Contents
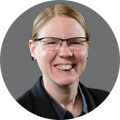
On-demand webinar
How Good is My Shield? An Introduction to Transfer Impedance and Shielding Effectiveness
by Karen Burnham
My previous posts have discussed specific soldering-related topics to help you achieve perfect soldering. Following are some soldering tips that, while very important, do not require hundreds of words each.
The 8 Must-Knows in Soldering
1. There’s no point in beautiful solder connections if the system is unreliable.
Cosmetically acceptable solder joints are important but only if they are achieved in a reliable fashion. Wetting issues can be eliminated by employing stronger fluxes, but the resulting ionic contamination can cause failures. And overheating components leads to premature failures.
Neither ionic contamination nor overheating can be seen but they can be deadlier than unattractive solder. Anyone can melt solder onto components; very few people do it reliably.
2. Class 3 “high reliability” is often fraudulent.
Class 3 products are not supposed to fail. There are endless requirements for things like record keeping and lead protrusion from circuit boards intended to minimize risk. And, of course, the inspection is endless.
But, ultimately, all of those precautions are meaningless because people with soldering irons fall back on touchup to enhance solder appearance. At soldering iron temperature, the solder will stick to oxides and give the appearance of reliable connections.
The solder itself passes inspection but the high heat inflicted on the component damages internal bonds and shortens the component’s life.
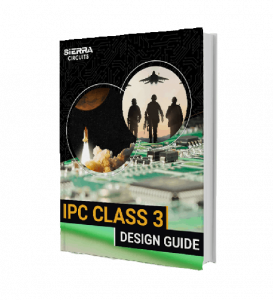
IPC Class 3 Design Guide
8 Chapters - 23 Pages - 35 Minute ReadWhat's Inside:
- IPC guidelines for manufacturing defects
- IPC standards for assembly processes
- Common differences between the classes
- IPC documents to set the level of acceptance criteria
Download Now
3. Reliability can’t be inspected.
A cosmetically defective solder connection is almost certainly unreliable. However, cosmetically acceptable alone proves nothing. True reliability requires doing the job right the first time, every time.
4. Constant temperature soldering irons can cause as much damage as irons with fluctuating temperatures.
The only way to prevent heat damage is by using the solder as a heat sink. However, solder training still teaches the application of heat and solder methods developed in the vacuum tube era to put as much heat as possible into the components.
What worked for soldering wires to vacuum tube sockets is disastrous for modern electronic components. (J-STD-001 still requires the use of heat sinks for soldering heat-sensitive components. When was the last time a heat sink was used in your production?)
5. Do not refer to “acid” flux.
Words matter. Using the correct terminology makes effective process management and troubleshooting more likely. When some people refer to plumbing flux as “acid” flux, they undermine the recognition that all fluxes used in electronics are acidic.
6. There’s no such thing as “cold” solder.
Again, words matter. The logical corrective action for “cold solder” is more heat, and that is the normal industry approach to the problem. But, unless the solder actually froze before completing its flow (as in a plated through-hole with heavy mass), what people call “cold solder” is just poor wetting.
IPC-A-610G, 1.8.2, defines “cold solder” as “A solder connection that exhibits poor wetting, and that is characterized by a grayish porous appearance. (This is due to excessive impurities in the solder, inadequate cleaning prior to soldering, and/or the insufficient application of heat during the soldering process.)” The British have a better term, “dry solder,” that accurately represents the underlying solderability issue.
7. “Pin holes” are not process indicators.
When the solder cools, it shrinks. The last area to freeze will pull back to eliminate stresses. This has nothing to do with the process; it’s just solder being solder. Yet IPC-A-610G (5.2.2) calls pin holes “process indicators” for Class 2 and 3.
Process indicators have no meaning beyond indicating the need for tightening the process parameters. Since no process change can prevent solder from being solder, there’s no logic in requiring documentation of the feature.
8. Perfect soldering is easy – 98% perfect is hard.
I began this series by telling you that “perfect soldering is simple.” So, it seems appropriate to end with the same theme. Soldering is actually a fairly straightforward science.
If we meet a small number of requirements imposed by nature, the solder will do the work and produce perfect connections. But we must comply with all the requirements.
A process that violates just one of nature’s requirements produces visually unacceptable connections; it is necessary to set other parameters to sub-optimal levels that compensate for the initial flawed setting. Perfect soldering really is easy, but it doesn’t happen by luck or guesswork.
Written by Jim Smith of Electronics Manufacturing Sciences, Inc.
Start the discussion at sierraconnect.protoexpress.com