Contents
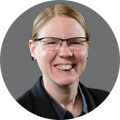
On-demand webinar
How Good is My Shield? An Introduction to Transfer Impedance and Shielding Effectiveness
by Karen Burnham
Jim Smith is bringing the Science of soldering seminar to Silicon Valley.
Since 2019, we have partnered with expert Jim Smith of Electronics Manufacturing Sciences to host soldering seminars..
Join us at Sierra Circuits on November 1st and 2nd, 2023 for a two-day hands-on soldering seminar.
You will learn:
- That soldering is mostly about chemistry
- 7 easy steps that guarantee perfect soldering
- The workmanship that all customers expect
- Why most of what you’ve been told about soldering is wrong
- A simple technique for ensuring that components never get much above the melting temperature of solder (most component failures are caused by overheating components)
- Why cosmetically “perfect” connections may not be reliable
- Why your company soldering techniques guarantee failure
- How to make a $90 soldering iron perform like an $800 iron
- Why “soldering” tin-plated parts is not actually soldering
- A simple, easy way to work with ground planes
- The fast, simple way to solder fine-pitch surface mount components
- How to replace any component — without damaging the PCB (and without any special equipment)
- The secret to easy lead-free soldering
- Why you can’t inspect-in reliability
- Why flux-cored solder isn’t suited to soldering
- Why the greatest challenges of the lead-free world have almost nothing to do with the solder alloy
- To never trust any lessons from the Internet
- The “industry standards” that are 100% wrong
- How to pick a true “no clean” flux (and avoid the false claims of flux manufacturers)
- And much, much more on how to achieve perfect soldering…