Contents
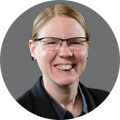
On-demand webinar
How Good is My Shield? An Introduction to Transfer Impedance and Shielding Effectiveness
by Karen Burnham
Flux consists of two basic ingredients: acids to remove oxides and a substance or substances (“solids”) to coat the surface and prevent oxygen from reaching the surface after oxides are removed. Liquid flux is just those same ingredients in a solvent.
Flux selection may be the most important decision any electronics assembly business will ever make. The right flux can save immense costs including but not limited to solder defects, cleaning and product failures. However, fluxes are complex and making the right choice involves navigating a chemical minefield complicated by occasionally bizarre terminology and, too often, shady marketing practices by some well-known flux manufacturers.
This is the second of a three-part explanation of fluxes: what they do, how they do it and which one is best for various applications. If you read Part 1, you know the fundamentals of flux and are ready for the specifics of how to pick the flux that will make your soldering life very easy. If you haven’t read Part 1 of soldering flux, that really is the best place to start.
Solder flow is known as wetting and occurs only if the solder is applied to a pure elemental metal surface. Elemental metal is unstable and has energy to draw the solder (interatomic attraction). Oxidized metal lacks that energy, however, and does not allow wetting. With the exception of gold, all component surfaces are oxidized and that oxide must be completely removed and the deoxidize surface protected from reoxidizing before application of the solder. Removal of oxides and prevention of reoxidation is the role of flux.
Flux consists of two basic ingredients: acids to remove oxides and a substance or substances (“solids”) to coat the surface and prevent oxygen from reaching the surface after oxides are removed. Liquid flux is just those same ingredients in a solvent.
Blog written by:
James A. (Jim) Smith, PhD ABD, President, Electronics Manufacturing Sciences, Inc.
jsmith@emsciences.com
Acids
The part of the flux that removes oxides, which the industry for reasons lost in antiquity insists on calling “activators,” is almost always acid, either directly or in a compound that releases acid when heated. The term used to describe flux acidity is “activity.” Most often, the acids are organic (meaning they contain carbon). Inorganic acids (compounds of hydrogen with non-metals) such as hydrochloric or hydrobromic have exceptional oxide removal properties but not compatible with electronic reliability; they leave highly conductive and corrosive residues that can cause electrical failures. Inorganic acids in the form of halides (discussed below) are found in some electronics fluxes but in very low concentrations and only supplemental to the greater amounts of organic acid.
Acid strength is determined by its hydrogen ion content; more hydrogen ions equate to greater acidity. During deoxidation (the interaction of the acid with the metal oxide, a base), hydrogen from the acid combines with the oxygen stripped from the oxide to form water while the other elements of the acid combine with the metal to form metallic salts. Stronger acids, in general, attract oxygen with more force than weaker acids. The greater attraction means stronger acids have greater deoxidizing ability (able to remove greater amounts of oxide faster than weaker acids and able to remove oxides from a greater range of metals than weaker acids).
Strong and weak acids
Let’s pause to apologize to chemists for our use of the words “strong” and “weak” in referring to acidity. For our purposes, we can think of “strong” acids simply being more powerful than “weak” acids. But chemists don’t think of potency when classifying acids as strong or weak. To them, strong acids are those that break into their constituent parts (“ionize”) when added to water. Weak acids do not ionize completely while strong acids do. This special terminology causes considerable confusion for non-chemists when laboratories testing cleanliness of circuit assemblies report that failures are due to excessive amounts of weak acid residues.
It’s mostly about hydrogen
Aqueous solutions contain hydrogen in two forms: hydrogen ions [H+][1] and hydronium ions [H3O+]. A hydrogen atom (H) consists of one proton and one electron. The hydrogen ion (H+) is just a proton (and is often referred to as a proton rather than hydrogen ion). The hydrogen ions are highly reactive and can be donors of protons or recipients of electrons in chemical reactions.
Solutions containing more H+ than H3O+ are acids and solutions with fewer relative hydrogen ions are basic. The H+ concentration is expressed as pH, the negative log of the hydrogen ions per liter – pH =−log10[H+] where [H+] represents the hydrogen ion concentration in moles (M).[2] The pH scale runs from 0 to 14 with 7.0 being neutral.[3][4] Numbers smaller than 7.0 (higher concentrations of H+) are acidic and greater than 7.0 are basic.
This is a highly simplified look at acids. There are actually three different definitions for acid, two of which are exclusively concerned with hydrogen but a third defines acid in a manner that does not require hydrogen. It’s not necessary for our purposes to go there.
pH vs. acid number
Non-chemists often think of acid strength in terms of pH but, for the most part, pH is not relevant where flux is concerned. For reasons we will get to later, the solvent of most liquid fluxes is alcohol rather than water while pH applies only to water-based solutions. For solutions not based on water, the relevant measure of strength is “acid number,” the number of milligrams of potassium hydroxide (a base) required to neutralize a gram of the acidic material. For the purposes that matter here, acids work the same in aqueous and non-aqueous solutions; only the acid measurement system differs.
The “strength” of an acid depends on concentration of hydrogen ions. A lower concentration (content by total volume) of acid will have lower pH or acid number than a higher concentration of the same acid. This is important with respect to use of very reactive halides in electronics fluxes, discussed below.
“Neutral pH” flux
Fluxes labeled “neutral pH” are available, including from some very prominent flux brands. And they are extremely effective for oxide removal, capable of deoxidizing some of the least solderable metals.[5] How can something “neutral” (which, after all, means non-reactive) remove oxides? The answer, of course, is that they are not “neutral” at all temperatures.
Neutral fluxes come in two forms. The first goes on as a neutral compound but produces acids when heated. The acids are very strong and, therefore, excellent for deoxidation. But highly conductive and corrosive ionic residues are created that and must be removed after soldering.
The second type starts out with high acidity but is neutralized by reaction with oxygen at high temperatures. The problem is that there are situations where not all of the flux reaches the neutralization temperature and any flux in cavities or under components displaces the air (and oxygen) needed for neutralization.
Both types of neutral flux come with the requirement that they be washed off after soldering. The residues are water soluble and can be removed by water if the water can reach the residues. This is not certain. Flux has low surface tension that allows it to penetrate tight spaces. In fact, the ability of the flux to enter those spaces that require deoxidation is very important. But water has very high surface tension and cannot reach flux in cavities. Moreover, tap water, like flux, contains conductive and potentially corrosive ions that will degrade reliability. Cleaning must use water from which the ions have been removed (“deionized” water). But the surface tension of deionized water is greater than the surface tension of tap water, increasing the likelihood that the wash water will not reach all flux residues.
Activation
Deoxidation is an endothermic chemical reaction and happens faster at higher temperatures. Although some strong acids can remove some oxides at room temperature, all acids work faster when heated and the acids in electronics flux generally do not begin to work until heated. The minimum temperature at which the acid begins working is the “activation temperature.” The activation temperature is often in the range of 150°F/65°C but that is only the starting point.
In many cases, the flux acids begin as inert compounds at room temperature. They must be heated to break down and form acids.
A few words about halides
Although fluxes rely primarily on acids for oxide removal, some also contain small amounts of metal halide to reinforce the acid. Sodium chloride (table salt) is a common halide, though not one found in flux. Only compounds of chlorine and bromine are used in flux but there are several possibilities and there is no way of knowing which halide is in a flux.[6] When the halide encounters water (one of the byproducts of deoxidation when hydrogen of the acid combines with oxygen from the oxide), it separates into the metal ion and halogen anion, generally either chloride or bromide. Interestingly, the halogen is a base like metal oxide, not an acid, but it vigorously attacks oxide. Why and how? The answer isn’t clear. Scientists are still arguing about the reason halogens attack metal oxide (possibly because the halogen is a stronger base than the oxide, but that has not been proven).
It is known that a small amount of halogen (from decomposition of the halide) enhances the work of the flux acids. It’s also known that halogens carry a strong electrical charge that is destructive to electronic circuitry in large amounts. To qualify as halide-free under J-STD-004B, the current classification system, a flux must contain less than 0.05% halide by volume (that is, for liquid flux, volume excluding solvent). That is a very difficult level to stay under and most fluxes suitable for use in production of reliable products do not qualify for halide-free status. However, high reliability fluxes contain less than 0.5% halide by volume.
The ionic contamination problem
In an ideal world, there would be no negative consequences for using strong acids and halides. Our world is not ideal, however, and both the acid and halides present serious reliability challenges. The acid and halide residues are ionic and their residues after soldering are called “ionic contamination.” Ionic means they are electrical conductors and, potentially, corrosive. In general, though not absolutely, the conductivity and corrosivity increase with strength of the acid or base.
Conductive residues can allow electrical current to flow between non-common conductors (“current leakage”) rather than through the circuitry. Most electronics assemblies can tolerate some current leakage, but all assemblies have limits easily exceeded by the ionic or anionic residues of relatively mild fluxes. Higher ionic levels (greater ionic charge and/or more ionic material) can allow formation of dendrites. And even higher ionic levels can cause corrosion.
Flux strength classifications
Electronics fluxes are classified as low, medium or high “activity” (written L, M and H) on the basis of the conductivity and corrosivity of their residues after soldering. The rules are spelled out in an industry document J-STD-004B issued by the trade association IPC. Corrosivity is determined by applying the flux to a thin layer of copper on a glass plate and seeing whether and by how much the flux breaks through the copper leaving only the glass. (Where copper has been removed, it is possible to see through the glass underlay.) Conductivity is more complicated.
The procedure for determining conductivity is rather complicated but, in essence and very generally, the steps are:
- Apply the test flux (from cored wire solder, paste, liquid or solder paste) to coupons (laminate with a comb pattern of fine traces spaced .020” or .508mm apart).
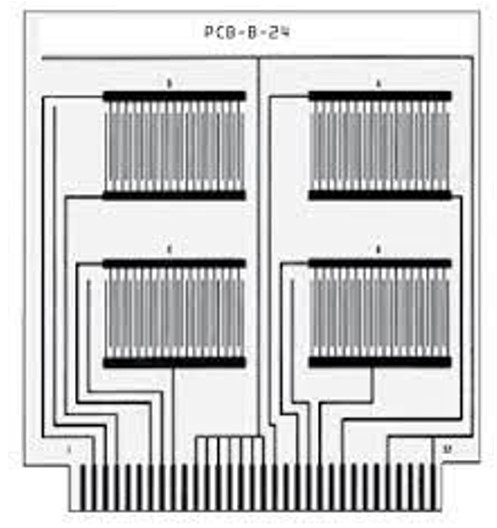
- Run the coupons through a reflow oven set to normal process temperature or across a solder wave
- Clean some of the processed coupons
- of cleaned and uncleaned coupons
- Place the clean and uncleaned coupons in an environmental chamber at 40°C and 90% relative humidity
- Apply current and measure the change in SIR after 96 hours and after 7 days
- Flux passes the test if:
- The SIR does not fall below 100 MΩ at any point and
- The SIR does not fall below 1000 MΩ after 96 hours until conclusion of the test and
- Dendrites (electrical bridges between uncommon conductors created by migration of positively charged metal ions migrating to a negatively charged conductor) do not form
Fluxes whose coupons pass the conductivity test without being cleaned and do not break through any coverage area in the copper mirror test are classified as low activity (L). Some medium activity (M) fluxes break through up to 50% of the coverage area on the copper mirror but may pass the conductivity test without cleaning but most do require cleaning to pass the conductivity test. H fluxes break through more than 50% of the copper mirror coverage area and require cleaning to pass the conductivity test. Fluxes that cannot pass the conductivity test are stronger than H and not suited for use on electronics assemblies.
The flaw in J-STD-004B
The conductivity test has several critical flaws. Most importantly, heating the flux in a reflow oven or wave solder system can neutralize organic acids. With enough temperature (150°C or more) in the presence of oxygen (the air that surrounds us), the organic acids will oxidize and become neutral. In other words, the flux acids may be neutralized before conductivity and dendrite tests are conducted. Defenders of the classification procedure contend that the flux will exceed the neutralization temperature during application of the solder. Critics (myself included) point out that this is by no means guaranteed. Flux that is not in contact with a soldering iron, for example, may never get above room temperature. Flux trapped in cavities or under surface mount components displaces the oxygen-containing air and will not oxidize not matter what temperature they experience. There are other scenarios under which flux fails to reach neutralization temperature. Further muddying the water, a group of fluxes use compounds that are initially neutral but form very strong acids when reaching a sufficiently high temperature that may be more than the peak temperature during processing of the test samples.
When selecting flux, the J-STD-004B rating is a good place to start; it saves a lot of time that might otherwise be spent evaluating completely unsuitable fluxes. However, the safety of the flux in its pure state (not heated) must also be taken into account. Many fluxes qualified as low activity by J-STD-004B have suspiciously high acid numbers and not all of that flux in every area of a circuit assembly will experience meaningful heating during soldering. Unfortunately, the information about flux conductivity before heating is not usually available.
Conductivity of flux residues does matter enormously. Failures occur when too much electricity chooses to flow through the acid residues between non-common conductors rather than following the circuitry. How much current leakage is “too much” depends on the required precision of the product involved and the environment where the product needs to operate. (The problems with ionic contamination increase as humidity increases. An assembly sitting in a desert will be much less affected by ionic contamination than the same assembly in a swamp.)
Some more about halides
Halides get special treatment in flux classification. Because the residues of halides are highly conductivity and corrosive, fluxes containing halides are classified separately from those that do not (“halide-free”). Fluxes that contain halides are also classified according to the percentage of halide. Only fluxes containing less than 0.05% halide by volume (based on the flux contents without solvent) can be classified as halide-free. Low activity halide fluxes contain less than 0.5% halide by volume. The halide content limit for medium activity halide fluxes is less than 2.0%. High activity halide fluxes contain 2% or more halide. This results in six activity levels: L0, L1, M0, M1, H0 and H1 with 0 for halide-free and 1 for containing halides within the specified limits.
Solids
Oxides must be removed or the solder will not wet. However, removal of oxides, on its own, is not sufficient. If oxygen can reach the deoxidized surface, new oxides will form instantly and the surface energy lost. In addition to removing oxides, flux must provide a barrier preventing oxygen from reaching the newly deoxidized metal until solder is applied. That is where the solids come in.
Flux manufacturers have their own jargon, such as “activators” instead of acids. The traditional but increasingly uncommon jargon for solids is “vehicle,” presumably because the acids are carried in the solids. “Solids” more accurately reflects the material’s role in providing the barrier against oxygen.
The role of solids
Solids exist only to prevent oxygen from reaching the deoxidized metal while solder is being applied. That’s all. They do not remove oxides. They are not conductive. They are not corrosive. They make up a much greater percentage of the flux volume than the acids. Any visible flux residues after soldering are remnants of the solids; the acids are not visible. As contract manufacturers know, however, their customers have no knowledge of soldering science and want to reject assemblies with visible residues. (Depending on the nature of the solids, they can cause problems such as contaminating test fixture pins or preventing proper adhesion of conformal coating, but these do not in themselves affect product integrity. In the case of conformal coating, switching coating materials can often eliminate the adhesion problem.) Because of pressure from uninformed customers, many contract manufacturers adopted flux formulations that leave no visible residues and, of course, flux manufacturers created new formulations to meet demand for invisible solids.
Rosin
Historically, all electronics fluxes used rosin[4] for solids. Rosin is derived from sap of certain pine trees after most of the volatile components have been evaporated (forming turpentine, among other derivatives). Anyone who has handled a Christmas tree is very familiar with one rosin property – it is very sticky (until all remaining volatiles evaporate, at which point the rosin feels and acts very much like polyurethane, although the two materials are very different chemically).
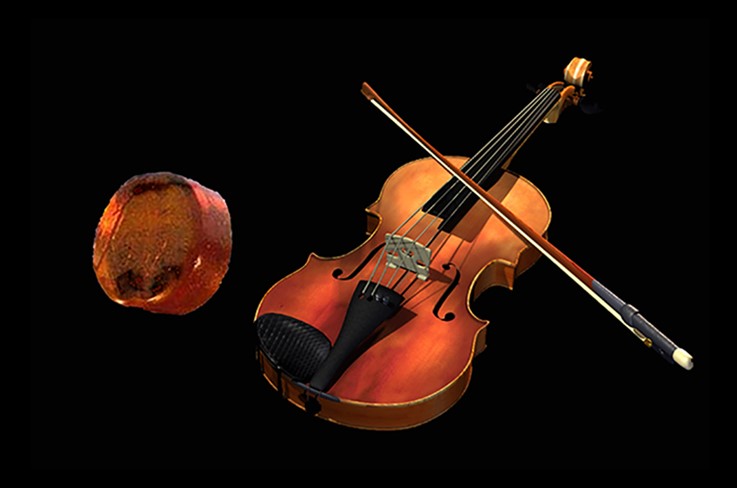
Musicians use it with stringed instruments.
Rosin has two properties that make it ideal for use in electronics fluxes. First, it tolerates soldering temperatures without breaking down, ensuring that the deoxidized surface remains protected from oxygen. Second, and even more important, it is hydrophobic (repels moisture). Rosin encapsulates the acids in a moisture-free environment that minimizes conductivity and corrosion. (All the unpleasant consequences of ionic contamination require some humidity. Resistance to current leakage goes down as humidity increases.)
Rosin in its natural state contains a very mild organic acid, abietic. The acid is not strong enough to remove many oxides other than tin oxide. Stronger acids are added to fluxes suitable for production but rosin in alcohol without extra acids is still sold for use with tin-plated parts. (Under the now obsolete MIL standard for flux, rosin in alcohol is designated “Type R.”)
Rosin is nonpolar and not soluble in water, which is polar.[5] Attempting to mix rosin in water results in a gooey mess (not a technical term but an accurate description). Powerful solvents such as trichloroethane that were very effective for removing rosin residues in the past are now banned for environmental and health issues. No currently available solvents can equal the ability of trichloroethane to remove rosin and the solvents that are available are expensive. It is intended to be left on the circuitry after soldering.
The main issue with rosin is its visibility. The brown residue stands out after soldering. The residue is harmless (though the acid contained in the rosin may be an issue, but only if the wrong strength of flux is used) but too often interpreted by the uninformed as signifying poor reliability. Soldering operators often spend great time and effort removing the visible rosin after soldering, a total waste of resources. “Cleaning” with a brush or cloth and solvent after hand soldering accomplished little except spreading the flux residues over a larger area so they are less visible.
The amount of residue remaining after soldering is determined by the concentration of solids in the flux. The way to avoid annoying amounts of rosin residue is to avoid fluxes with high concentrations of rosin. Because they were formulated for early versions of wave soldering where excess solder such as bridges could be prevented by high concentrations of rosin (40% or more in some cases), many rosin fluxes still in common use today contain many times more solids than are needed for today’s soldering. Dark brown liquid flux provides no benefits to compensate for the time and money required to remove the residues after soldering. Most flux manufacturers today offer low solids (less than 5% by volume) liquid rosin fluxes that leave no meaningful residue.
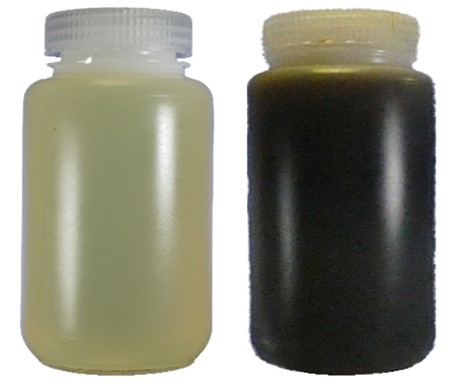
Flux cored wire solder leaves residues. The default flux content of wire solder is around 3% by weight, which translates into a very large quantity by volume. Using solder with around 1% flux content eliminates the major source of visible rosin residue. The flux inside the solder provides no great benefit in any case.[6]
Resin
The disadvantage of rosin for flux manufacturers involves profits. Rosin is rosin, regardless of the flux manufacturer’s label. At a fundamental level, there is no meaningful difference between one brand and another. But substituting a material other than rosin for the solids allows for product differentiation – and the potential for somewhat higher pricing and profits.
One type of material used in place of rosin is resins. And this gets tricky.
The Cambridge Dictionary defines resin as “a thick, sticky substance that is produced by some trees and that becomes yellow and hard after it is collected, or any of various similar substances produced by a chemical process for use in industry.” We have already discussed the material in the first part of that definition: rosin. And some resins refined from rosin have properties very similar to rosin. But other resins are not related to rosin; they are the results of chemical synthesis. Rosin is rosin but resins have many forms and, since no manufacturer reveals their proprietary ingredients, there is no way of knowing the resin used in any particular resin flux.
Water soluble solids (organic flux)
Customers of contract manufacturers (or internal customers of integrated companies with in-house production) often reject assemblies with visible flux residues. The visible residues are harmless remains of the solids and not a reliability issue, as opposed to invisible ionic contamination left by the acids but most supplier auditors know nothing about process. The easiest way to mollify uninformed customers is to replace visible solids (rosin or some resins) with colorless solids. Glycols are among the most popular replacements.
Glycols are colorless and water soluble. They leave very little visible residue after soldering and, unlike rosin, can be removed by water wash if necessary. The lack of visibility and ability to be removed by water (as opposed to expensive chemicals needed for removal of rosin) makes these fluxes very popular with contract manufacturers as well as companies producing for their own use but lacking enough knowledge to understand why rosin residues do not in themselves mean poor reliability (or that lack of visible residues in the case of solids like glycols do not necessarily reflect high reliability).
Solvents
Fluxes are available inside wire solder, mixed with solder particles in solder paste, as gels or pastes and as liquids. The feature that distinguishes liquid flux from the other forms is solvent.
The most common solvent is a variety of alcohol. It doesn’t really matter what alcohol is used; they all behave similarly. Two characteristics make alcohol the ideal flux solvent:
- Low surface tension, allowing the flux to penetrate tight spaces where oxide removal may be required, and
- High vapor pressure (the force that changes liquid to vapor without heat) that results in quick drying of the alcohol without using heat required to activate the flux and melt the solder
Alcohols are volatile organic compounds (VOCs) that are possibly carcinogenic, contribute to smog, and act as greenhouse gases. VOC restrictions in some regions, most notably portions of California, prevent the use of alcohol-based flux. The alternative to alcohol is water, which is inferior to alcohol in four main ways:
- High surface tension, so poor penetration of tight spaces including up plated through-holes
- Very low vapor pressure, so little tendency to dry after application
- Very high latent heat of vaporization. Driving off the water evaporates requires heating to 212°F/100°C, energy that would otherwise be used in activating the flux and melting the solder, and
- Spattering when a hot iron touches the fluxed workpiece or a fluxed assembly enters a solder wave
Water based is not the same as water soluble. Water soluble means the flux residues after vaporization of the solvent are soluble in water. The residues of many alcohol-based fluxes (excluding fluxes containing rosin and some resins) are water soluble.
Coming soon
The Soldering Flux eBook will explain flux categories per J-STD-004B. It will conclude with recommendations for how to pick the flux best suited to the product needs.
[1] The hydrogen ions H+ are actually paired with oxygen in the form OH– known as hydroxide but the hydrogen behaves like a standalone ion and chemists refer to the hydroxide as hydrogen ions.
[2] M represents moles per liter of water where 1 mole = 602,214,076,000,000,000,000,000
[3] A liter of pure water at 25°C contains 1 × 10-7 M hydrogen ions and the same number of hydronium ions. (1 × 10-7 M)x(−log10) = 7.
[4] “Neutral” is actually a moving target that depends on temperature. Neutral water at 25°C has pH of 7.0. At 0°C, neutral pH of 7.4 while neutral pH at 50°C is 6.63.
[5] In Part 1, I defined “solderability” as the difficulty of removing the oxide from a surface. In other words, the strength of flux required to deoxidize the part.
[6] Flux manufacturers all have their own proprietary recipes that they guard the way Coke famously hides its formula. Aside from a few generic ingredients such as rosin or isopropyl alcohol, most of the key additives are kept secret. The safety data sheet of one flux manufacturer states “Trade Secret exemption is pending with the [Hazardous Materials Information Review Commission] for one or more ingredients in this product.”