Contents
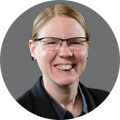
On-demand webinar
How Good is My Shield? An Introduction to Transfer Impedance and Shielding Effectiveness
by Karen Burnham
At first glance, the term thermal control system (TCS) may seem complex. But it simply means maintaining the desired temperature without getting influenced by external environmental conditions.
Advanced electronics are the fundamental element in the aerospace sector. If these electronics experience constant temperature fluctuations, it will result in an early failure which is not acceptable for mil-spec/aerospace applications. Hence, precise aerospace thermal control is mandatory for the efficient functioning of space vehicles.
We got the opportunity to interview Paul Cooke, field application manager at AGC. During this conversation, he explained various concepts of aerospace boards like thermal interfaces, reliability, heat dissipation, etc. Watch the entire interview to learn more about the critical aspects of PCBs in space.
A few applications of circuit boards in aviation include:
- Full authority digital engine control systems (FADEC)
- Advanced medium-range air-to-air missiles (AMRAAM)
- Electronic flight instrumentation systems
- Digitalized signal and microwave processing systems
- Passive detection systems
- Central air data computers (CADC)
- Ground station applications
- Signal sensors
- Radio communications
- LED lighting
- Instrumentation and power switches
Designing thermally regulated aerospace PCBs is crucial for the efficient functioning of electronic subsystems. The functionality of these applications depends upon the condition of their PCB. Thermal management has become crucial more than ever due to increased space access, flight velocity, vehicle survivability, and mission power. Let’s dig deep into the details of aerospace thermal control.
What is an aerospace thermal control system?
Aerospace thermal control system refers to maintaining the temperature level of equipment, payloads (maximum carrying capacity), and launchers during all phases of a space mission. It shields aviation hardware and ensures the optimum execution of the operation. Thermal control sets the desired temperature range during the lifetime of the aircraft. It also assures the efficient performance of delicate electronic components.
The ideal temperature of aircraft/spacecraft depends on the amount of heat input into, stored in, and expelled from the device.
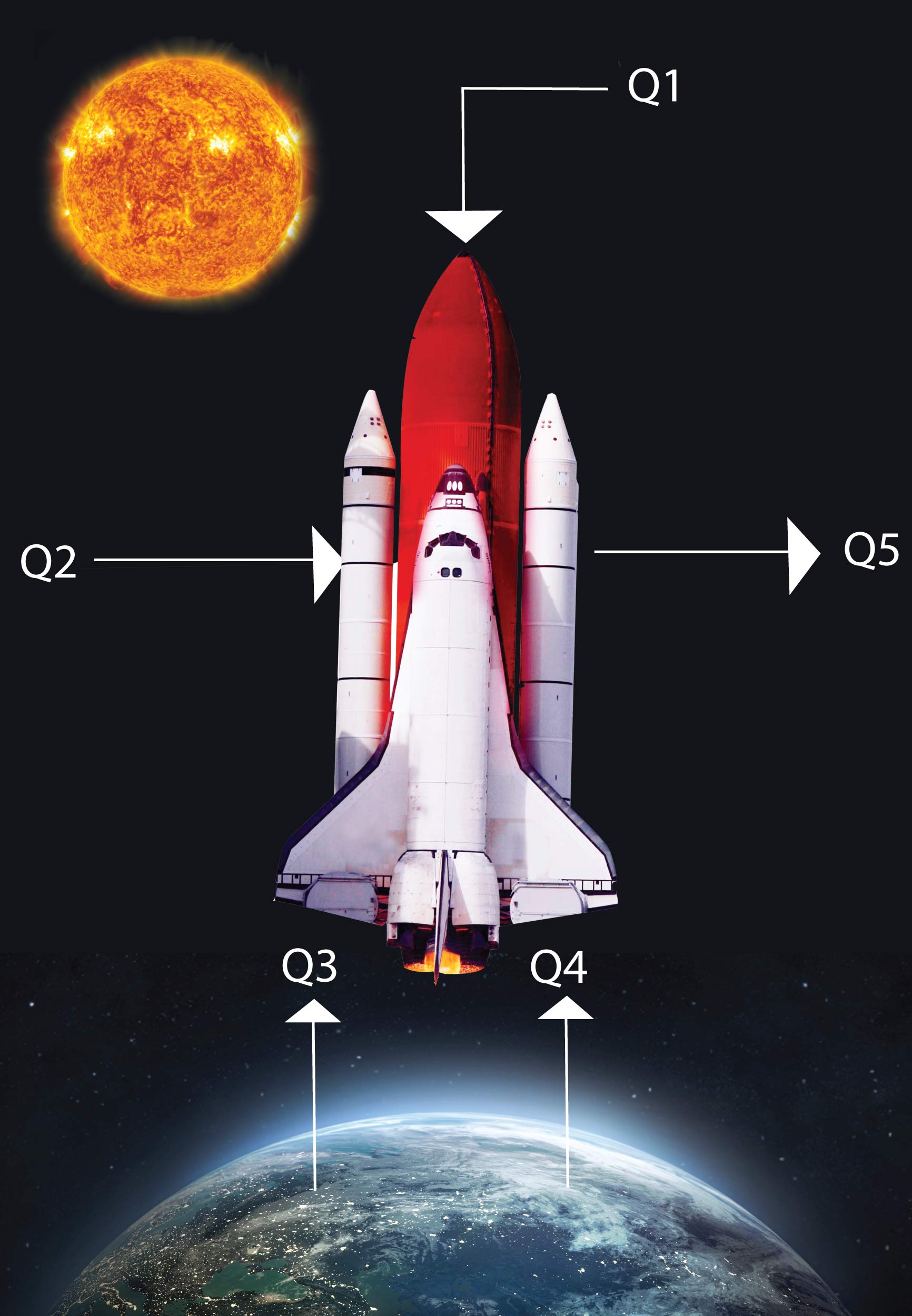
Where,
Q1= Heat developed through spacecraft that is a function of efficiency and power of aerospace components.
Q2= Heat received from the sun. Q2 depends upon the distance from the sun and the absorptivity of the spacecraft’s surface.
Q3= Solar heat reflected from the planet. It relies on the solar absorptivity of the surface and the planet.
Q4= Infrared heat from the planet that is a function of the planet and infrared emissivity of that surface.
Q5= Heat emitted through radiation that consists of infrared emissivity, radiator space, and the temperature difference between spacecraft radiator and heat sink.
Structural and electrical design methods to manage the thermal environment
Effective management of aerospace thermal control systems involves the following methods:
Orientation of space vehicles
- The orientation of space vehicles plays a vital role in managing thermal stability. Sometimes, it needs to change direction to meet the operational requirements. This is determined by the amount of heat dissipation. Even if it is not defined, changing orientation establishes temperature control.
- This technique can also be combined with other elements (such as a radiator) to achieve thermal management.
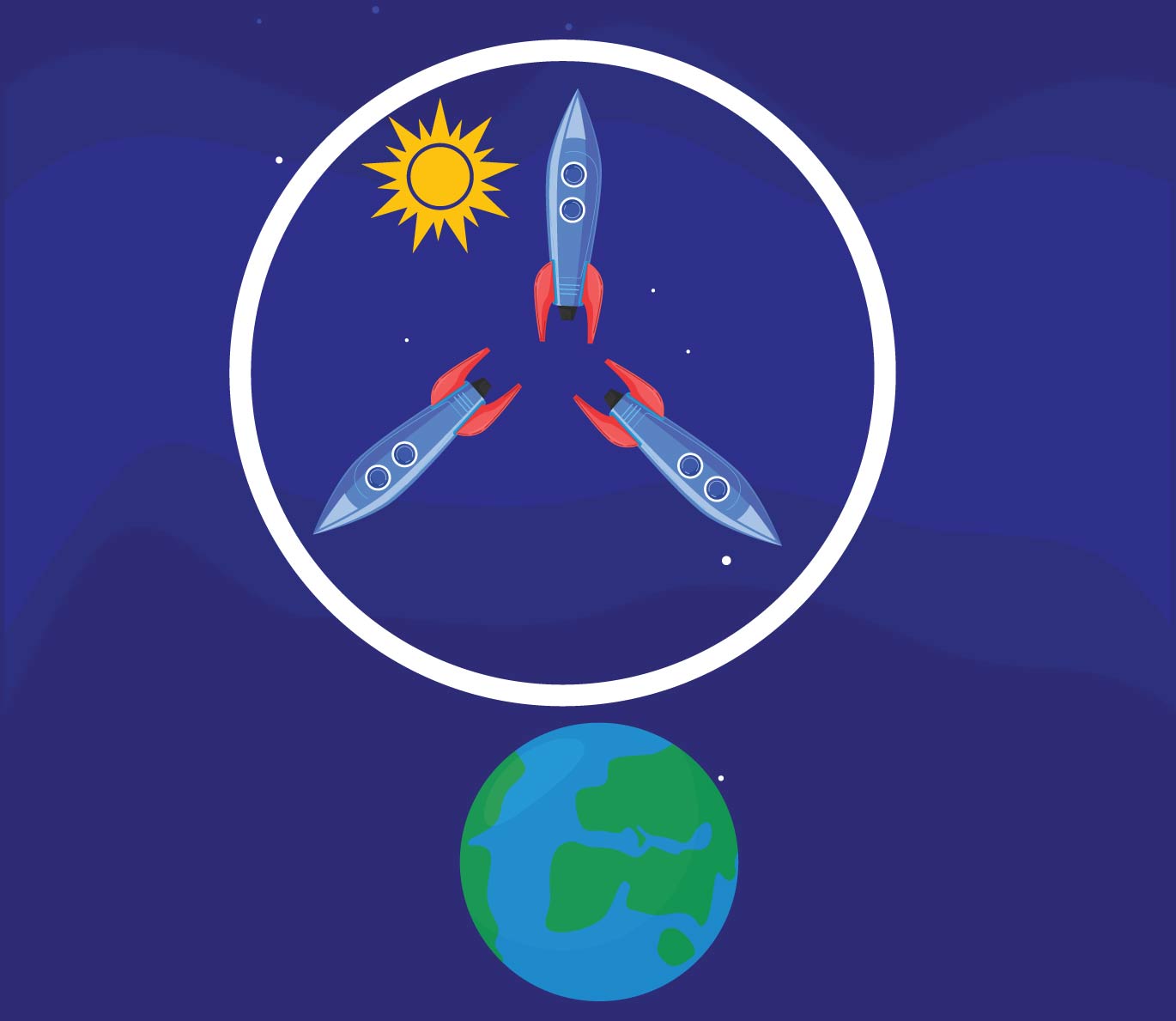
Material selection
Selecting component and circuit board materials according to heat transfer capabilities and heat loss in the dielectric is a good practice. Board materials should also comply with the CTE (coefficient of thermal expansion) conditions suitable for high-reliability applications. It is better to select low-loss PCB material to reduce power loss.
Paul shared his thoughts on this saying, “Polyimide is a brittle material, so it can be very prone to micro cracking, especially if you’re building like planar magnetic-type boards with a lot of heavy copper and the aerospace guys hate that. Ideally, materials for space applications should have low CTE, low loss, and high-speed PTFE type products so they are less likely to develop microcracks.”
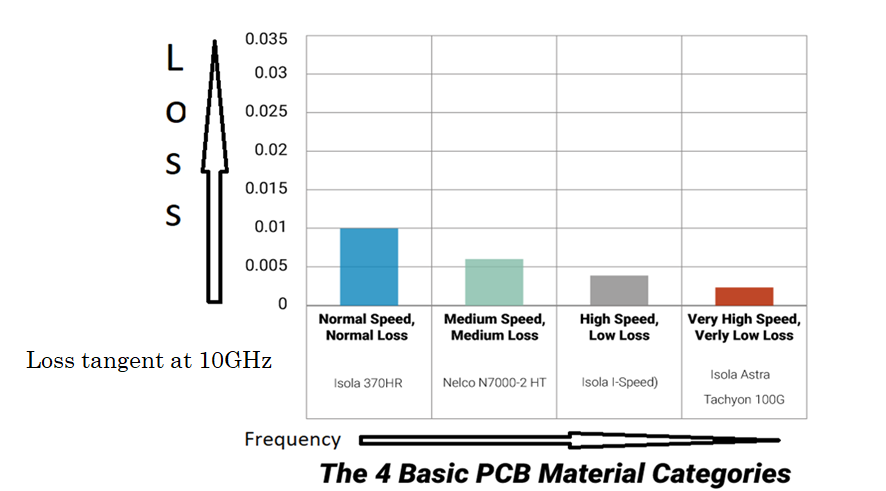
Circuit board design considerations
- Boards can be mounted using wedge locks to increase heat transfer away from them to the structure.
- Another way to channel the heat away from electrical components is to raise the number of copper layers within each board.
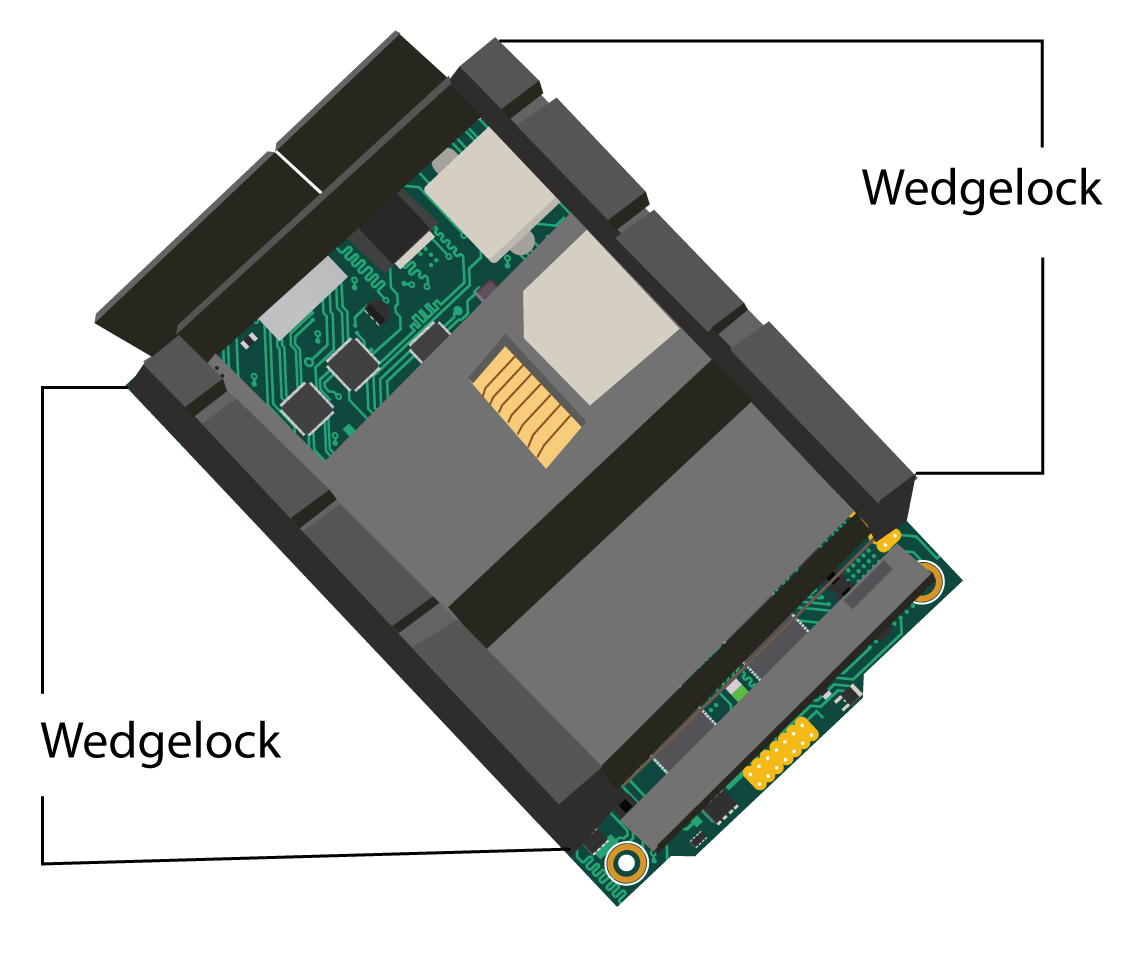
Thermal interfaces
- The mounting method governs the thermal contact between components and facilitates the heat exchange to a structural element when necessary.
- Heat exchange can be increased by:
- Mounting surfaces with thermal interface materials.
- Attaching components with more fasteners whenever possible.
- It is possible to reduce heat transfer by mounting a component through a stack of washers having less thermal conductivity.
Critical aspects of populated boards in aircraft TCS
Circuit boards are a vital component for the precise functioning of aerospace vehicles. Let’s list out some important elements of PCB assembly for TCS.
Conformal coating
Conformal coating on a circuit board acts as a protective barrier against corrosion, harsh environmental conditions, and intense chemicals. Various coating materials like acrylic, urethane, silicone, epoxy, and perylene are available. Material selection depends on a few factors, such as operating temperature range, condensation, repair, and tin whisker mitigation.
These materials possess different properties suitable for various applications. Parylene coating provides excellent penetration into cracks, is an ideal barrier and insulator, and has high thermal and UV stability. Therefore, it is a good choice for aerospace applications.
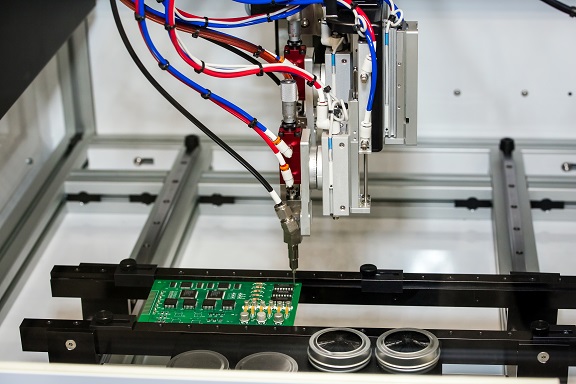
Heat dissipation
Heat dissipation removes the excess heat from the circuit board. It also means the heat transport by controlling thermal resistance (resistance to the heat flow). The following points will assist you with establishing good thermal conductivity:
- Selecting components satisfying aerospace manufacturing standards.
- Choosing board materials according to space constraints.
- Analyzing the temperature limit in the design stage.
- Conducting thermal analysis to ensure dissipation.
These elements assure good conductivity resulting in better heat dissipation. Poor thermal conductivity poses serious problems like component damage, degradation, delamination, and even fire. Some common heat dissipation methods consist of using:
- Heavy copper
- Heat sink
- Cooling fans
- Suitable component placement
- Thermal vias
- Advanced colling methods
However, this choice can be made according to the latest trends and technologies.
According to Paul,“heat is dissipated most effectively with thermal vias stitching down to the heat sink. Another way is to mill the edges of the board to a ground plane. After that, the board slots in and begins to dissipate heat.”
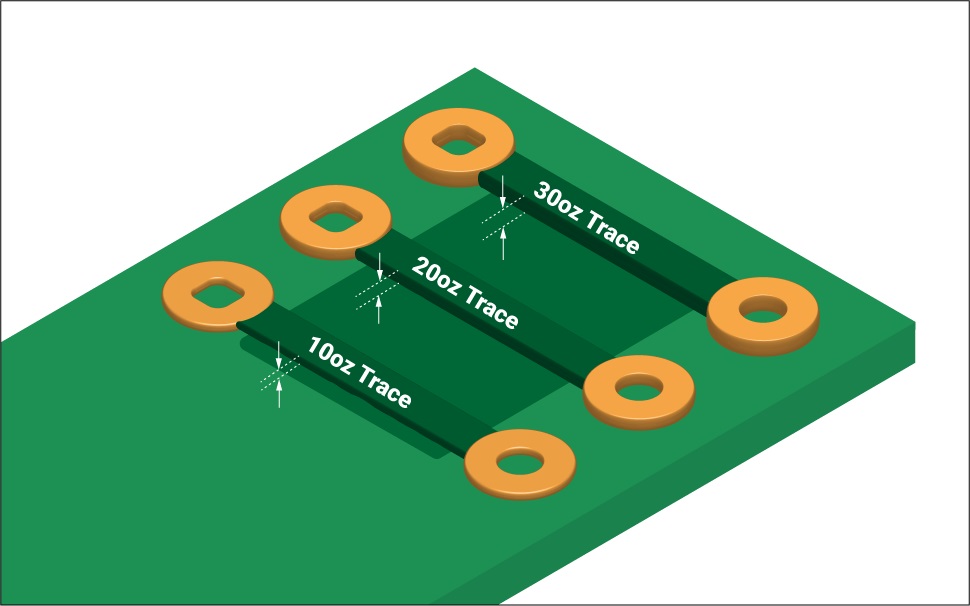
Cushioning
PCBAs for aerospace thermal control systems should use components with tight tolerances (1 to 2%) to accommodate the high current flow. It is a good practice to add extra design cushion or higher safety factors to ensure that the applications will survive in extreme conditions.
The extra cushion enhances durability and efficiency. For example, a trace carrying a 1 amp current could be designed to carry 2 amps, which is a safety factor of 2 to prevent it from overheating.
Regulatory compliance
It is essential to consider specific features, suitable processes, and component performance for establishing compliance for aerospace boards. Military and aerospace boards require adherence to certain standards.
- AS 9100: Aerospace quality management system
- IPC 2220 series: Circuit board design and fabrication
- IPC-A-600: Board acceptability requirements
- IPC-J-STD-001 and its H revision: Soldering requirements
Here’s what Christopher Young, President of Young Engineering Services, has to say about aerospace PCB design challenges.
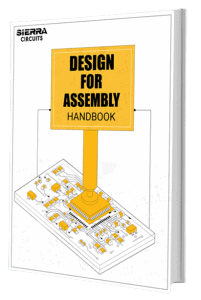
Design for Assembly Handbook
6 Chapters - 50 Pages - 70 Minute ReadWhat's Inside:
- Recommended layout for components
- Common PCB assembly defects
- Factors that impact the cost of the PCB assembly, including:
- Component packages
- Board assembly volumes
Download Now
What are the types of thermal control systems?
There are two types of aerospace thermal control: passive and active. Let’s discuss them in detail.
Passive thermal control system
This system controls the constant temperature of components without using powered devices. A passive system works best in case of low power, mass, and volume requirements.
Multi-layer insulation
MLI (multi-layer insulation) blanket is made up of multiple inner layers of thin material having a low IR emissivity, and an outer layer containing a durable material. MLI acts as a thermal radiation barrier to protect spacecraft from incoming solar and IR flux.
It also prevents the unwanted dissipation of heat and controls the temperature range of electronics (including circuit boards) and batteries in orbit. Despite this, there are some challenges associated with MLI. Its performance drops if compressed, resulting in short circuits. So, it is best to avoid placing it on the outer surface of small satellites that fit into a deployer (pushing the spacecraft out of its launch vehicle and into the appropriate orbit).
Thermal interface materials
Thermal interface materials increase the conductive heat transfer between two components. These materials exhibit various forms, such as grease, paste, or sheets. Thin sheets can be employed between the mounting surface and heat-dissipating electronics to lower the temperature. The efficiency of these materials relies on the contact pressure essential for heat transfer.
For high heat-dissipating chips, thicker pads are used on the PCBs. Several properties influence the choice of these materials, such as thermal conductivity, thickness, electrical isolation, temperature range, etc.
In Paul’s opinion, “COOLSPAN is probably the best thermal interface material because it is thermally and electrically conductive.”
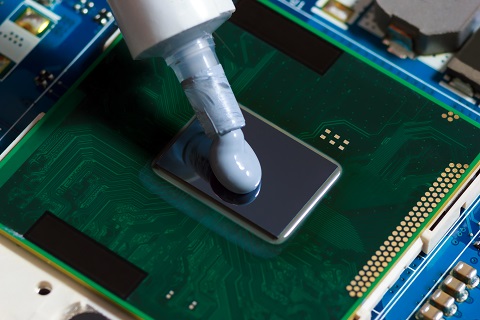
Thermal straps
A thermal strap is a flexible link that transmits heat from a heat source to a sink. Often, these devices are utilized between high heat-generating chips or components and a chassis wall or radiator surface. Because of their flexibility, it is not necessary to add structural loads.
These are created by using copper, aluminum, or graphite (because of high conductivity). They are built with cables or numerous foil sheets with end blocks to hold them in place. Straps having more than two end blocks and several material combinations can be equipped for big spacecraft.
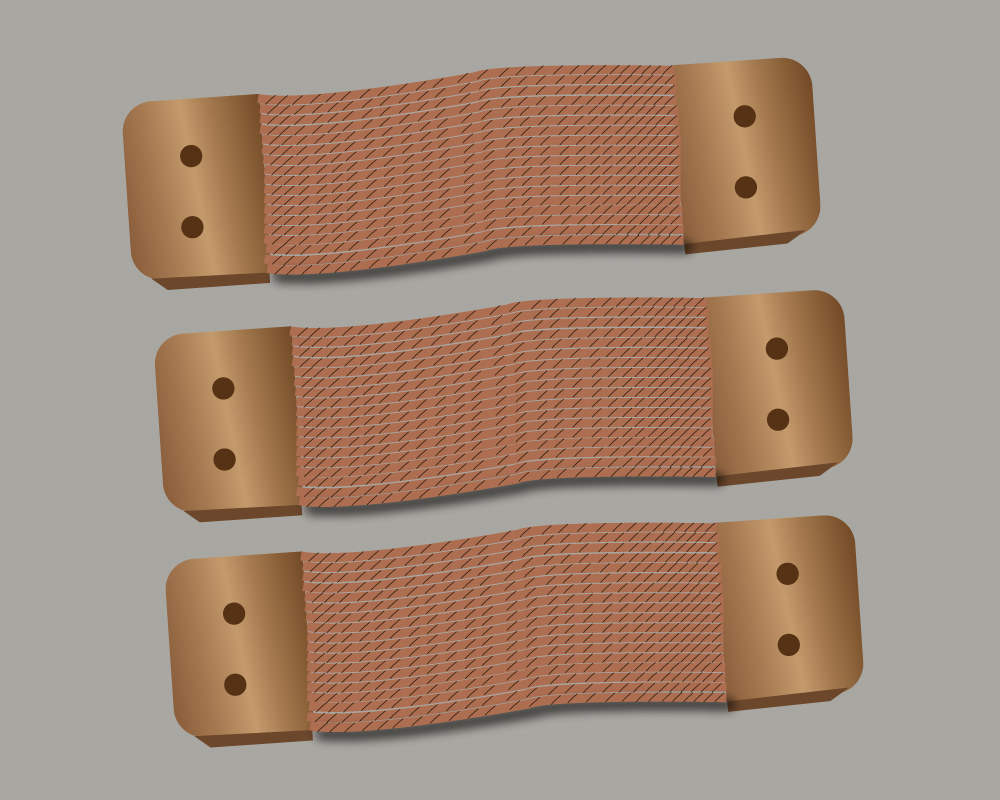
Sunsheilds
A sunshield, also known as a sunshade, is an apparatus that lessens the portion of incident solar flux striking a spacecraft by obstructing the sight to the sun. It can operate for multiple months at temperatures below 100 K in low earth orbit.
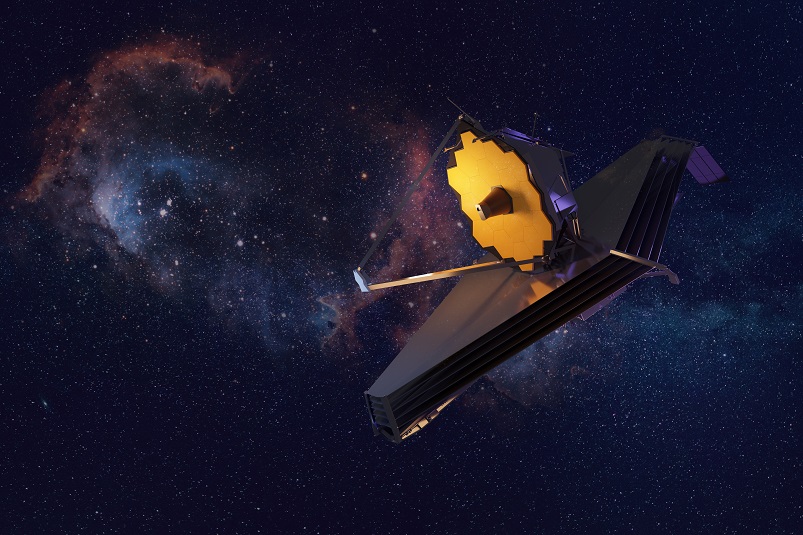
Heat pipe
A heat pipe is a mode of passive heat transfer. It uses a closed-loop system to carry the surplus heat through temperature gradients from electrical machines to a colder surface (radiator or heat sink).
Radiators
Radiators are machines that transfer excessive temperature through radiative heat exchange mode. These devices achieve aerospace thermal control due to low solar absorptivity and high IR emissivity. In aerospace, a deployable radiator is used to enhance thermal performance.
Active thermal control system
Active TCS requires input power for operation, and it is more effective in controlling the stringent temperature needs of components.
Cryocoolers
Cryocoolers are employed for cryogenic cooling (a method that uses extremely cold temperatures for material cooling). These are the refrigeration instruments that cool below 100 K. In space, these coolers are used for high-precision IR sensors, interferometers, and spectrometers to work effectively at low temperatures. Cryocoolers offer:
- Minimum vibrations
- High thermodynamic efficiency
- Extended lifetime
- Cooling temperature less than 50 K
Read our post on how vibrations in space vehicles affect PCBA to gain an in-depth understanding of vibration sources and their effects on circuit boards.
Heaters
Usually, small spacecraft employ Kapton heaters that include polyamide circuit boards. These heaters maintain battery temperature in cold environments. Generally, small satellites require a low-power heater for temperature control. These devices control thermal regulations in eclipse and attain thermal stability for biological payloads.
Thermoelectric cooler (TEC)
TEC systems use the Peltier effect (the electric current flowing through a junction will emit or absorb heat to stabilize chemical potential difference) to dissipate excess temperature using a heat exchanger. TEC is operated by current flowing through the ceramic substrates to create heat transfer and a temperature differential, where one side of the TEC is cold, and the other is hot.
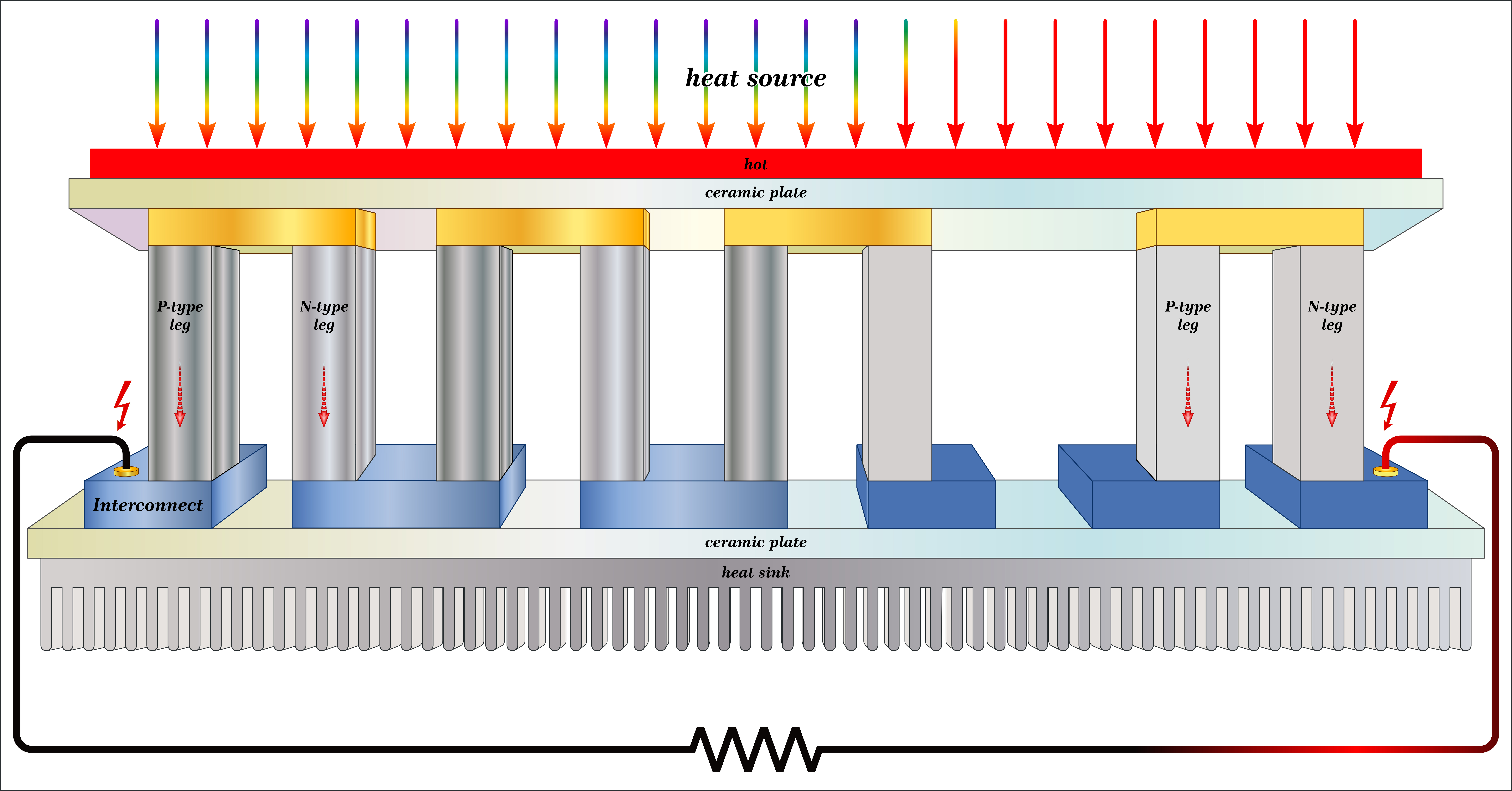
Active thermal control involves other techniques, such as fluid loops, active thermal management, and some advanced techniques. It is wise to decide after careful observation of these methods.
Remember the following three points regarding PCBA for aerospace thermal control:
- Classify components according to their thermal characteristics. The best way to design a board is to group components with similar thermal properties. Always use space-grade parts for utmost reliability.
- Position sensors near the target area. It is crucial to construct sensors based on the precise location where they will be used in the spacecraft.
- Consider the manufacturing and operational temperature limits while building the boards. For instance, materials are selected based on their resistance to stresses, but they should not violate the thermal restrictions.
Paul concluded by saying, “Reliability is a function of design rules and appropriate fabrication specifications (conservative-type features) such as minimum plating thickness, surface finish, etc. Ensure that the contract manufacturer is capable of building high-level products (class 3).”
If you have any further questions about aerospace thermal control systems, please let us know in the comments section. Check out our design guide to learn more about class 3 boards used in space and defense electronic devices.
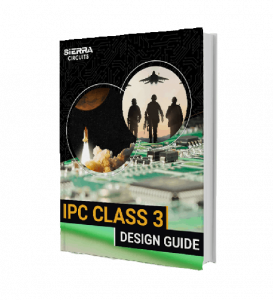
IPC Class 3 Design Guide
8 Chapters - 23 Pages - 35 Minute ReadWhat's Inside:
- IPC guidelines for manufacturing defects
- IPC standards for assembly processes
- Common differences between the classes
- IPC documents to set the level of acceptance criteria