Contents
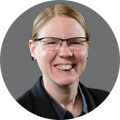
On-demand webinar
How Good is My Shield? An Introduction to Transfer Impedance and Shielding Effectiveness
by Karen Burnham
For many years the demand for polyimide and PTFE materials was very low, very specialized, confined in the case of polyimides almost exclusively to high-temperature or high-voltage applications and in the case of the PTFE laminates, such as the Rogers duroids, microwave circuits. Designers increasingly are turning to those laminates, perhaps for good reasons based on the thermal or electrical attributes listed in data sheets, but without regard to certain manufacturing characteristics that set them apart from the fabrication processes for conventional FR4. Many of those manufacturing characteristics are not apparent from datasheets.
Wise designers consult manufacturers before developing hybrid stack-ups, because combining laminates with dissimilar mechanical properties can complicate fabrication and therefore bear on cost, especially with respect to yield. By the time a design is ready to prototype, it’s often too late and too expensive to recast in a way that would achieve the design objectives yet be easier to build. My company, which is devoted to prototype manufacture and up to medium scale production, often takes on challenging projects that might have been better architected had the designers reached out to us at the stack-up stage.
Not Covered in Data Sheets
Let me focus on one aspect of hybrid builds brought to mind by a recent conversation with the engineer who supervises drilling operations here. “The problem is,” he emphasizes, “there can be very different feed and speed requirements for drilling one material compared to another.” Several designs we recently built involved three, four, even five different materials. For example, we had a project with two different polyimide materials, FR4, and flex material combined. The in-feed setting for the drills (how quickly they descend) and their spindle speed for drilling the polyimides is completely different than the in-feed and spindle speed for the flex material. Polyimide laminates are hard materials that fracture easily. Therefore, they must be drilled at a relatively low in-feed rate and a high spindle speed. Flex material is just the opposite, requiring a high in-feed rate and a slow spindle speed, because the slower the in-feed and the higher the spindle speed, the more heat that will be generated.
“It’s difficult when those materials are combined, because the polyimide can’t be drilled using the flex parameters, or vice versa, or the boards will be compromised,” the engineer points out. “The softer the material—the duroids and flex materials are about the same–the easier it is to drill, but the more susceptible it is to heat, so if you also have a harder material in combination to drill, it’s easy to distort the softer material if you go in at too high an in-feed. The drill can essentially pull the material out of the hole wall and then the material snaps back but not all the way, so one of the things you would see is that for no apparent reason there’s what appears to be negative etchback in the hole wall of the softer material.” What we are doing in such rigid-flex cases is “peck” drilling. We control the machines to drill a just certain distance and then withdraw the drills to let them cool, and then drill further. We are guided by the drilling characteristics of the most-sensitive materials.
ENEPIG—short for electroless nickel, electroless palladium, immersion gold—is a somewhat more expensive surface finish that has nearly universal advantages.
Unlike the duroids, Rogers 4000 materials have drilling characteristics that are relatively close to FR4. Some defects can result because the 4000 materials must be drilled more slowly and generate more heat. There is a tendency for the interconnects to smear a little bit in the holes—so-called nailheading—though that’s typically not cause for rejecting a board. Slowing down the feed rate for a given material in a stack runs the risk of causing some defects in the region of the hole where that material is located. Polyimides and the ceramic-filled materials have slower in-feed rates and higher spindle speeds because they are hard, and therefore less material is removed per revolution of the drill. The combination of feed rate and drill speed is sometimes referred to as chip load. A harder material necessitates a lower chip load; that is, a lower feed rate and a higher spindle speed. When you have a combination of materials, you have to adjust the drilling parameters to meet the requirements for the hardest material, or distortion inside the hole can result and that can interfere with plating the hole. But when you have two materials with very different drilling parameters, the settings are a compromise.
For manufacturers, there’s yet another consideration besides chip load and that’s drill hit count; the sharper the drill, the fewer the issues that will be encountered. For FR4 the drill hit count typically is around 800 but for a hard material, drills have to be changed after 400 or so hits, and that affects project cost.
Still another consideration internal to manufacturers is which of three entry materials will be used on top of the board stack for drilling support. There’s a coated aluminum material that’s best for drilling small holes; there’s an aluminum material with a paper core that’s used for most other drilling needs; and there’s phenolic material, which provides the most surface support and would usually be used when a soft material, such as a Rogers duroid, is the top layer of a board, but the phenolic material is the worst of the three entry materials for drilling accuracy. The phenolic entry material is hard and drills can skate when they start. If the drill diameters involved are not less than 10 mils, accuracy is not compromised by the phenolic material. If the drill diameters are much smaller, the coated aluminum material must be used or the drills will snap. However, in most cases, the amount of burring, the amount of debris in such small holes as a result of using the coated aluminum material is negligible.
There is considerable work among laminate suppliers to provide alternatives to polyimide and PTFE materials whose manufacturing characteristics are closer to those of FR4.
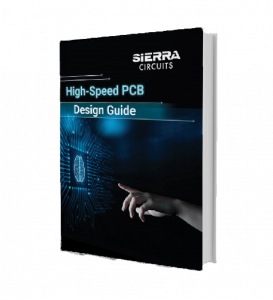
High-Speed PCB Design Guide
8 Chapters - 115 Pages - 150 Minute ReadWhat's Inside:
- Explanations of signal integrity issues
- Understanding transmission lines and controlled impedance
- Selection process of high-speed PCB materials
- High-speed layout guidelines
Download Now
Switching Gears
Let me turn to a different design consideration that influences manufacturing and cost as well as electrical and mechanical performance: surface finish. For example, if HASL [hot-air solder leveling] is selected, the PCB design must not include any fine-pitch components because a HASL surface finish will be too uneven to ensure uniform contact bonds for such parts. Immersion silver or immersion gold finishes are better alternatives if devices with tight contact pitches are involved. The immersion gold finish is called ENIG (electroless nickel, immersion gold).
Immersion silver does not require a layer of nickel underneath as does the immersion gold finish. The nickel is used as a barrier layer to prevent copper migration into the gold over time, which can result in increased contact resistance if boards are left unassembled too long. Both immersion silver and ENIG result in even surfaces that are much flatter than can be obtained with HASL; moreover, both are more electrically conductive. The overall thickness of the immersion silver finish can be held to a tighter tolerance than that for ENIG, so silver is preferred if there are press-fit connectors in the design. However, silver tarnishes quickly and assembly must, therefore, be completed soon after board fabrication. ENIG is the better choice for designs with very fine traces. ENIG is also better for thin boards because it is a relatively low-temperature process.
Both electrolytic soft gold, which would be a choice for designs that involve wire bonds in assembly, and electrolytic hard gold, which also supports wire-bonding and has advantages for sliding contacts, have a downside. To accomplish either finish requires the addition of buss bars on panels to electrically interconnect the copper features during the plating process, which afterward must be severed from the PCB circuits. Moreover, copper can remain exposed on trace sidewalls.
ENEPIG—short for electroless nickel, electroless palladium, immersion gold—is a somewhat more expensive surface finish that has nearly universal advantages. Nonetheless, my advice regarding surface finishes jibes with my advice regarding hybrid stack-ups: Consult your prospective manufacturer at the outset of your project, to make sure you don’t become invested too deeply to improve your design decisions.