Contents
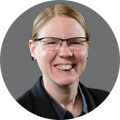
On-demand webinar
How Good is My Shield? An Introduction to Transfer Impedance and Shielding Effectiveness
by Karen Burnham
For more than 40 years, I have been teaching that perfect soldering is easy – the solder will do the work. However, most people who have not attended one of my Science of Soldering© classes do not find soldering all that easy and question my sanity. So let me add this clarification: Perfect soldering is easy provided we make it easy. The hard part is learning what makes soldering easy. And perhaps nothing is more important than understanding soldering flux selection and proper usage.
Blog written by:
James A. (Jim) Smith, PhD ABD, President, Electronics Manufacturing Sciences, Inc.
jsmith@emsciences.com
There’s no shortage of articles about flux on the Internet. Unfortunately, most (not all, but most) of the free advice is worth exactly what it costs. Dozens of manufacturers each sell dozens of flux formulations, almost all of those formulations being proprietary secrets that the customer won’t know, and they all post-marketing materials making claims that can be misleading and, in some cases, fraudulent. (Beware of “neutral pH” flux.) Anyone who knows enough to distinguish between what is valid and what is junk probably doesn’t need the research. The truly meaningful literature about flux (some of it free on the Internet but often behind paywalls) is written by chemists for chemists and completely unintelligible to the people who actually use the flux. Even the terminology can be impenetrable. The following, in plain English, is the heart of what users need to know about why flux is needed, the ingredients of flux and what they do, and general issues. Part 2 will explain flux categories, how to read a flux manufacturer’s technical data sheet, and how to determine the best flux for various situations.
This is the first of a two-part series and explains the fundamentals of soldering flux. The second part will explain the various types and classifications for electronics fluxes as well as the parameters that should be taken into account when selecting flux for specific uses.
To learn the constituents of soldering flux, see soldering flux: acids, solids, and solvents.
What soldering flux does
Understanding flux requires comprehension of what it does. As with most things related to soldering, that begins with wetting forces.
Solder flow is called wetting. When solder flows over a surface like a component lead, it is said to “wet” the surface. Failure to flow is non-wetting. What many people call “cold solder” actually has nothing to do with lack of heat; it is simply non-wetting. (I prefer the term I learned in Britain: “dry joint.”)
Four natural forces determine the amount of wetting. Two forces work against solder flow and are called “negative wetting forces.” They are:
Surface tension: Atoms on the surface of a liquid are attracted to atoms within the liquid. Some liquids have very low surface tension while others have higher surface tension. To see the difference, pour a little alcohol (very low surface tension) on a non-porous surface like glass. Then do the same with water (much greater surface tension). Alcohol flattens and spreads easily while water tends to bead up. Solder’s surface tension is much stronger than water’s (and greater with lead–free solder than leaded solder) and causes solder to form a sphere (the well-known “solder ball”). Surface tension is the most powerful negative wetting force.
Friction: Resistance as an object moves over the surface of another object is called “static friction” but friction also exists within liquids (“viscosity”). Both forces work against solder wetting but are less consequential than surface tension.
A third force (gravity) either helps or impedes wetting:
Gravity: Think of it as weight, pulling towards the ground. Gravity helps wetting at and below where the solder is applied (into plated holes if hand soldering, for example) but works against wetting above the solder application point (fighting vertical fill of PTHs in wave soldering).
The sum of those three forces is negative, meaning non-wetting. Wetting requires a fourth force – positive and stronger than the sum of the other three. That force is interatomic attraction between pure surface metal and solder. Note the emphasis on pure (elemental) metal. The atoms of metals that are good electrical conductors are unstable; they want to combine with other element(s) to share electrons. The resulting compounds have no reactive energy (the usual term is “passive”) and will not attract solder.
When solder is applied to a pure metal surface, there will be strong attraction between the surface metal and tin (the solder).[1] The attraction exceeds the negative wetting forces and the solder wets, flowing onto pads and leads or up PTHs. At the same time, a chemical reaction between the tin and surface metal creates a compound known as an intermetallic bond. In the case of copper, the resulting intermetallic consists of 3 copper atoms combined with one atom of tin (i.e., Cu3Sn) with a melting temperature of 1248°F/676°C.[2]
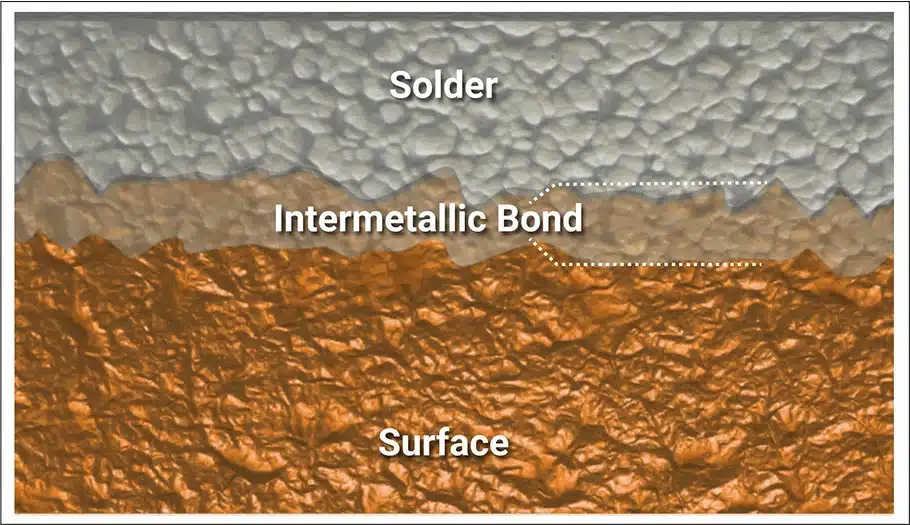
More about oxidation and deoxidation [3]
Wetting requires application of solder to pure metal. But the metal surfaces (except gold [4]) found in normal electronics are not pure metal; they are covered by an inert compound – metal oxide. To achieve wetting, the oxide must be removed before application of the solder.
Metal oxides are created by chemical reaction between metal atoms and oxygen atoms. The reaction (“oxidation”) begins instantly whenever a pure metal surface is exposed to oxygen. The oxide layer produced in that instant is enough to prevent the necessary contact between solder atoms and elemental metal beneath the oxide. However, oxidation may not stop with surface oxidation. Further oxidation will continue as long as oxygen atoms can reach metal atoms under the oxide.
At a molecular level, the oxide layer is not a continuous sheet like a table top; it is porous. Think of it as analogous to a window screen. If the oxide pores are larger than oxygen atoms, oxygen will pass through the pores to the pure metal underneath and create more oxide.[5]
Oxide porosity depends on the metal. Iron oxide (rust) has large pores while the pores of stainless steel (an alloy consisting largely of iron) are smaller than oxygen molecules. The difference in porosity explains why iron eventually undergoes complete oxidation (“rust”) while stainless steel pretty much lasts forever; the stainless steel oxide layer protects the underlying metal from oxygen while oxygen moves easily through porous rust to reach any remaining pure iron. [6]
Copper and tin can oxidize more thoroughly than stainless steel but eventually the pores close and oxidation stops. Again, it helps to think of oxide in terms of window screens. A single screen is permeable but stacking many screens with just a slight offset of each eventually forms an impenetrable barrier.
The attractive force between metal and oxygen also varies from metal to metal. Stainless steel does not form thick oxide layers but the attractive bond between the metal and oxygen is very strong. Copper oxidizes more than stainless steel but only forms weak oxide bonds. The bond between tin and oxygen is especially weak. Nickel oxidizes very slowly but the bond with oxygen is fairly strong – much less than the bond between stainless steel and oxygen but far greater than the force with which oxygen bonds to tin or copper.
“Solderable” and “solderability”
The concepts of solderability and solderable – two words that seem interchangeable but actually have very different meanings – are crucial to understanding soldering and fluxes. “Solderability” is the difficulty of removing oxide from a range of parts and is relative rather than a fixed condition. If Part A can be deoxidized more easily than Part B, A is said to have better solderability. Tin has better solderability than copper which has better solderability than nickel. However, among various pieces of the same metal, some may have less oxide and, therefore, better solderability than others. Solderability of components typically degrades with age. Newer parts usually have better solderability than older parts with the same metal surfaces.
Although they may seem like synonyms (and are often confused) the meanings of “solderability” and “solderable” are very different and the difference is important. Solderable relates entirely to the flux being used. While solderability is comparative (Part A having better solderability than Part B above), solderable is binary (yes, it is solderable, or no, it is not) and has meaning only for the soldering flux being used. If the flux to be used will deoxidize the part in the time available until application of solder, the part is solderable. If the flux cannot remove all the oxides in that time, the part is not solderable.
Part A that we specified as having better solderability than Part B may not be solderable with our flux.[7]
The difficulty of removing oxides (solderability) is determined by two factors:
1. The amount of oxide. Thicker oxide means deoxidation will be more difficult because:
a. Deoxidation is a chemical process in which acid is neutralized in the reaction with oxide. (The chemical reaction produces water and metal salts.) The acid content may be exhausted before all oxides are removed.
b. Even if the acid is not exhausted, oxides under the surface oxides cannot be removed until the surface oxidation has been removed. There may not be enough time for all oxide to be removed before application of the solder.[8] It is important to remember that sufficient oxidation to eliminate interatomic attraction will happen instantly, deoxidation requires time. The time required may be brief but it is real.
2. Type of metal. Tin and copper oxides are easily removed. Deoxidizing nickel (which has stronger bonds with oxygen) is substantially more difficult. Stainless steel, aluminum and titanium are very difficult to deoxidize. Contrary to popular belief, not all shiny silver surfaces are easily deoxidized. Deoxidizing chromium, a shiny silver metal, is harder than deoxidizing stainless steel.
Solderability reflects the strength of acid required for deoxidation. Stronger flux requirement equates to greater “difficulty” (inferior solderability). This is discussed in the section “Deoxidation” below.
However, there is no point in removing oxides if new ones can form before solder application. Sandpaper, for example, can remove oxides. Plumbers sand pipes all the time.[9] But the sanded surface will instantly form new oxides. The new oxide layer may be just a single molecule thick but that tiny layer has no surface energy and wetting will not occur. It is not enough to remove oxides. Formation of new oxides must be prevented.
Flux can be defined as any material that removes oxides and prevents formation of new oxides until solder can be applied.
Although it can remove oxides, sandpaper does not prevent reoxidation and is not a soldering flux. But many materials can prevent reoxidation as well as removing initial oxides. Some of those materials can be surprising. Hydrogen gas, for example, is used in soldering some small high frequency radio modules where even small amounts of flux residue would cause unacceptably high current leakage.[10]
Setting aside exotic but rarely used materials like hydrogen or formic acid/nitrogen gas, all electronics-grade fluxes contain:
- Acids, even if the acids are not very strong. Precision in terminology is important.
- Coating material (“solids” also known as “vehicles” or, if you want to impress with fancy words, “rheological additives”) to prevent oxygen from reaching the deoxidized Traditionally, the solids consisted of rosin derived from pine tree sap but resins are common and a widely used class of fluxes known as “organic (OR) fluxes” often but not universally have glycol or glycerin as solids. Rosin is not soluble in water but glycol and glycerin are. Most but not all resins are water soluble. Part 2 of this series will look at the different flux types in detail.
- Solvent (if liquid flux). Isopropyl alcohol (IPA) is the most common solvent but water-based fluxes exist,[11] used primarily in areas with serious smog problems.[12][13] The sole purpose of solvents is easy application of the materials (acid and solids) that do the actual work.
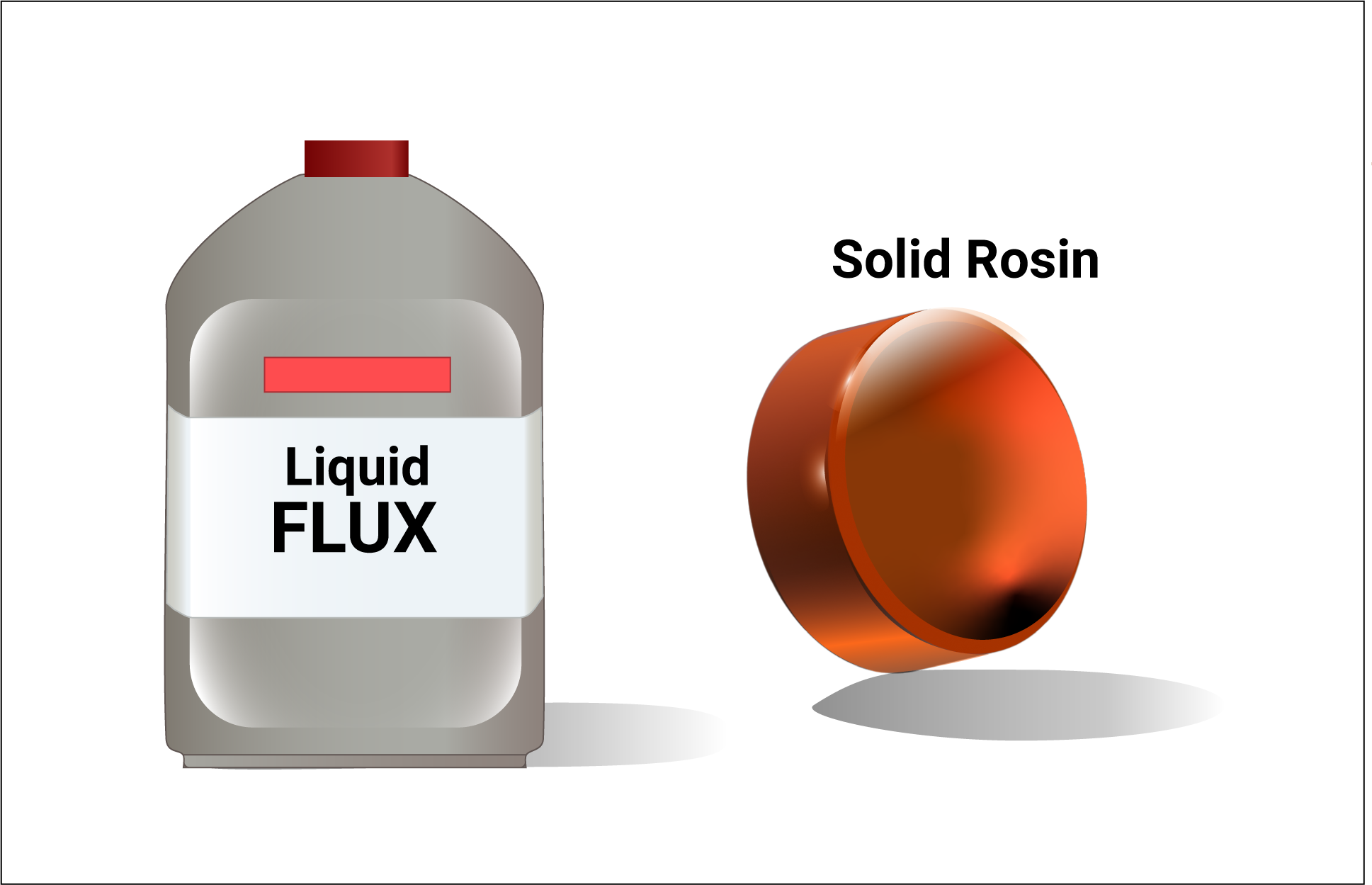
Some flux manufacturers add proprietary special purpose chemicals (surfactants, for example, to reduce surface tension and achieve better coverage). They can be considered part of the solids.
Acidity and deoxidation
Remember that soldering flux needs time to work. The amount of time may not be long but it is real and must be taken into account. On the other hand, oxidation sufficient to eliminate interatomic attraction happens instantly. As soon as air touches pure metal, the entire surface will be covered by a layer of oxide one molecule thick and the surface energy is lost. Further oxidation may happen over time and reduce solderability but the surface energy essential to wetting disappears instantly with the initial oxidation. So, oxidation happens instantly while deoxidation requires time.
The ability of flux to remove oxides is determined by its acidity, generally called flux “strength” except by chemists.[14]
Stronger acids:
- Work faster than weaker acids, and
- Can deoxidize a wider range of metals. A flux capable of deoxidizing tin or copper may not be sufficiently acidic to deoxidize nickel or stainless steel, but a flux able to remove stainless steel oxide can deoxidize tin or copper.
Deoxidation (like oxidation) is a chemical process and happens faster at higher temperatures. Often, the flux may not be acidic when first applied but heating (“activation”) causes initially neutral compounds to decompose and form acids. Some fluxes sold as “neutral pH” are only neutral until heated; when activated, they form highly corrosive acids, some of which remain after soldering and can cause failures. A different type of “neutral pH” flux begins as very strong acid that is neutralized by oxidation at high temperature in the presence of oxygen. Even acids that work at room temperature work faster at higher temperatures (typically reaching maximum activity by 300°F/150°C).
Acidity is often thought of in terms of pH[15] but pH only applies to acidity of aqueous (water) solutions. Most fluxes are not water-based, so pH isn’t relevant. The specification for acidity of non-aqueous solutions is “acid number” – how many milligrams of potassium hydroxide (KOH, a base) are required to neutralize one gram of the flux acid, usually written as mgKOH/g. Larger acid number signifies stronger acidity.
Oxide removal is a chemical tug-of-war. Acids and metals both attract oxygen with the oxygen ending up in combination with the material that exerts the greater attraction. If the flux acid attraction for oxygen is greater than the metal’s attraction, the oxide bond breaks and the oxygen combines with the acid. If the oxide bond is more powerful than the acid’s attraction, the oxide will remain intact. Stronger (higher acid number) acids attract oxygen with more force than weaker acids. Therefore, more strongly acidic fluxes can remove a wider range of oxides (or remove the same amount of oxide in less time).
Given that stronger acids are more effective at deoxidation than weaker acids, using the strongest fluxes would eliminate all wetting problems; all surfaces would be solderable and production would be much easier. Unfortunately, acid residues are ionic (electrically charged atoms) and the residues after soldering are called “ionic contamination.” The ions of stronger acids carry stronger electrical charges, meaning they are more conductive (reduce surface insulation resistance, SIR) and potentially corrosive. In other words, reliability decreases as flux acidity increases.
The risk of ionic contamination failure is determined by flux acidity (greater acidity means higher risk) but also by humidity. Risks of serious current leakage, dendrites and corrosion increase with humidity. Assemblies that function perfectly well outdoors in Arizona (close to zero humidity) may suffer high failure rates in Miami (very high humidity) in summer despite having identical ionic contamination.
Choosing the appropriate flux acidity is a balancing act. Too strong (which, in terms of acidity, is rather mild where electronics are concerned) can result in failures from SIR breakdown or, worse, corrosion. Weaker than the product can tolerate limits the range of solderable parts with no additional reliability benefit. The “goldilocks” choice is the strongest flux that will not cause ionic contamination failures. The right choice for some types of electronics can be wrong for others; the only way to know is by rigorous environmental stress testing.
Post-solder cleaning
But why not just remove the flux after soldering? Wouldn’t post-solder cleaning allow safe use of very strong acids? That would indeed be the case – if complete removal could be achieved. But it can’t. Or, more accurately, there is no way to be sure that it can.
After soldering, remnants of two flux components remain: solids and acids. The solids residues, especially rosin and some resins, can be easily seen but have little to no effect on reliability. Rosin, being impervious to moisture, actually helps reliability by acting like a conformal coating.[16] The acid residues (which are ionic – conductive and potentially corrosive), on the other hand, are not visible. An assembly with serious ionic contamination can appear perfectly clean. An assembly with visible rosin residues, on the other hand, may have perfect reliability even in high humidity environments.
In other words, in the world of electronics, “clean” is not a cosmetic condition. What can be seen is probably not a reliability problem. What can’t be seen may be catastrophic. How “clean” is “clean” has been a perennial question for decades.
The nature of materials to be removed can also complicate matters. Rosin is not soluble in water (a polar solvent) but the ionic residues are only soluble in polar solvents such as water. Both solids and ionics of another class of fluxes (so-called “organic acid” fluxes) are soluble in water but not in non-polar solvents like alcohol.
The materials to be removed may be soluble in the cleaning solvent but only if the solvent reaches them. Modern electronics assemblies with surface mount component bodies almost touching the PCB make complete contact between cleaning solvent and contaminants almost impossible. The issue is relative surface tensions of flux and cleaning solvents. Alcohol-based fluxes (the most common type) have very low surface tension and penetrate small gaps and capillaries. They readily flow under low-lying surface mount components. But removal of ionics requires use of polar solvents, the most common being water. The surface tension of water is much higher than that of alcohol (flux), however, which prevents penetration of cavities. Further complicating matters, tap water itself contains ions that will themselves contaminate circuitry. Removing ions from water (“deionized water”) causes surface tension to increase. Surfactants are often added to reduce the surface tension of water wash but the effect leaves the solution with higher surface tension than the flux. Spraying, ultrasonic vibration and other hydraulic forces are applied to force cleaning solution into the tight spaces, but there is no way to determine whether the result is adequate removal of all flux residues. Quite simply, there is no way to ensure that cleaning results in acceptable cleanliness. Ionic matter concentrated in a small area of conductors like component leads can be enough to cause failure even though the rest of the circuitry is totally free of ionic residues.
Cleaning not only does not guarantee reliability, it is expensive. Cleaning can be more expensive than the soldering itself.
If cleaning is expensive and not foolproof, why bother cleaning? Using flux that can be left on the assembly with no degradation of reliability is cheaper and more reliable. “No clean” fluxes exist and are ideal in most electronics assembly applications. But just because the label calls the flux “no clean” does not guarantee that it is truly safe.
This has been Part 1 of a two-part explanation of soldering flux. We have covered the basic science. Part 2 will explain specifics of electronics-grade fluxes including the different types, classification systems, how to read a flux specification sheet, and picking the ideal flux for any situation.
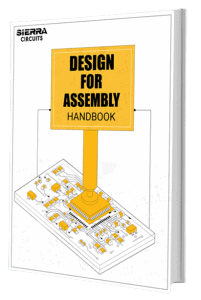
Design for Assembly Handbook
6 Chapters - 50 Pages - 70 Minute ReadWhat's Inside:
- Recommended layout for components
- Common PCB assembly defects
- Factors that impact the cost of the PCB assembly, including:
- Component packages
- Board assembly volumes
Download Now
[1] Most lead–free solders consist mostly of tin. The lead in tin/lead solder is relatively inert compared with tin.
[2] More accurately, Cu3Sn is created when the solder is liquid. Intermetallic in the form of Cu6Sn5 with a melting temperature of 779°F/415°C continues to form at a very slow rate after the solder freezes.
[3] Oxidation originally meant the formation of a new substance by the addition of oxide. For metals, this results in transfer of electrons from the metal to oxygen. Chemists now use “oxidation” to mean loss of electrons by an atom when forming a molecule even if oxygen is not involved. When metals combine with oxygen, the metals lose electrons to the oxygen.
[4] Gold does not oxidize. It does, however, react with some other elements such as sulfur to form sulfides that, like oxides, are passive.
[5] More accurately, since atmospheric oxygen atoms normally travel in pairs (O2), the oxide’s pores would need to be larger than an oxygen molecule.
[6] Further, unlike stainless steel oxide, rust tends to flake off and expose the underlying iron.
[7] At the same time, Part B cannot be solderable if Part A is not solderable, although Part A can be solderable without the same being true for Part B.
[8] Flux must work faster in hand soldering than surface mount reflow or wave soldering. With hand soldering, heat to activate the flux comes from the iron and the solder melts soon after application of the iron. In machine soldering, heat is applied for many minutes before the solder melts (or, in wave soldering, touches the area to be soldered). This long preheat means activated flux has a greater opportunity to remove thicker oxides. However, time to work is irrelevant if the solderability issue is the type of metal rather than the amount of oxide.
[9] Sanding pipes, which may have very thick oxide layers, removes the heaviest oxides and reduces the amount of work required from the flux.
[10] The components (placed on solder preforms) are inserted in ovens filled with hydrogen and (inert) nitrogen gas. At roughly 660°F/350°C, the energized hydrogen strips the oxygen from component oxide (forming water vapor). The modules emerge from the oven with thoroughly wetted solder connections and no flux residue.
[11] Deoxidation is an endothermic chemical reaction, meaning the reaction requires heat and happens faster at higher temperatures that are not reached until after complete evaporation of the solvents. Evaporation of alcohol uses little energy but evaporation of water requires considerable energy.
[12] VOCs combine with nitrogen oxides to produce ozone, a major ingredient in urban smog.
[13] There is a difference between water-based and water soluble. The residues of alcohol-based fluxes may be soluble in water. This is an important consideration in post-solder cleaning.
[14] In layman terms, acid strength is generally thought of as pH, with 7.2 being neutral and smaller numbers indicating “stronger” acid. However, chemists use “strong” and “weak” in a very different way. “Weak” acids in chemical terms are acid compounds that remain at least partially intact in water. “Strong’ acids completely decompose (“ionize”) in water. Of the myriad acids, only 7 are “strong” acids; all the others are “weak.” Weak acids (unlike, for example, hydrochloric acid which immediately separates to release hydrogen and chloride ions). Hydrofluoric acid – one of the strongest of all acids – is classified as a “weak” acid because it remains mostly intact in water. For our purposes, we will use “strong” and “weak” to mean acid potency.
[15] As noted earlier, hydrogen gas can be used as a flux. Elemental hydrogen is ionic (H+)and highly reactive. It is also the portion of the acid responsible for deoxidation; deoxidation always produces water in addition to metallic salts. pH (derived from an old term “power of hydrogen”) is determined by the H+ or hydroxyl ions (HO) in water. At 7.2, the H+ content equals the HO content. Below 7.2, H+ outnumbers HO while above 7.2 (basic) there are more HO ions. The greater the concentration of H+ ions, the lower the pH and the stronger the acid.
[16] Rosin residues do negatively affect adhesion of some actual conformal coating, can contaminate test probes and is sticky until curing. Modern “no clean” rosin fluxes leave very little residue, however.