not always an easy task. There are ways to control impedance and contain fields, even in a 1-layer board, but you have to do everything in a co-planer fashion. You must have a return path for every trace just as you would if it were a high-speed board that was high layer count.
The key element, the spacing between the routed trace and the Ground plane or Ground route must be very tight. As our friend Dan Beeker always says, “It’s all about the space”. That’s the way the IoT, automotive and appliance worlds are going to have to start thinking. Also, as they get into reduced IC sizes, they’re going to be thrust into the same exact problem with fine lines that many other industries already face. That’s going to affect everybody and we all need to think about the impact.
3. Fines lines
You don’t necessarily need fine lines in low layer count. As long as density is low, you can go with standard line weights and widths and standard copper weights without any issues at all. However, designers still have to understand what it means to design a PCB transmission line. They have to know that every signal coming out of these devices are fast. IC rise times keep getting faster. It’s not about the clock frequency, it’s about the Rise and Fall time of the energy in the transmission line.
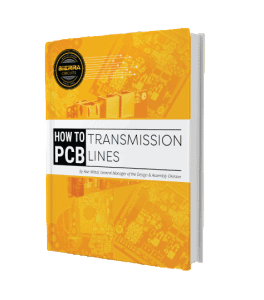
PCB Transmission Line eBook
5 Chapters - 20 Pages - 25 Minute ReadWhat's Inside:
- What is a PCB transmission line
- Signal speed and propagation delay
- Critical length, controlled impedance and rise/fall time
- Analyzing a PCB transmission line
Download Now
4. Copper for ground and power planes
In the average circuit, power delivery has a relatively fixed voltage (ie- 3.3v), so many folks think they are dealing with DC energy, not the case. The current, associated with the magnetic field, is almost always very high in frequency, hence power delivery to ICs driving transmission lines is a high-frequency event.
When you are dealing with really low-frequency current flow, which is VERY rare, designers may need thicker planes. What some people lose sight of, when it comes to power delivery, most of the energy is not at low frequencies, it’s at very high frequencies. The frequency of the energy has to match the switching speed of the IC outputs. The power bus has to provide all of the harmonic frequencies in the square wave, from the clock to .5 divided by rise time, to the output drivers of the IC. This energy is very high frequency. The result is that skin effect takes over during power delivery.
When you have IC output edge rates that are sub-500 picoseconds, you’re now dealing with frequencies of one, two, and three gigahertz. Skin effect is going to be the dominating factor in terms of how much current the copper can handle. One-ounce copper won’t do any better than half ounce copper in that domain. Once you go up beyond a certain frequency you don’t use the entire copper thickness.
Some people are deluding themselves into believing they need one and two-ounce copper in planes. The key is to examine current flow at high frequencies, then do the skin effect calculations and determine how thick the copper really needs to be. What they’re going to find, very often, even quarter ounce copper is good enough for planes in many cases. You don’t need one or two-ounce copper, in planes, most of the time.
5. Roughness of the copper
The roughness of copper does have an impact, unfortunately. People tend to want to look at voltage and current when they analyze issues. Skin effect is about fields. Everything is about the fields, but skin effect is certainly one of those issues. The roughness of copper makes it harder for the fields to establish an even current into the copper of the trace and the plane as the current is induced from the fields. Since the fields establish the current into the copper, the rougher the copper, the harder it is to get even current flow through that copper. Result, the losses become greater with rougher copper.
At high frequencies, skin effect losses almost demand the use of low-profile copper on PC boards. When making low and very low-profile ED copper, the process simply takes longer, hence costs more. Low profile copper is almost a must, if we expect to get the kind of insertion losses in PCB transmission lines.
6. Stack-up design
Since the energy in the circuit is in the fields, if we expect our circuit boards to function as we want them to and to pass EMI testing, we must know where the fields are in the PC board. The stack-up must be designed to contain the fields, so they won’t expand and won’t cause interference problems or EMI issues. Again, to quote Dan Beeker, “It’s all about the space”. The best piece of advice I could give designers is focus on the fields. The fields must be contained. That requires proper Board Stack-up, proper partitioning of circuits. proper routing, layer changes, etc, etc.
Ralph Morrison has recently released a book called ‘Fast Circuit Boards / Energy Management’. This book will tell designers what they really need to know about the management of energy in circuits to help control interference, EMI, and signal integrity issues. Very important publication.
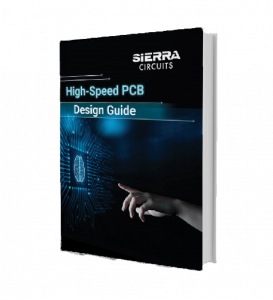
High-Speed PCB Design Guide
8 Chapters - 115 Pages - 150 Minute ReadWhat's Inside:
- Explanations of signal integrity issues
- Understanding transmission lines and controlled impedance
- Selection process of high-speed PCB materials
- High-speed layout guidelines
Download Now
7. Work with your fabricator
One of the things I encourage people to do in my classes is to learn about the boards that their fabricators make. In other words, if you’re going to get a 6, 8, or 10-layer board, find out what is the natural 6-layer, 8-layer or 10-layer board that the fabricator wants to build. What are the dielectrics? What are the copper weights? Find a way to design around that board. Design around those dielectrics. Design around that copper weight. Even if it requires different line widths on different layers to hit some target impedance of 50 or 60 ohms, or whatever.
Design around what the fabricator’s building. Let them know in your fabrication drawing, “This is your 6-layer, this is your 8-layer or this is your 10-layer.” And if you do that, they’re going to get much better throughput. We have done that in the past and high 90 percent throughput from our fabricators even on 12, 14 and 16-layer boards that had very tight impedance control.
For more design information, contact our DESIGN SERVICE team.